Restoration Company Cooperation: Vacuum Protocols After Water or Fire Damage
When disaster strikes, proper vacuum protocols separate successful restorations from failures. Learn the industry’s best practices for cooperation in water and fire damage cleanup.
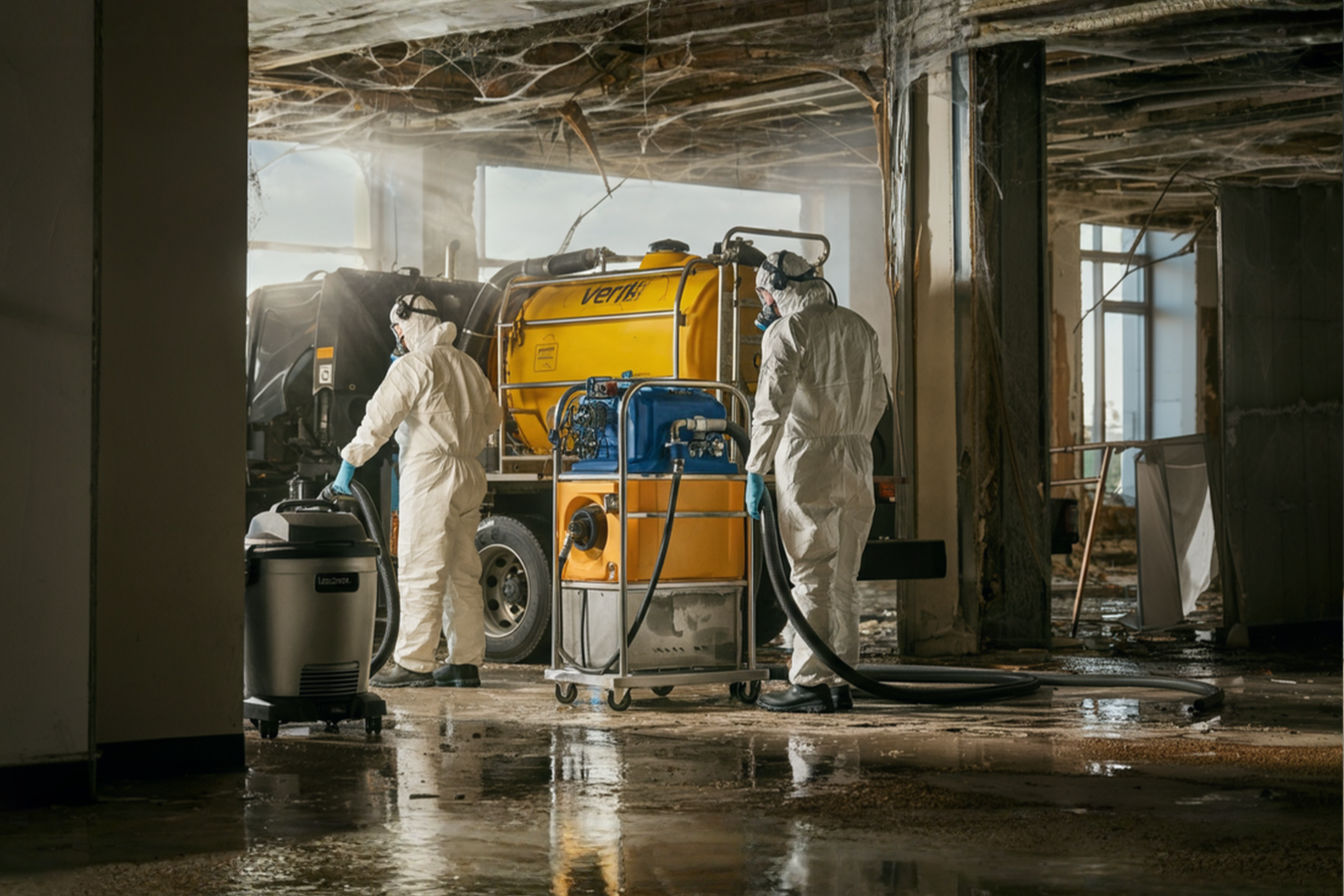
This post may contain affiliate links. If you make a purchase through these links, we may earn a commission at no additional cost to you.
When disaster strikes a property, whether through flooding or fire, proper vacuum protocols can mean the difference between successful restoration and long-term structural damage. Restoration companies across the industry increasingly recognize that cooperation in establishing and following standardized vacuum procedures leads to better outcomes for both clients and contractors.
The complexity of modern restoration projects often requires multiple specialized companies working together. Without clear vacuum protocols and effective cooperation strategies, teams risk cross-contamination, equipment damage, and project delays. This comprehensive guide explores the essential vacuum procedures that enable restoration companies to collaborate effectively while maintaining the highest standards of safety and efficiency.
Understanding Vacuum Requirements for Different Damage Types
Water Damage Vacuum Specifications
Water damage restoration presents unique challenges that demand specific vacuum capabilities. Professional extraction equipment must handle both standing water and absorbed moisture effectively. Most water removal projects require vacuums with minimum capacities of 12 gallons and airflow ratings of at least 100 CFM (cubic feet per minute). The key lies in selecting equipment that balances suction power with gentle operation to prevent further damage to sensitive materials.
Weighted extraction tools play a crucial role in carpet and upholstery restoration. These specialized attachments apply consistent pressure while vacuuming, ensuring thorough moisture removal without damaging fibers. Advanced restoration teams often utilize truck-mounted extraction systems for large-scale flooding, offering superior power and capacity compared to portable units.
Fire and Smoke Damage Requirements
Fire damage cleanup demands entirely different vacuum specifications focused on particulate capture and filtration. HEPA-rated vacuums capable of trapping particles as small as 0.3 microns become essential for removing toxic smoke residues and soot. These specialized units must feature sealed systems to prevent captured contaminants from escaping back into the environment.
Commercial fire restoration typically requires vacuums with multi-stage filtration systems. Primary filters capture larger debris, while secondary filters handle fine particulates, and final HEPA filters ensure complete air purification. Motor protection features become critical in these applications, as fire damage often includes corrosive substances that can quickly deteriorate standard equipment.
Combined Damage Scenarios
Properties affected by both water and fire damage present the most complex restoration challenges. Specialized vacuum systems must handle wet materials while maintaining strict filtration standards for smoke particles. This dual requirement often necessitates separate equipment for different phases of restoration or advanced hybrid systems designed specifically for combined damage scenarios.
Moisture meters and thermal imaging devices guide the vacuum process in these situations, helping technicians identify hidden pockets of damage. Proper sequencing becomes vital—removing standing water first, then addressing surface contaminants, and finally extracting deeply embedded moisture and particles.
Equipment Standards and Certifications
Industry-Approved Vacuum Types
The restoration industry recognizes specific vacuum categories suitable for different damage types. Wet/dry vacuums serve as the workhorses for water extraction, while HEPA vacuums handle hazardous particles. Submersible pumps and portable extractors supplement these primary tools for specialized applications.
Commercial-grade equipment differs significantly from residential models in durability, capacity, and filtration efficiency. Professional restoration requires vacuums rated for continuous operation, often featuring metal construction, reinforced hoses, and industrial-strength motors. These investments prove essential for meeting project timelines and quality standards.
Required Certifications and Testing
Legitimate restoration equipment undergoes rigorous testing and certification processes. The Institute of Inspection, Cleaning and Restoration Certification (IICRC) establishes baseline standards for vacuum performance and safety. HEPA vacuums must demonstrate 99.97% efficiency in capturing particles 0.3 microns or larger to receive certification.
Third-party testing laboratories verify equipment claims through standardized procedures. Air quality monitors measure post-vacuum environments to ensure proper particulate removal. Documentation of these certifications becomes crucial for insurance compliance and liability protection.
Compliance with IICRC Standards
IICRC standards provide comprehensive guidelines for vacuum usage in restoration projects. These protocols address everything from equipment selection to operational procedures and maintenance requirements. Certification requires both proper equipment and trained personnel who understand correct implementation.
Regular recertification ensures companies maintain current knowledge of evolving standards. Documentation systems track equipment compliance status, maintenance history, and operator certifications. These records prove invaluable during insurance audits and legal proceedings.
Vacuum Protocol Implementation
Initial Assessment Procedures
Effective vacuum protocols begin with thorough damage assessment. Restoration teams must evaluate the type, extent, and location of damage before selecting appropriate equipment. Moisture mapping identifies water-affected areas, while air quality testing determines particulate levels in fire-damaged spaces.
Documentation during assessment includes photographs, moisture readings, and contamination levels. This baseline data guides equipment selection and helps measure restoration progress. Experienced teams develop standardized assessment checklists to ensure consistent evaluation across projects.
Proper Equipment Selection
Equipment selection depends on multiple factors including damage type, affected materials, and project scale. Water extraction requires consideration of both surface and structural drying needs. Fire damage cleanup demands attention to particulate sizes and potential toxicity levels.
Teams must match vacuum capacity to project requirements while considering practical limitations like power availability and access restrictions. Portable units offer flexibility in tight spaces, while truck-mounted systems provide maximum power for large-scale operations.
Operational Guidelines
Standard operating procedures ensure consistent results across different projects and teams. These guidelines address equipment setup, operation sequencing, and monitoring protocols. Clear procedures reduce errors and improve efficiency while maintaining safety standards.
Teams establish communication protocols for coordinating vacuum operations across multiple work areas. Regular progress checks ensure proper coverage and prevent missed areas. Documentation requirements include work logs, equipment readings, and completion checklists.
Safety Standards and PPE Requirements
Vacuum operations expose workers to various hazards including electrical risks, water-borne pathogens, and toxic particulates. Proper personal protective equipment becomes non-negotiable in professional restoration work. Requirements typically include waterproof boots, gloves, eye protection, and respiratory gear appropriate to the specific hazards present.
Electrical safety protocols address grounding requirements, GFCI protection, and voltage compatibility. Teams receive training in proper lifting techniques to prevent injuries when moving heavy equipment. Regular safety audits ensure consistent compliance with established standards.
Cross-Company Cooperation Strategies
Communication Protocols
Effective cooperation between restoration companies requires clear communication channels and procedures. Project managers establish communication hierarchies and reporting structures at the outset of collaborative projects. Regular coordination meetings ensure all parties understand current progress and upcoming requirements.
Digital communication platforms enable real-time updates and documentation sharing. These systems maintain transparency while creating detailed records of decisions and actions. Standardized reporting formats ensure consistent information across different company systems.
Equipment Sharing Guidelines
Sharing specialized vacuum equipment between companies requires formal agreements addressing liability, maintenance, and usage protocols. Clear guidelines prevent disputes and ensure equipment returns in proper condition. Written agreements specify acceptable uses, cleaning requirements, and damage liability.
Equipment logs track usage across companies, including operators, project details, and maintenance performed. Regular inspections before and after sharing document equipment condition. These practices protect all parties while maximizing resource efficiency.
Documentation and Tracking Systems
Comprehensive documentation supports successful cooperation between restoration companies. Digital tracking systems monitor equipment location, usage history, and maintenance schedules across organizational boundaries. Standardized forms capture essential information consistently regardless of the company performing the work.
Cloud-based systems enable real-time access to documentation from any location. Version control ensures all parties work from current information. Access controls protect sensitive data while allowing necessary information sharing.
Liability and Insurance Considerations
Cooperative restoration projects require careful attention to liability issues. Insurance policies must address equipment damage, worker injuries, and property damage across company lines. Written agreements clarify responsibility for different aspects of vacuum operations.
Legal counsel reviews cooperation agreements to ensure adequate protection for all parties. Regular risk assessments identify potential liability issues before they become problems. Insurance documentation remains readily available to all project participants.
Contamination Prevention Measures
Between-Job Cleaning Protocols
Cross-contamination between job sites poses significant risks in restoration work. Thorough cleaning procedures between projects prevent the transfer of mold spores, bacteria, or chemical residues. These protocols address all vacuum components including hoses, attachments, and collection chambers.
Cleaning stations equipped with appropriate sanitizing agents ensure proper decontamination. Teams follow specific procedures for different contamination types, using appropriate cleaning agents and methods. Documentation tracks cleaning completion for quality control purposes.
Filter Replacement Guidelines
Filter management plays a crucial role in maintaining vacuum effectiveness and preventing contamination. Regular replacement schedules vary based on usage intensity and contamination levels encountered. Visual inspection protocols help identify filters requiring early replacement.
Proper disposal procedures ensure contaminated filters don’t create secondary hazards. Teams maintain adequate filter inventories to prevent project delays. Documentation tracks filter changes for maintenance records and warranty compliance.
Quarantine Procedures for Equipment
Equipment exposed to hazardous materials may require quarantine periods before reuse. Formal procedures govern the isolation, testing, and clearance of potentially contaminated vacuum equipment. Designated storage areas prevent contact between quarantined and clean equipment.
Testing protocols verify successful decontamination before equipment returns to general use. Documentation tracks quarantine status and test results. These measures protect workers and prevent project contamination issues.
Maintenance and Calibration Standards
Regular Maintenance Schedule
Preventive maintenance extends equipment life and ensures reliable performance. Scheduled maintenance includes motor inspections, seal checks, and electrical system testing. Daily maintenance tasks address basic cleaning and visual inspections.
Monthly and quarterly maintenance procedures involve more thorough examinations and component replacements. Annual servicing typically includes professional testing and calibration. Teams maintain detailed maintenance logs for warranty compliance and performance tracking.
Performance Testing Requirements
Regular performance testing verifies vacuum equipment meets required specifications. Airflow measurements, suction tests, and filtration efficiency checks ensure continued compliance with industry standards. Testing frequencies increase for equipment used in critical applications.
Standardized testing procedures ensure consistent results across different operators and locations. Documentation includes test results, corrective actions taken, and verification of restored performance. These records support quality assurance programs and regulatory compliance.
Record-Keeping Systems
Comprehensive maintenance records support equipment reliability and regulatory compliance. Digital maintenance management systems track service history, parts replacement, and performance data. These systems generate alerts for scheduled maintenance and track compliance metrics.
Easy access to maintenance records assists troubleshooting efforts and warranty claims. Historical data analysis identifies trends and potential issues before they cause failures. Regular audits ensure record-keeping accuracy and completeness.
Training and Certification
Required Technician Training
Proper vacuum operation requires more than basic equipment knowledge. Technicians must understand damage assessment, equipment selection, and safety procedures specific to restoration work. Initial training covers theoretical knowledge and hands-on experience with various vacuum types.
Advanced training addresses specialized situations like hazardous materials handling and confined space operations. Regular refresher courses maintain skill levels and introduce new technologies and procedures. Competency assessments verify training effectiveness.
Ongoing Education Programs
The restoration industry continually evolves with new technologies and techniques. Structured continuing education programs keep technicians current with industry developments. These programs cover equipment advances, regulatory changes, and improved procedures.
Online learning platforms provide flexible training options for busy professionals. Industry conferences and workshops offer hands-on experience with new equipment. Certification renewal requirements encourage ongoing professional development.
Company Certification Requirements
Beyond individual technician certification, companies must maintain organizational credentials. These certifications verify proper procedures, equipment, and training programs are in place. Regular audits ensure continued compliance with industry standards.
Documentation systems track company certifications, training records, and equipment compliance status. Quality management programs support continuous improvement efforts. These organizational certifications build client confidence and support marketing efforts.
Common Challenges and Solutions
Equipment Compatibility Issues
Different restoration companies often use various equipment brands and models. Compatibility challenges arise when connecting different systems or sharing components. Standardized adapters and universal connection systems help overcome these issues.
Technical specifications databases assist teams in identifying compatible equipment combinations. Cross-training on multiple equipment brands improves operational flexibility. Regular equipment audits identify potential compatibility issues before they impact projects.
Resource Allocation Problems
Multiple simultaneous projects can strain available vacuum resources. Strategic planning and resource sharing agreements prevent equipment shortages during peak periods. Centralized scheduling systems track equipment availability across companies.
Rental agreements with equipment suppliers provide backup capacity during busy periods. Maintenance scheduling considers project demands to minimize equipment downtime. Regular capacity assessments ensure adequate resources for anticipated workloads.
Quality Control Measures
Maintaining consistent quality across different teams and companies requires robust control measures. Standardized checklists, inspection protocols, and performance metrics ensure uniform results. Third-party quality audits provide objective assessments of work quality.
Digital quality management systems track performance metrics and identify improvement opportunities. Regular team meetings address quality issues and share best practices. Customer feedback systems provide valuable input for quality improvement efforts.
Conclusion
Success in restoration work depends heavily on proper vacuum protocols and effective cooperation between companies. Well-defined procedures, appropriate equipment, and trained personnel form the foundation of successful restoration projects. Companies that prioritize these elements consistently deliver superior results while maintaining safety and efficiency.
The future of restoration vacuum technology promises continued advancement in filtration efficiency, automation, and data integration. Smart vacuums with built-in sensors and connectivity features will further improve documentation and quality control. Companies that embrace these technologies while maintaining strong cooperation protocols will lead the industry forward.
Investment in proper vacuum protocols represents more than regulatory compliance—it demonstrates commitment to quality, safety, and professional excellence. As the restoration industry continues to evolve, companies that master these fundamental practices will build lasting reputations for reliability and expertise.