Vacuum Cleaner Circuit Protection: Safeguards That Prevent Motor Burnout
Modern vacuum cleaners use sophisticated circuit protection systems to prevent costly motor burnout. Learn how these safeguards work and how proper maintenance can extend your vacuum’s lifespan.
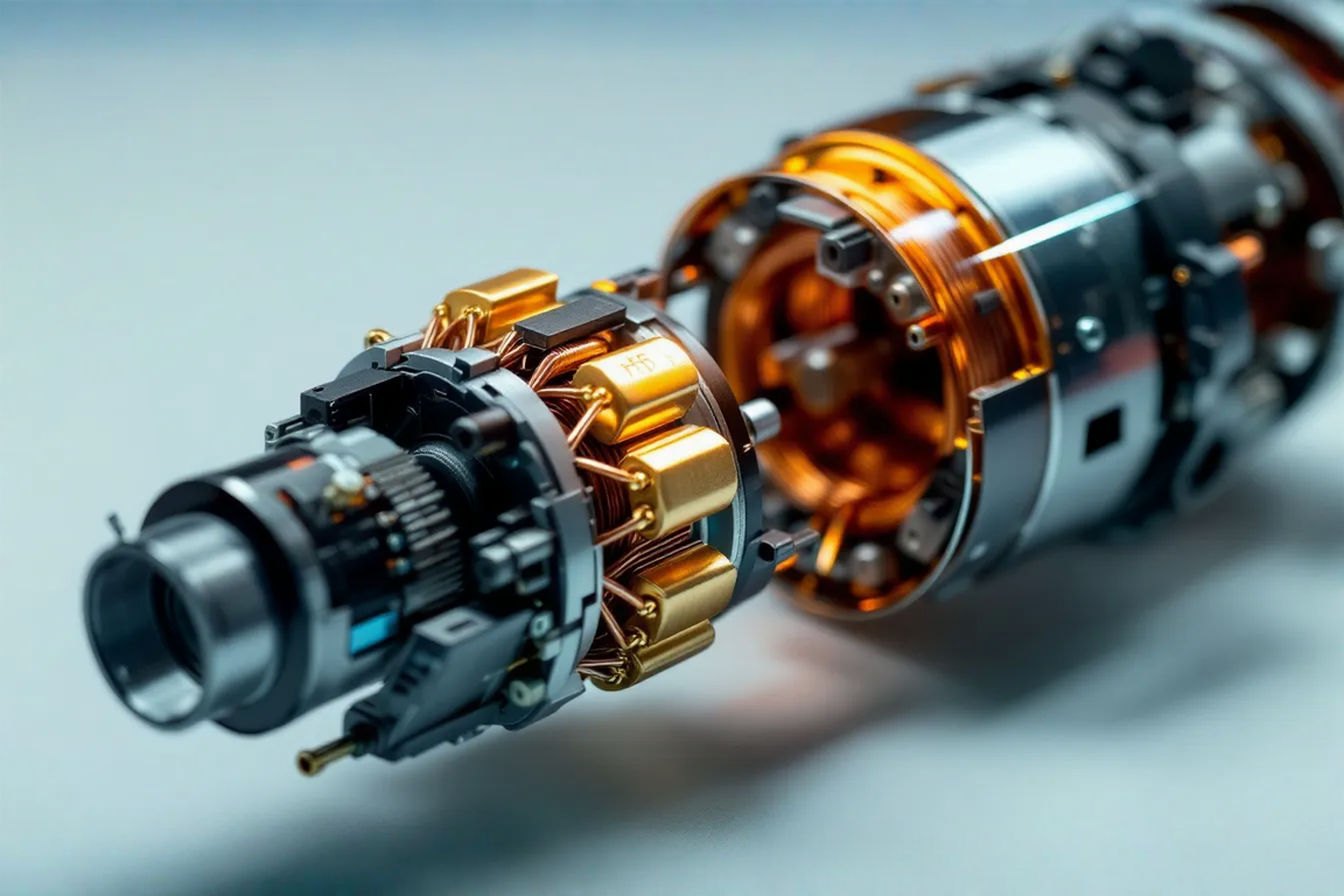
This post may contain affiliate links. If you make a purchase through these links, we may earn a commission at no additional cost to you.
When your vacuum cleaner suddenly stops working, the culprit is often a burnt-out motor. What many homeowners don’t realize is that modern vacuum cleaners come equipped with sophisticated circuit protection systems specifically designed to prevent this costly failure. These safeguards represent the thin line between a minor inconvenience and a major expense.
Studies show that electrical issues account for approximately 60% of vacuum cleaner failures, with motor burnout being the most expensive type of damage. While a replacement motor can cost between $80-$150, the protection components that prevent burnout typically cost just $5-$20. This stark contrast highlights why understanding circuit protection isn’t just for engineers—it’s essential knowledge for any vacuum owner.
Vacuum cleaner circuit protection encompasses multiple systems working together to monitor and regulate electrical conditions. These systems act as vigilant guardians, standing ready to interrupt power before damage occurs. From simple thermal fuses to complex microprocessor-controlled circuits, these protective measures have evolved significantly over decades of engineering innovation.
In this comprehensive guide, we’ll explore the various protection systems that keep your vacuum running safely, explain how they function, and provide practical maintenance advice to extend the life of your appliance. Whether you’re troubleshooting a problem, considering a new purchase, or simply curious about how these everyday appliances safeguard themselves, you’ll find valuable insights in the sections that follow.
Understanding Vacuum Cleaner Motors and Electrical Systems
Before diving into protection systems, it’s helpful to understand what they’re protecting. The heart of every vacuum cleaner is its motor, and several types are commonly used across different models.
Types of Motors Used in Vacuum Cleaners
Universal motors are the workhorses of most household vacuum cleaners. These motors can operate on both AC and DC power, making them incredibly versatile. They feature a wound stator (the stationary part) and a wound armature (the rotating part) with brushes that transfer electrical current. While universal motors deliver excellent power-to-weight ratios and high speed capabilities, their brush design makes them susceptible to wear over time.
Brushed DC motors are found in some battery-operated vacuums. They work through electromagnetic attraction and repulsion, using carbon brushes to transfer electricity to the rotating commutator. These motors are efficient for their size but require regular maintenance as the brushes wear down with use.
Brushless DC motors represent newer technology found in premium and modern cordless vacuums. As their name suggests, they eliminate the need for brushes by using electronic commutation instead of mechanical commutation. This design significantly reduces friction and heat generation, resulting in longer lifespans and greater reliability—but at a higher cost.
Induction motors occasionally appear in high-end or commercial vacuum cleaners. These motors have no brushes and fewer moving parts, making them exceptionally durable. However, their heavier weight and higher cost limit their use in household models.
Typical Electrical Requirements and Specifications
Most household vacuum cleaners operate on standard 120V AC power in the United States (or 220-240V in many other countries) and draw between 5-12 amps of current. This translates to approximately 600-1440 watts of power consumption. Commercial models often require more power, sometimes necessitating specialized outlets.
The motor’s power needs translate directly to suction capability, which manufacturers often measure in air watts, water lift (inches of water column), or CFM (cubic feet per minute of airflow). Higher numbers generally indicate stronger cleaning power but also greater electrical demands on protection systems.
Common Electrical Stress Points and Failure Modes
Vacuum cleaner motors face several challenging conditions that can lead to failure:
- Start-up surge: When first powered on, motors draw significantly more current than during normal operation—sometimes 3-5 times their running current. This “inrush current” creates momentary stress on components.
- High operating temperatures: Vacuum motors typically run at 140-180°F (60-82°C) during normal operation. Any restriction in cooling airflow can quickly push temperatures into dangerous territory.
- Dust contamination: Despite filters, fine dust particles eventually infiltrate the motor chamber, coating components and acting as an insulating blanket that traps heat.
- Brush wear: In universal and brushed DC motors, carbon brushes gradually wear down, changing the electrical characteristics and potentially causing arcing.
- Power fluctuations: Household voltage isn’t always steady, and variations can stress motor components over time.
How Motor Burnout Occurs and Its Signs
Motor burnout happens when the insulation on copper windings breaks down due to excessive heat. This creates short circuits between windings, drawing more current and generating even more heat in a destructive cycle that ultimately renders the motor useless.
Early warning signs include:
- Unusual odors: A burning smell often precedes complete failure
- Decreased suction: Weakening performance as the motor struggles
- Strange noises: Grinding, whining, or irregular sounds
- Excessive heat: The exterior of the vacuum becomes unusually hot
- Intermittent operation: The vacuum works, then stops, then works again
If you notice these symptoms, it’s likely that protection systems are already engaging periodically, indicating that larger problems may be developing.
Primary Causes of Vacuum Cleaner Motor Burnout
Understanding what causes motor burnout helps explain why specific protection mechanisms are necessary. Several common factors contribute to premature motor failure:
Overheating Due to Restricted Airflow
Vacuum cleaner motors rely on a continuous flow of air not just for suction but for cooling the motor itself. When this airflow becomes restricted, operating temperatures rise dramatically. A blocked hose, full dust bag, or clogged filter can raise motor temperature by 30-50°F in just minutes.
In the simplest terms, most vacuum motors are designed to be air-cooled. As air passes through the system, it draws heat away from the motor. Without this cooling effect, temperatures quickly reach levels that damage insulation on motor windings.
Technical detail: Motor windings are typically wrapped with thin enamel insulation rated for specific temperature ranges (Class A: 221°F/105°C, Class B: 266°F/130°C, etc.). When temperatures exceed these ratings, the insulation begins to soften, crack, and eventually fail altogether.
Power Surges and Voltage Fluctuations
Power surges occur when voltage temporarily increases beyond normal levels. These can be caused by lightning strikes, power outages followed by restoration, or switching of large appliances on the same circuit. Even brief surges can damage sensitive components.
Voltage fluctuations happen more gradually but can be equally damaging. When voltage drops (brownouts), motors draw more current to maintain power, generating additional heat. When voltage exceeds normal levels, components may receive more power than they’re designed to handle.
Technical detail: Universal motors are particularly sensitive to voltage changes. A 10% increase in voltage can lead to a 20% increase in current draw and significantly higher operating temperatures.
Mechanical Jamming and Blockages
When the rotating components in a vacuum cleaner become jammed—perhaps by a sock being sucked into the brushroll or a pencil lodged in a crevice tool—the motor continues to draw power while unable to rotate. This “locked rotor” condition creates extreme heat very quickly.
Without movement, the motor’s cooling system becomes ineffective while electrical energy continues to convert to heat rather than mechanical motion. In as little as 10-15 seconds, temperatures can reach damaging levels.
Technical detail: A locked rotor can cause current draw to increase by 5-8 times normal operating levels. This generates heat in proportion to the square of the current (P = I²R), creating a rapid temperature spike.
Continuous Operation Beyond Design Limits
Most household vacuum cleaners are designed for intermittent use—typically 30-60 minutes at a time with cooling periods between sessions. Extended continuous operation pushes components beyond their design parameters, especially in less expensive models.
During prolonged use, heat gradually builds up in motor components faster than it can dissipate, eventually reaching critical levels. This is particularly problematic in smaller, more compact vacuum designs where airflow around the motor may be limited.
Dust and Debris Contamination of Electrical Components
Despite manufacturers’ best efforts to seal motor chambers, microscopic dust eventually penetrates these barriers. As dust accumulates on electrical components, it:
- Acts as thermal insulation, trapping heat
- Absorbs moisture, potentially causing short circuits
- Creates additional friction on moving parts
- Interferes with electrical contacts
Technical detail: Carbon dust from wearing brushes is particularly problematic as it conducts electricity, potentially creating paths for current where none should exist.
Aging and Wear of Components
Even with perfect maintenance, vacuum components naturally degrade over time:
- Motor bearings lose lubrication and develop friction
- Capacitors gradually lose capacity
- Insulation becomes brittle
- Electrical contacts develop resistance
- Seals harden and become less effective
This natural aging process makes older vacuums more susceptible to burnout, explaining why protection systems often activate more frequently in aging appliances.
Thermal Protection Systems
Thermal protection represents the first line of defense against motor burnout. These systems monitor temperature and interrupt power when unsafe conditions are detected.
Thermal Fuses and How They Function
Thermal fuses are simple, one-time protection devices that permanently break an electrical connection when a specific temperature is reached. Typically small cylindrical components wired in series with the motor, they contain a fusible link that melts when heated beyond its rating.
In simplest terms, thermal fuses act like the weakest link in a chain—they’re designed to fail safely before more expensive components can be damaged.
Technical detail: Most vacuum cleaner thermal fuses are rated between 257°F (125°C) and 291°F (144°C), depending on the motor design. Once the fusible link melts, the circuit is permanently opened and the fuse must be replaced—it cannot reset itself.
Resettable Thermal Switches
Unlike one-time thermal fuses, resettable thermal switches (sometimes called thermal cutouts or thermal protectors) automatically restore power once temperatures return to safe levels. These devices use a bimetallic strip or disc that bends when heated, breaking the circuit.
The key advantage is their ability to return to normal operation without replacement parts. When the temperature drops, the bimetallic element returns to its original position, reconnecting the circuit.
Technical detail: Bimetallic elements consist of two different metals bonded together with different thermal expansion rates. When heated, one metal expands more than the other, causing the element to bend and trigger the switch mechanism.
Thermal Sensors and Electronic Monitoring
Modern premium vacuums often employ sophisticated thermal monitoring systems using thermistors or other temperature-sensitive components. These continuously measure temperature and feed data to control circuits.
Rather than simply cutting power completely, electronic systems can take graduated actions:
- Reducing power to the motor temporarily
- Activating additional cooling
- Triggering warning lights or notifications
- Initiating an orderly shutdown
Technical detail: Negative Temperature Coefficient (NTC) thermistors decrease in resistance as temperature increases, allowing the control circuit to precisely measure temperature changes. This enables more sophisticated protection algorithms than simple on/off protection.
Materials Used in Thermal Protection
The reliability of thermal protection depends heavily on the materials used:
- Fusible links typically use alloys like bismuth, lead, tin, and cadmium with precise melting points
- Bimetallic elements commonly combine brass or copper with iron or invar
- Contact materials must resist arcing and corrosion, often using silver alloys
- Housing materials need to withstand high temperatures without deforming
These specialized materials ensure consistent operation over thousands of cycles and years of service.
Temperature Thresholds and Ratings
Protection systems activate at carefully calculated thresholds:
- Warning threshold: Some advanced systems begin preventative measures at approximately 200°F (93°C)
- Thermal switch activation: Typically occurs between 230-260°F (110-127°C)
- Thermal fuse melting: Usually set between 257-291°F (125-144°C)
- Catastrophic damage: Motor winding insulation begins failing around 284-320°F (140-160°C), depending on insulation class
The small margin between protection activation and actual damage highlights the importance of properly functioning thermal safeguards.
Overcurrent Protection Devices
While thermal protection guards against excessive heat, overcurrent protection specifically prevents damage from excessive electrical current flow.
Circuit Breakers Specific to Vacuum Cleaners
Vacuum cleaner circuit breakers are specialized versions of the familiar devices found in your home’s electrical panel. They automatically interrupt current flow when it exceeds safe levels but can be reset once the issue is resolved.
Unlike home circuit breakers designed to protect wiring, vacuum-specific breakers are calibrated for the precise needs of motor protection, with trip points much closer to normal operating currents.
Technical detail: Many vacuum circuit breakers use a combination of electromagnetic and thermal triggering mechanisms. The electromagnetic portion responds instantly to severe overloads while the thermal element reacts more slowly to sustained moderate overloads.
Fuses and Their Ratings
Electrical fuses in vacuum cleaners contain a metal wire or strip that melts when current exceeds its rating, permanently breaking the circuit. They provide simple, reliable protection but must be replaced after activation.
Fuse ratings are carefully matched to the vacuum’s design specifications. For example, a vacuum that normally draws 8 amps might use a 10-amp fuse, providing just enough headroom for normal operation while protecting against dangerous conditions.
Technical detail: Time-current characteristics are crucial for proper fuse selection. The curve illustrates how quickly a fuse will blow at different levels of overcurrent. For motors, this curve must accommodate normal start-up surges while still providing protection.
Current Limiting Devices
Some modern vacuums incorporate current limiting devices that actively restrict current rather than simply interrupting it. These components can:
- Absorb excess energy during brief surges
- Reduce available current during overload conditions
- Provide more nuanced protection than simple on/off mechanisms
Technical detail: Positive Temperature Coefficient (PTC) resistors increase their resistance dramatically when heated by excessive current flow. This self-limiting behavior reduces current without completely interrupting it, allowing for potential automatic recovery.
Electronic Current Monitoring Systems
Premium vacuums increasingly use electronic current monitoring, where microprocessors continuously measure current flow and can take various actions based on the severity and duration of abnormal conditions.
These sophisticated systems can distinguish between normal variations (like when the vacuum transitions from carpet to bare floor) and genuinely problematic conditions requiring intervention.
Technical detail: Hall effect sensors can measure current without introducing resistance into the circuit. They detect the magnetic field generated by current flow, allowing precise non-contact measurement that can be processed by control circuits.
Difference Between Slow-Blow and Quick-Acting Protection
Protection devices are carefully chosen based on the characteristics of the protected equipment:
Quick-acting (fast-blow) protection responds almost instantly to overcurrent conditions. These are used to protect sensitive electronic components that can be damaged in milliseconds.
Slow-blow (time-delay) protection allows temporary current spikes but responds to sustained overloads. These are ideal for motor protection since they accommodate the high inrush current at startup without nuisance tripping.
Technical detail: Time-delay features can be implemented through various mechanisms including thermal inertia, magnetic damping, or dual-element designs combining quick and delayed response elements.
Surge Protection Mechanisms
Power surges represent a significant threat to vacuum cleaner electronics. These brief but intense voltage spikes can destroy components instantly without adequate protection.
Metal Oxide Varistors (MOVs)
Metal oxide varistors are among the most common surge protection components in household appliances, including vacuum cleaners. These ceramic semiconductor devices act like electrical pressure relief valves.
Under normal operating conditions, MOVs have high resistance and minimal impact on the circuit. When voltage exceeds their rating, their resistance drops dramatically, diverting excess energy away from sensitive components.
Technical detail: MOVs are made from zinc oxide grains separated by intergranular boundaries. These boundaries prevent current flow at normal voltages but break down under high voltage conditions, creating conductive paths that shunt surge current.
Transient Voltage Suppressors
Transient voltage suppressors (TVS) are specialized semiconductor devices similar to Zener diodes but designed specifically for surge protection. They react faster than MOVs and provide more precise protection levels.
TVS components are particularly important in protecting the sophisticated electronics found in modern “smart” vacuums with digital controls and wireless capabilities.
Technical detail: TVS diodes operate by avalanche breakdown, a phenomenon where high voltage causes a sudden increase in current flow through the semiconductor junction. This diverts energy away from protected circuits within nanoseconds.
Surge Protection Circuits
Beyond individual components, many premium vacuum cleaners incorporate complete surge protection circuits that combine multiple protective elements:
- First stage: Suppresses extremely high voltage spikes
- Second stage: Filters remaining surge energy
- Final stage: Provides precise protection for sensitive electronics
These multi-layered approaches offer significantly better protection than single-component solutions.
Technical detail: Coordinated protection stages use components with progressively lower voltage ratings and faster response times, resulting in an overall system that can handle severe surges while maintaining precise protection thresholds.
Isolation Transformers
Some high-end commercial vacuum cleaners include isolation transformers that physically separate the vacuum’s electrical system from the power supply. These devices transfer power through magnetic coupling rather than direct electrical connection.
Isolation provides excellent protection against surges and other power anomalies, though size, weight, and cost considerations limit their use primarily to commercial equipment.
Technical detail: Isolation transformers block direct current paths between primary and secondary circuits while allowing alternating current to transfer through magnetic induction. This prevents many types of electrical disturbances from reaching sensitive equipment.
EMI/RFI Protection Components
Electromagnetic interference (EMI) and radio frequency interference (RFI) can affect vacuum cleaner operation and potentially cause damage over time. Protection components include:
- Ferrite cores or beads that absorb high-frequency noise
- Filter capacitors that shunt interference to ground
- Shielded cables that prevent signal radiation and reception
These components not only protect the vacuum but also prevent it from interfering with other electronics in your home.
Technical detail: Common mode chokes use paired windings on a shared magnetic core to block interference that appears on both power conductors simultaneously while allowing normal differential current flow.
Advanced Protection Systems in Modern Vacuums
As vacuum cleaners have evolved from simple mechanical devices to sophisticated appliances, their protection systems have become increasingly advanced. Modern premium models incorporate protection mechanisms that would have seemed like science fiction just decades ago.
Microprocessor-Controlled Protection Circuits
Microprocessor-controlled protection represents the cutting edge of vacuum cleaner safeguards. These systems use dedicated processing chips to monitor multiple parameters simultaneously:
- Current draw across different components
- Temperature at various points
- Motor speed and performance
- Airflow characteristics
- Power quality and stability
Based on sophisticated algorithms, the microprocessor can identify potential problems before they cause damage and take appropriate preventative actions.
Technical detail: Modern protection microcontrollers often operate at 16-32MHz and can sample analog inputs thousands of times per second. This allows them to detect anomalies within milliseconds and respond with precise countermeasures tailored to the specific condition.
Smart Power Management Systems
Smart power management goes beyond simple protection by actively optimizing how power is delivered to various vacuum components. These systems can:
- Apply just the right amount of power based on surface type
- Adjust motor speed to maintain optimal suction with minimal energy use
- Redistribute power between motors when multiple motors are present
- Implement soft-start functions that reduce wear and tear
These sophisticated control systems not only prevent damage but also extend component lifespan through more efficient operation.
Technical detail: Pulse-width modulation (PWM) controllers rapidly switch power on and off at varying duty cycles to precisely control the average power delivered to motors. This allows for infinitely variable speed control rather than the simple high/medium/low settings of older designs.
Self-Diagnostic Capabilities
Modern vacuums increasingly include self-diagnostic systems that can identify potential issues before they cause failure. These capabilities include:
- Error code generation for specific fault conditions
- Maintenance reminders based on actual use patterns
- Performance monitoring to detect gradual degradation
- Communication of specific issues through display panels or smartphone apps
By identifying and communicating problems early, these systems help prevent catastrophic failures and simplify maintenance.
Technical detail: Self-diagnostics often utilize parameter baseline comparisons, where the system learns “normal” operating characteristics during initial use, then continuously compares current performance against these baselines to detect deviations.
Soft-Start Mechanisms to Reduce Inrush Current
Soft-start mechanisms address one of the most stressful moments in a motor’s operation—startup. Rather than applying full voltage instantly, these systems gradually ramp up power over fractions of a second.
Benefits include:
- Reduced electrical stress on motor windings
- Lower mechanical stress on gears and bearings
- Decreased surge current demand from household wiring
- Extended brush life in traditional motors
Technical detail: NTC (Negative Temperature Coefficient) thermistors are sometimes used as simple soft-start devices. Initially cold, they have high resistance that limits inrush current. As current flows, they quickly heat up and their resistance drops, allowing normal operation.
Brushless Motor Electronic Controllers
The shift toward brushless motors in premium vacuums has introduced sophisticated electronic controllers that provide inherent protection advantages:
- Precise control of motor speed and torque
- Constant monitoring of electrical parameters
- Ability to detect and compensate for obstructions
- Elimination of brush wear and associated failures
These controllers not only drive the motor but continuously protect it through active management rather than passive protection.
Technical detail: Brushless motor controllers use Hall effect sensors or back-EMF detection to precisely determine rotor position and optimize commutation timing. This allows the controller to detect abnormal conditions like stalls or binding almost instantly.
Circuit Protection in Different Vacuum Types
Different vacuum cleaner designs face unique challenges that require specialized protection approaches.
Upright Vacuum Protection Systems
Upright vacuums commonly incorporate protection features specifically designed for their configuration:
- Brushroll jam sensors that detect when the roller becomes obstructed
- Belt protection systems that prevent motor damage if the belt breaks or slips
- Thermal protection positioned near the motor’s hottest points
- Airflow sensors that detect bag fullness or blockages
The compact design of uprights, with motors often positioned close to dust collection systems, creates particular thermal management challenges requiring carefully positioned protection devices.
Technical detail: Many uprights use sacrificial drive belts that are designed to slip or break before damage can occur to the more expensive motor. This mechanical protection complements the electrical safeguards.
Canister Vacuum Safeguards
Canister vacuums separate the motor unit from the cleaning head, allowing for different protection approaches:
- Dual thermal protection (one near the motor, one monitoring exhaust temperature)
- More sophisticated cord management systems to prevent cord damage
- Separate protection for power nozzle attachments
- Water level detection in wet/dry models
The separate motor housing typically allows for better airflow and cooling, but often requires protection against water intrusion as the canister may be pulled into wet areas.
Technical detail: Many canister vacuums feature double-insulated construction that eliminates the need for a ground wire. This requires specialized protection approaches since ground fault detection is not possible.
Robotic Vacuum Protection Circuits
Robotic vacuums face unique challenges and incorporate specialized protection:
- Battery management systems that prevent overcharging and over-discharging
- Collision and fall sensors that prevent mechanical damage
- Multiple low-voltage protection circuits for various subsystems
- Thermal management for compact, enclosed designs
- Self-rescue protocols when stuck or entangled
The sophisticated electronics in robotic vacuums require multilayered protection strategies far more complex than traditional models.
Technical detail: Robot vacuums often employ dedicated power management ICs (integrated circuits) that handle multiple protection functions simultaneously, monitoring battery parameters, motor current, and system voltage while communicating with the main processor.
Central Vacuum System Protection
Central vacuum systems have unique requirements due to their permanent installation and higher power:
- Higher-capacity thermal protection due to longer potential run times
- Line voltage monitoring to protect against household power issues
- Specialized motor protection for continuous-duty motors
- Airflow monitoring systems that detect blockages in built-in piping
Their permanent installation often justifies more expensive protection components since replacement is more complicated than with portable units.
Technical detail: Many central vacuum systems use two-stage protection: a resettable thermal switch for normal overheating conditions and a non-resettable thermal fuse as backup protection. This provides convenience for minor issues while ensuring safety for major failures.
Commercial/Industrial Vacuum Protection Differences
Commercial vacuums face more demanding use patterns and incorporate enhanced protection:
- Heavy-duty thermal protection rated for extended duty cycles
- More robust filtration monitoring to protect motors from industrial debris
- Enhanced surge protection for inconsistent workplace power
- Specialized protection for hazardous environment models (HEPA, explosion-proof)
These machines often cost substantially more than household models, justifying more sophisticated protection systems to safeguard the investment.
Technical detail: Many commercial vacuums incorporate hour meters similar to those in other industrial equipment. These help maintain proper maintenance schedules and can be integrated with protection systems to require service at appropriate intervals.
DIY Maintenance to Prevent Circuit Issues
Proper maintenance dramatically reduces the risk of protection system activation and extends vacuum life.
Regular Cleaning of Air Paths and Filters
Nothing impacts vacuum motor life more than airflow maintenance. Regular attention to cleaning pathways helps prevent the most common cause of protection system activation:
- Empty dust containers when they reach 2/3 capacity, not just when completely full
- Replace disposable bags before they’re completely full
- Wash or replace filters according to manufacturer guidelines
- Check and clear hoses and tubes monthly
- Clean brush rolls weekly to remove hair and thread buildup
Technical detail: A partially clogged filter can reduce airflow by 30-50%, dramatically increasing motor temperature and power consumption. Even invisible dust accumulation on filters significantly impacts performance.
Checking Cord Integrity
The power cord represents both a safety concern and a potential cause of motor damage:
- Inspect the entire length for cuts, cracks, or abrasions
- Check for overheating at the plug
- Ensure proper winding/storage to prevent internal wire breakage
- Replace damaged cords immediately—never tape or attempt repairs
- Use cord guards or protectors for commercial environments
Technical detail: Damaged cords can cause voltage drops that force motors to draw higher current, creating extra heat. A seemingly minor cord issue can lead to persistent undervoltage that stresses protection systems.
Monitoring for Warning Signs of Impending Failure
Early intervention can prevent complete failure. Watch for:
- Unusual odors: Electrical smells often precede protection activation
- New or different sounds: Grinding, whining, or buzzing often indicates problems
- Intermittent operation: Protection systems cycling on and off
- Reduced performance: Lower suction may indicate impending issues
- Unusual vibration: May signal mechanical problems that will lead to electrical issues
Technical detail: Many electrical components emit specific odors when overheating but before failing completely. Capacitors often smell like fish, while motor windings typically produce a distinct “hot electrical” odor.
Proper Usage Practices to Prevent Overheating
How you use your vacuum significantly impacts its electrical health:
- Allow cooling breaks during extended cleaning sessions (15 minutes use, 5 minutes rest)
- Start with clean filters and empty containers for major cleaning jobs
- Use appropriate power settings for the task (full power isn’t always necessary)
- Avoid vacuuming wet materials with standard vacuums
- Don’t continue use when suction decreases substantially
Technical detail: Motor temperature typically rises 15-30°F during the first 10 minutes of operation before stabilizing. Extended use beyond 30 minutes can push temperatures another 10-15°F higher, potentially approaching protection thresholds.
Storage Recommendations to Prevent Circuit Damage
Even when not in use, vacuums can suffer damage:
- Store in clean, dry environments away from extreme temperatures
- Avoid storage in areas with high humidity that can degrade insulation
- Keep away from areas with chemical fumes that can corrode components
- Ensure cords are properly wound without tight bends
- Follow manufacturer recommendations for battery maintenance in cordless models
Technical detail: Humidity above 80% can lead to moisture absorption in motor windings and electrical components. Over time, this moisture accelerates insulation breakdown and corrosion of internal components.
Troubleshooting Circuit Protection Problems
When protection systems activate, understanding how to diagnose the issue prevents repeated problems.
Identifying When Protection Systems Have Activated
Different protection systems display distinct symptoms:
- Thermal cutout activation: Vacuum stops but lights may remain on; unit may restart after cooling period (15-30 minutes)
- Fuse failure: Complete loss of power with no lights or signs of life
- Circuit breaker trip: Clicking sound, complete power loss, may have reset button
- Electronic protection: Error codes, warning lights, or specific patterns of operation
Modern vacuums often provide specific indications through blinking lights or digital displays that can be decoded using the owner’s manual.
Technical detail: Some thermal protection systems make a distinctive clicking sound when they activate and again when they reset. This sound comes from the bimetallic disc snapping between its curved positions.
Testing Fuses and Circuit Breakers
Basic testing can often identify protection issues:
- Multimeter testing: Using a continuity setting to check if fuses are intact
- Visual inspection: Some thermal fuses have clear windows showing the fusible link
- Reset testing: Attempting to reset circuit breakers after sufficient cooling
- Resistance measurements: Comparing readings to manufacturer specifications
Technical detail: When testing thermal fuses, measurements should be taken at room temperature. A good thermal fuse will show near-zero resistance (0.1-1.0 ohms), while a blown fuse will show infinite resistance (open circuit).
Diagnosing Thermal Cutout Issues
When thermal protection repeatedly activates, systematic diagnosis is essential:
- Check for airflow restrictions first—this is the most common cause
- Inspect for mechanical binding in motors or brushrolls
- Test for proper voltage at the outlet
- Look for dust accumulation on motor components
- Measure ambient temperature—high room temperatures reduce cooling margins
Repeated thermal cutout activation always indicates an underlying problem that will eventually lead to permanent damage if not addressed.
Technical detail: Thermal cutouts are typically designed to activate when motor temperature reaches approximately 230-260°F (110-127°C). This provides a safety margin below the temperature where insulation damage begins (around 284-320°F/140-160°C for most motor insulation classes).
When to Replace Protection Components
Knowing when to replace protection devices prevents damage and ensures safety:
- One-time thermal fuses must always be replaced after activation
- Circuit breakers that become difficult to reset or that trip at progressively lower loads should be replaced
- Thermal cutouts that activate with increasing frequency may be weakening
- Electronic protection systems that display error codes should be serviced according to manufacturer guidelines
Always replace protection components with identical or manufacturer-recommended parts. Using components with incorrect ratings can lead to insufficient protection or nuisance tripping.
Technical detail: Protection components are selected based on specific time-current curves that match motor characteristics. Substituting a “similar” component with different activation timing can leave motors vulnerable during critical startup periods or cause unnecessary shutdowns during normal operation.
Professional vs. DIY Repair Considerations
Some repairs are DIY-friendly while others require professional service:
Appropriate for DIY repair:
- Cleaning or replacing filters and airways
- Replacing accessible thermal fuses (with proper testing)
- Resetting circuit breakers
- Basic cord repairs (replacing plugs)
- Simple mechanical maintenance
Best left to professionals:
- Internal electronic component replacement
- Motor rebuilding or replacement
- Circuit board repair
- Modifications to existing protection systems
- Repairs involving sealed motor units
Technical detail: Modern vacuum cleaners increasingly use surface-mount components and multi-layer circuit boards that require specialized equipment for proper repair. Amateur soldering attempts often cause additional damage to these sensitive components.
Future Trends in Vacuum Cleaner Circuit Protection
Protection systems continue to evolve, with several emerging trends pointing toward the future of vacuum cleaner safety and reliability.
Integration with Smart Home Systems
Smart home integration is transforming how vacuum cleaners monitor and protect themselves:
- Communication with home energy management systems to schedule operation during optimal power conditions
- Integration with home automation to prevent operation during known power quality issues
- Remote monitoring capabilities that alert owners to potential problems
- Usage pattern analysis that suggests preventative maintenance
- Cloud-based diagnostics that compare performance to similar units
Technical detail: Protocols like Matter, Zigbee, and Wi-Fi allow modern vacuums to communicate bidirectionally with home systems. Rather than simply protecting themselves, they can participate in whole-home energy management strategies.
Predictive Maintenance Capabilities
Beyond reacting to problems, predictive maintenance aims to prevent them entirely:
- Continuous monitoring of motor parameters to detect gradual changes
- AI-powered analysis of performance trends
- Sensors that detect signs of impending component failure
- Automatic scheduling of maintenance based on actual usage patterns
- Comparison of performance metrics against expected values
Technical detail: Machine learning algorithms can analyze parameters like current draw patterns, temperature rise rates, and motor speed stability to identify subtle changes that precede failure—often weeks before traditional protection would activate.
Advanced Materials in Protection Components
Material science advances are improving protection component performance:
- High-temperature polymers that better withstand thermal cycling
- Advanced ceramic compounds for more reliable thermal sensing
- Carbon nanotube composites for improved current sensing
- Microelectromechanical systems (MEMS) for more precise protection
- Self-healing materials that can recover from minor overloads
Technical detail: New polymer blends can maintain consistent performance through thousands of thermal cycles, eliminating the “thermal fatigue” that causes conventional bimetallic elements to drift from their specified activation temperatures over time.
Energy Efficiency Improvements Through Better Circuit Design
Protection and efficiency are increasingly intertwined in modern designs:
- More efficient motors produce less waste heat, reducing protection activation
- Dynamic power management adjusts consumption based on cleaning needs
- Improved sensors allow operation closer to optimal points without risk
- Soft-start technologies reduce peak demands while extending component life
- Power factor correction reduces reactive loads and associated heating
Technical detail: Synchronous rectification in motor control circuits can reduce switching losses by up to 30% compared to conventional designs. This directly translates to less heat generation and greater margins between normal operation and protection thresholds.
Wireless Monitoring Capabilities
Wireless monitoring is transforming how users interact with protection systems:
- Smartphone apps that display real-time operational status
- Push notifications when protection systems activate
- Detailed diagnostic information rather than simple warning lights
- Guided troubleshooting when problems occur
- Maintenance reminders based on actual operating conditions
Technical detail: Low-power Bluetooth (BLE) allows vacuums to communicate diagnostic information even when main power is interrupted by protection systems, providing more comprehensive information about fault conditions.
Conclusion
The silent guardians inside your vacuum cleaner represent remarkable engineering achievements that often go unappreciated—until they prevent a costly failure. Circuit protection systems have evolved from simple thermal fuses to sophisticated electronic networks that not only protect but optimize performance.
The modern vacuum cleaner balances on a knife-edge between performance and protection. Manufacturers must design systems that allow motors to deliver powerful suction while simultaneously preventing them from self-destructing under adverse conditions. This balance requires increasingly sophisticated approaches as vacuums become more powerful and feature-rich.
Understanding these protection systems offers practical benefits for vacuum owners:
- Extended appliance lifespan through proper maintenance of protection-related components
- Reduced repair costs by addressing minor issues before they trigger protection systems
- Better cleaning performance since well-maintained airflow systems require less electrical power
- Improved safety through awareness of the warning signs that protection systems provide
As vacuum technology continues to advance, protection systems will likely become even more sophisticated—transitioning from merely reacting to problems toward actively preventing them through predictive intelligence and integration with smart home systems.
For those seeking additional information, manufacturer service manuals often provide detailed specifications for protection components. Professional appliance repair organizations also offer resources for understanding and maintaining these critical systems.
By appreciating the complex symphony of protection mechanisms working inside your vacuum cleaner, you gain not just technical knowledge but practical insights that can save money and extend the useful life of your cleaning equipment.