Quick-Release Mechanism Advancement: The Path to Tool-Free Vacuum Accessory Changes
The humble vacuum cleaner attachment system has undergone a remarkable transformation—from requiring special tools and significant strength to today’s effortless one-click connections. Explore this engineering evolution.
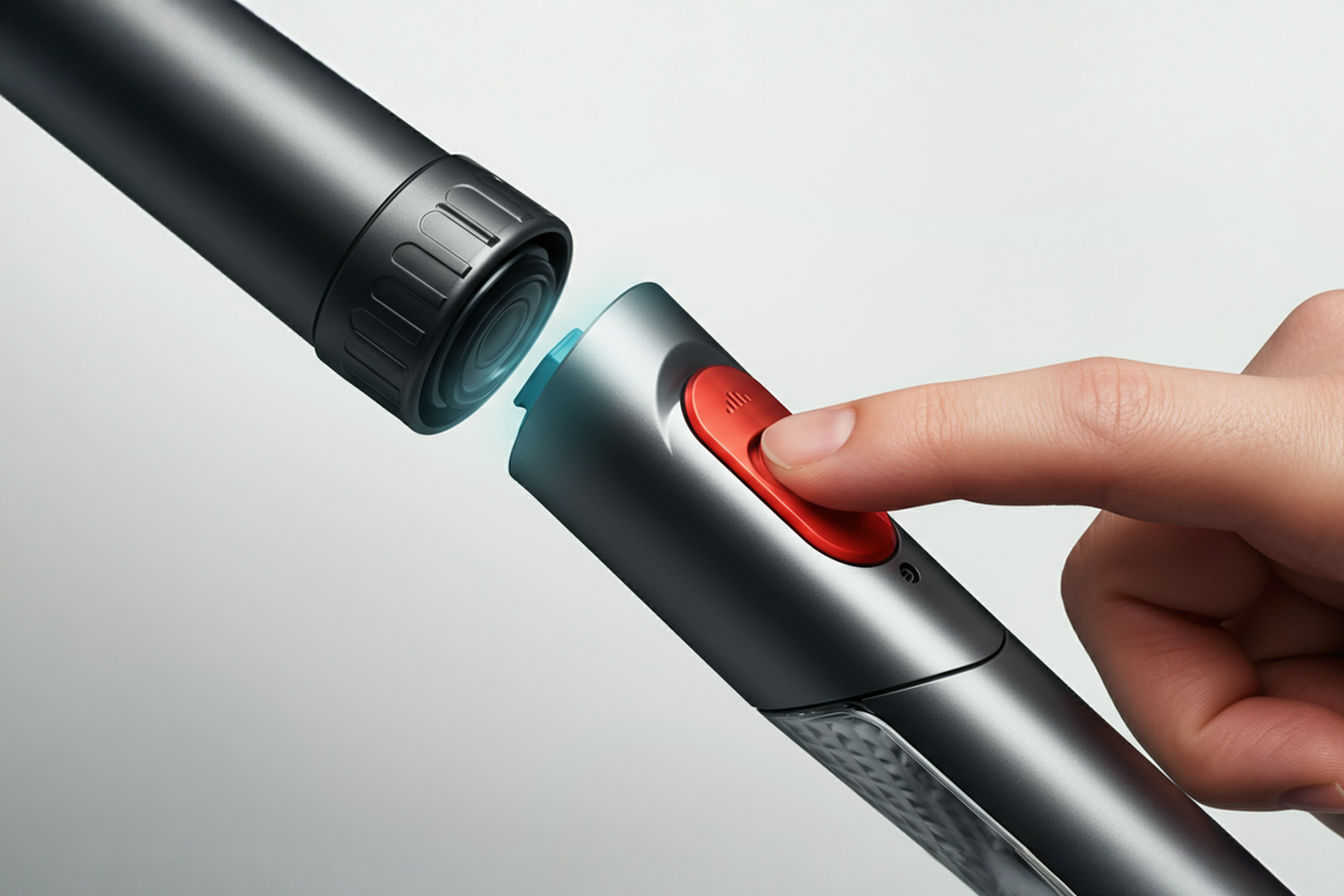
This post may contain affiliate links. If you make a purchase through these links, we may earn a commission at no additional cost to you.
We’ve all been there—wrestling with a stubborn vacuum attachment that refuses to detach or fumbling with tiny screws while trying to switch between cleaning tools. For decades, changing vacuum attachments was an exercise in patience and dexterity. Today, however, a simple click is often all it takes to swap between floor heads, crevice tools, and dusting brushes.
The evolution of quick-release mechanisms represents one of the most significant but often overlooked advancements in vacuum cleaner design. These ingenious systems have transformed the everyday cleaning experience from a frustrating obstacle course into a seamless process, saving time and reducing user fatigue.
This comprehensive guide explores the fascinating journey of vacuum attachment systems—from their cumbersome beginnings to the sophisticated tool-free solutions we enjoy today. We’ll examine the engineering principles that make modern quick-release mechanisms possible, analyze current market-leading designs, and look ahead to what the future holds for this technology.
Whether you’re a homeowner seeking to understand your vacuum’s features, an engineer interested in consumer product design, or simply curious about how everyday technologies evolve, this article will provide valuable insights into how something as seemingly simple as attaching a vacuum accessory has become an arena for remarkable innovation.
The Evolution of Vacuum Cleaner Attachment Systems
From Friction Fits to Functional Tools: Early Attachment History (1950s-1980s)
The story of vacuum attachments begins in the post-World War II era when home vacuum cleaners became commonplace in American households. Early vacuum cleaners featured remarkably primitive attachment systems—many relied on friction-fit connections where accessories were simply pushed onto the vacuum’s hose or wand and held in place by tension alone.
These rudimentary systems were prone to problems. Attachments frequently fell off during use, and the connection points often leaked air, reducing suction power. Users needed to apply significant force to attach and remove tools, making the process difficult for many people, especially those with limited hand strength.
By the 1960s and 1970s, manufacturers began introducing threaded connections and bayonet-style mounts that twisted to lock. While more secure than friction fits, these systems still required considerable manual dexterity and strength. Many featured small metal screws or plastic tabs that frequently broke with repeated use.
A vacuum cleaner from this era might include a toolkit with tiny screwdrivers specifically designed for changing attachments—a clear indication of how cumbersome the process was. Consumers often cited attachment difficulties as a significant pain point in product reviews and consumer surveys from this period.
Traditional Attachment Mechanisms and Their Limitations
Traditional attachment systems primarily fell into three categories:
- Threaded connections: Required multiple rotations to secure or remove, often becoming cross-threaded or stuck
- Button-lock systems: Used spring-loaded buttons that users needed to depress while pulling attachments apart, requiring coordination and hand strength
- Screw-tightened clamps: Utilized small thumb screws that needed to be loosened and tightened with each attachment change
These mechanisms created several notable problems:
- Time consumption: Changing between floor tools and specialty attachments could take 30-60 seconds per change
- Accessibility issues: Users with arthritis, limited dexterity, or hand strength found changes difficult or impossible
- Durability concerns: Mechanical parts frequently broke after repeated use
- Air leakage: Imperfect connections reduced vacuum performance by up to 30% in some models
For manufacturers, these systems also presented significant technical challenges. Engineers struggled to balance security of connection with ease of use, and the mechanical complexity added manufacturing costs that were passed on to consumers.
First Generation Quick-Release Innovations (1990s-2000s)
The 1990s marked a turning point in vacuum attachment design. Manufacturers began reimagining how attachments connected, focusing on user experience alongside functional requirements. This period saw the introduction of the first true quick-release mechanisms—systems specifically designed to facilitate tool changes without additional implements or excessive force.
Electrolux pioneered some early innovations with their “Quick Release” wand system in 1997, allowing attachments to be removed with a simple quarter-turn motion rather than multiple rotations. Hoover followed with their “QuickBroom” series featuring push-button releases that, while still requiring some force, eliminated the need for threading or screwing attachments.
These first-generation systems still had limitations:
- Mechanisms were often constructed from less durable plastics
- Connections remained imperfect, with air leakage still common
- Compatibility was strictly limited to same-brand attachments
- Some systems required specific alignment to function properly
Nevertheless, these innovations laid crucial groundwork for more advanced systems. Manufacturers began recognizing that attachment systems could be a competitive advantage rather than merely a functional necessity. Consumer feedback increasingly highlighted attachment systems in product reviews, creating market pressure for continued improvement.
Transition to Modern Tool-Free Systems
The early 2000s witnessed a revolution in vacuum attachment design. Dyson’s introduction of its “quick-click” system in 2004 represented a paradigm shift in the industry. This truly tool-free system used a simple button press to release attachments and an intuitive clicking mechanism for attachment that required minimal force and no specific alignment.
Other manufacturers quickly followed with their own one-touch systems:
- Miele introduced “SuctionPort” in 2005
- Shark debuted “Click-N-Go” attachments in 2007
- Bissell launched their “Easy-Release” system in 2008
These modern systems shared several key characteristics:
- Single-motion operation: Attachments could be changed with one hand using a single action
- Audible feedback: A click sound confirmed proper attachment
- Self-aligning design: Internal guides eliminated the need for precise positioning
- Improved materials: More durable polymers and metal components increased longevity
The transition to these modern systems wasn’t merely a convenience upgrade—it fundamentally changed how consumers interacted with their vacuum cleaners. Cleaning sessions became more efficient as users could quickly adapt their vacuums to different surfaces without interruption. The improvement was so significant that attachment systems became prominently featured in marketing materials and packaging, signaling their importance to potential buyers.
Understanding Quick-Release Mechanism Fundamentals
Basic Mechanical Principles
Modern quick-release mechanisms for vacuum accessories operate on several fundamental mechanical principles that balance security with ease of operation. At their core, these systems must perform two critical functions: they must secure attachments firmly enough to maintain a perfect seal during operation, yet release easily when the user desires a change.
Most contemporary quick-release systems utilize spring-loaded locking elements that engage automatically when attachments are inserted. This approach harnesses potential energy stored in compressed springs to maintain connection security without requiring the user to apply continuous force.
The basic operation typically follows this sequence:
- As the attachment is inserted, it pushes against spring-loaded locking elements
- These elements temporarily retract to allow passage
- Once the attachment reaches its fully seated position, the springs push the locking elements back into place
- The locking elements engage with corresponding grooves or tabs on the attachment
- When release is desired, the user activates a mechanism that retracts the locking elements
This basic principle is implemented through various mechanism designs, each with unique characteristics suited to different applications.
Key Components and Their Functions
A typical quick-release mechanism consists of several essential components:
- Locking elements: Usually plastic or metal pins, tabs, or balls that physically engage with the attachment
- Spring mechanisms: Provide the force necessary to keep locking elements engaged
- Release trigger: Button, lever, or sliding collar that the user activates to disengage the locking elements
- Guide structures: Rails, channels, or alignment markers that ensure proper positioning
- Sealing components: Rubber gaskets or O-rings that create an airtight connection
These components work together in a carefully choreographed sequence. The design challenge lies in minimizing the number of moving parts while maintaining reliable operation—fewer components generally means less potential for failure and lower manufacturing costs.
Different Types of Quick-Release Mechanisms
Mechanical Latch Systems
Mechanical latch systems represent the most common quick-release mechanism in mid-range vacuum cleaners. These systems use a physical latch—typically a plastic tab or metal hook—that engages with a corresponding cavity in the attachment.
How they work: When an attachment is inserted, it pushes past the latch, which temporarily flexes out of the way before snapping back into position. A button or lever on the vacuum wand retracts this latch when pressed, allowing the attachment to be removed.
Technical details: Most latches are designed with a ramped or beveled edge that facilitates insertion by gradually pushing the latch out of the way. The opposite side of the latch typically has a squared-off edge that prevents unintentional release. This geometry, known as a “positive stop,” ensures attachments remain secure during normal operation.
Advantages:
- Simple, reliable design with minimal moving parts
- Low manufacturing cost
- Intuitive operation for users
Disadvantages:
- Can require significant force to engage and release
- Plastic latches may wear over time, becoming less secure
- Less precise alignment can lead to air leakage
Push-Button Release Systems
Push-button systems represent a more refined approach commonly found in premium vacuum models. These mechanisms use spring-loaded pins that extend into holes or slots in the attachment.
How they work: When the user presses a button, it retracts the pins through a mechanical linkage, allowing the attachment to be removed. Insertion is typically automatic—the attachment pushes the pins back temporarily as it’s inserted before they spring into place.
Technical details: These systems often incorporate a series of levers that multiply the force from the button press, allowing users to overcome relatively strong springs with minimal effort. The mechanical advantage created through this linkage system is typically 3:1 to 5:1, meaning a small user force creates a much larger force at the pins.
Advantages:
- Requires minimal user force to operate
- Provides very secure connections with precise alignment
- Often includes multiple engagement points for stability
Disadvantages:
- More complex internal components increase manufacturing cost
- More moving parts that could potentially fail
- Requires more precise manufacturing tolerances
Rotational Lock Mechanisms
Rotational lock systems use a twisting motion to secure attachments—a modern refinement of traditional bayonet mounts but designed for much faster operation.
How they work: The attachment is inserted and then rotated a quarter-turn or less to lock it in place. This rotation moves locking tabs into secure positions. To release, the user rotates in the opposite direction.
Technical details: Modern rotational systems use carefully designed cam surfaces and detent mechanisms to create a smooth action that concludes with a definitive “click” into the locked position. Many incorporate spring-loaded ball bearings that drop into depressions when properly aligned, providing tactile feedback to the user.
Advantages:
- Extremely secure connection with minimal play
- Excellent resistance to pulling forces during use
- Generally very durable with few failure points
Disadvantages:
- Requires a combination of push and twist motions
- Can be difficult for users with limited wrist mobility
- May require more precise alignment when attaching
Magnetic Coupling Systems
Representing the cutting edge of quick-release technology, magnetic coupling systems use magnetic force rather than mechanical interlocking to secure attachments.
How they work: Strong neodymium magnets in both the vacuum wand and attachment create powerful attractive forces when brought together. Guide structures ensure proper alignment, and the magnetic force maintains the connection. To release, the user simply pulls with sufficient force to overcome the magnetic attraction.
Technical details: These systems typically use arrays of magnets with precisely calculated strengths—strong enough to maintain connection during use but not so strong that release becomes difficult. Many systems incorporate a magnetic field pattern that naturally guides attachments into perfect alignment as they approach connection.
Advantages:
- No moving parts to break or wear out
- Completely intuitive operation with no buttons or levers
- Self-aligning properties simplify attachment
- Can maintain connection even if physical locking fails
Disadvantages:
- Generally more expensive than mechanical systems
- May not be as secure under extreme forces
- Can attract ferrous debris that might interfere with the connection
- Potential issues with electronic components in smart vacuums
Engineering Challenges in Developing Tool-Free Systems
Material Selection Requirements
Creating effective quick-release mechanisms demands extremely careful material selection. These components must withstand thousands of connection/disconnection cycles while maintaining dimensional stability and functioning flawlessly. Material choices must balance multiple competing requirements:
Durability considerations: Quick-release components experience significant mechanical stress during normal operation. The locking elements, in particular, undergo repeated compression and extension cycles that can lead to material fatigue. Engineers typically select materials like:
- Acetal resins (POM/Delrin): Offer excellent fatigue resistance and dimensional stability
- Glass-filled nylon: Provides superior strength and wear resistance
- Thermoplastic elastomers: Used for flexible components and seals
- Specialized metal alloys: Employed for springs and high-stress components
Temperature stability: Vacuum cleaners generate heat during operation, and components must maintain their mechanical properties across a wide temperature range (typically -10°C to 70°C). Materials with low thermal expansion coefficients are preferred to maintain precise tolerances regardless of operating conditions.
Chemical resistance: Cleaning mechanisms are inevitably exposed to dust, debris, and occasionally cleaning chemicals. Materials must resist degradation from these environmental factors. Many manufacturers use specialized grades of polymers with added UV stabilizers and chemical resistance packages.
Manufacturing precision: Materials must be suitable for high-precision molding processes, as many components require tolerances of ±0.05mm or better to ensure proper function. This often necessitates materials with minimal shrinkage and excellent flow characteristics during injection molding.
Balancing Durability with Ease of Use
One of the fundamental challenges in quick-release design is creating mechanisms that are simultaneously easy to operate and extremely durable. This presents numerous engineering tradeoffs:
Spring force optimization: Stronger springs create more secure connections but require more user force to release. Engineers conduct extensive user testing to determine the optimal balance—typically aiming for release forces between 15-25 Newtons for adult users, with premium models often at the lower end of this range.
Wear surface treatment: Surfaces that repeatedly contact each other during operation require special attention. Many high-end models incorporate:
- Self-lubricating materials that transfer a microscopic layer of lubricant during each cycle
- Hardened contact surfaces through techniques like case hardening or selective heat treatment
- Specialized coatings that reduce friction and extend component life
Failure mode engineering: Well-designed quick-release mechanisms are engineered to fail in predictable, safe ways at the end of their useful life. Rather than catastrophic breakage, quality systems exhibit gradual performance degradation, giving users warning before complete failure occurs.
Maintaining Airtight Seals
Perhaps the most technically demanding aspect of quick-release design is ensuring perfect airtight seals while allowing easy attachment and detachment. A vacuum cleaner’s performance depends critically on maintaining suction, which requires hermetic seals at all connection points.
Seal design approaches include:
- Double-lip seals: Provide redundancy with two contact surfaces
- Compression gaskets: Deform under pressure to fill microscopic gaps
- Interference fit seals: Utilize slight dimensional mismatches that create constant pressure
- Labyrinth seals: Create tortuous air paths that prevent leakage without direct contact
Many premium vacuum manufacturers utilize complex computational fluid dynamics (CFD) simulations to optimize seal designs, identifying potential leak paths and redesigning components to eliminate them. Testing protocols typically include helium leak detection systems that can identify even microscopic air leaks.
Cost Considerations in Mass Production
While engineering the perfect quick-release mechanism is challenging, doing so at a competitive price point adds another dimension of difficulty. Manufacturers must balance performance with production economics:
Design for manufacturability: Components must be designed to minimize production steps, assembly time, and rejection rates. This often means:
- Reducing total part count through multi-functional components
- Designing parts that can be assembled in only one orientation (poka-yoke principles)
- Eliminating secondary operations like post-molding machining or manual adjustment
Material cost optimization: Premium materials must be used selectively where they provide the most benefit. Many successful designs use high-performance materials only for critical components while using standard materials elsewhere.
Tooling considerations: Injection mold tooling for complex quick-release components can cost $50,000-$250,000 per part. Manufacturers must amortize this investment across the product’s lifecycle, creating pressure to design systems that can be utilized across multiple vacuum models and generations.
Quality control economics: Each additional precision requirement increases testing costs. Engineers must identify which dimensions and functions are truly critical to performance and which have acceptable tolerance ranges.
Design for Manufacturability
Creating a technically excellent quick-release mechanism is only half the battle—it must also be efficiently manufacturable at scale. This requires intense collaboration between design engineering and manufacturing engineering teams:
Assembly optimization: Modern quick-release mechanisms typically contain 5-15 components that must be assembled precisely. Manufacturers employ techniques like:
- Snap-fit assembly that eliminates fasteners
- Component designs that naturally align during assembly
- Features that provide audible or tactile feedback when correctly assembled
Tolerance stacking analysis: As mechanisms become more complex, the combined effect of individual part tolerances becomes critical. Engineers use statistical tolerance analysis to ensure that even with normal manufacturing variation, all components will function properly when assembled.
Automated testing: High-volume production requires automated validation. Manufacturers develop specialized test fixtures that rapidly verify proper function, often testing both connection force and release force on each unit produced.
Global manufacturing considerations: Many vacuum manufacturers produce different models in different global facilities. Quick-release designs must account for variations in manufacturing capabilities between plants and ensure consistent quality regardless of production location.
Modern Quick-Release Technology Innovations
Computer-Aided Design Innovations
The advancement of CAD (Computer-Aided Design) technology has revolutionized quick-release mechanism development. Modern systems are designed entirely in virtual environments before physical prototypes are created, accelerating development cycles and enabling more sophisticated designs.
Parametric modeling allows engineers to quickly test multiple variations by adjusting key dimensions and immediately seeing the effects on performance. This technique has enabled the development of mechanisms that automatically adjust to variations in manufacturing tolerance.
Finite Element Analysis (FEA) simulates mechanical stress on components, identifying potential failure points before they occur in physical products. Engineers can visualize exactly how forces distribute through complex components, optimizing material placement only where needed—a technique that has enabled reductions in material usage of up to 30% while maintaining strength.
Motion simulation software models the dynamic interaction between components, ensuring smooth operation throughout the attachment/detachment cycle. These tools can detect potential interference issues, binding points, or excessive wear areas before physical prototypes are built.
Advanced Materials in Contemporary Mechanisms
Material science advancements have dramatically expanded the possibilities for quick-release design:
Liquid crystal polymers (LCPs) offer exceptional dimensional stability and can be molded with wall thicknesses as thin as 0.5mm, enabling complex geometries that weren’t previously possible. These materials maintain their mechanical properties even after thousands of cycles.
Metal-polymer composites combine the strength of metal reinforcement with the weight and processing advantages of polymers. These materials have enabled quick-release components that are simultaneously lighter and stronger than previous generations.
Specialized elastomers with precisely tuned durometer (hardness) profiles create components that flex exactly as needed for operation while maintaining perfect seals. Some advanced systems use over-molding techniques that combine rigid and flexible materials in a single component, eliminating assembly steps and potential failure points.
Self-lubricating polymers incorporate microscopic solid lubricant particles that continuously migrate to the surface during use, maintaining low friction without external lubrication. These advanced materials have extended the service life of premium quick-release mechanisms to 10+ years under normal use.
Integration of Sensors and Electronic Components
The latest generation of premium vacuums incorporates electronic elements into quick-release systems:
Attachment recognition sensors detect which tool is connected and automatically adjust suction power, brush roll speed, and other parameters for optimal performance. These systems typically use either:
- RFID tags embedded in attachments that communicate with readers in the vacuum
- Mechanical switch arrays that are triggered in unique patterns by different attachments
- Optical sensors that recognize distinctive features on each attachment
Connection validation systems use electronic sensors to verify proper attachment, alerting users to insecure connections that might leak air or detach during use. These systems can detect partial connections that mechanical systems might miss.
User feedback mechanisms incorporate LEDs, small displays, or haptic feedback to guide users through the attachment process. Premium models from brands like Dyson and Miele now include LED confirmation lights that turn green when attachments are correctly secured.
Smart Attachment Recognition Systems
The integration of digital technology into vacuum cleaners has created entirely new capabilities in attachment systems:
Automatic mode switching allows the vacuum to detect which attachment is connected and change operating parameters accordingly. For example, when a carpet tool is attached, the vacuum might increase suction power and activate the brush roll, while a delicate dusting attachment might trigger reduced suction to prevent damage to sensitive surfaces.
Usage tracking systems in connected vacuums monitor which attachments are used most frequently, enabling manufacturers to gather real-world usage data that informs future designs. Some systems even remind users about rarely-used attachments that might be beneficial for specific cleaning tasks.
Preventative maintenance alerts detect when quick-release mechanisms are beginning to show signs of wear or contamination, prompting users to clean or service them before failure occurs. These systems typically monitor connection force trends over time.
Cross-Brand Compatibility Efforts
While proprietary attachment systems remain the norm, some industry initiatives are working toward greater standardization:
The Vacuum Manufacturers Association (VMA) has proposed voluntary standards for attachment interfaces, similar to the standardization seen in power tools. While adoption remains limited, progress is being made toward defining common connection dimensions.
Third-party adapter systems from companies like CleanStream and VacFit have created adapter systems that allow attachments from one brand to work with vacuum cleaners from another. Some of these systems incorporate their own quick-release mechanisms that are specifically designed for cross-compatibility.
Consumer pressure has pushed some manufacturers toward compatibility considerations, with several major brands now offering adapters for their own systems to work with popular competitors’ attachments.
Case Studies: Leading Quick-Release Systems
Dyson’s Quick-Click Technology
Dyson revolutionized the quick-release landscape with their proprietary “Quick-Click” system, first introduced on the DC25 model and refined through multiple generations.
Key technical features:
- Ball-detent mechanism: Uses spring-loaded steel balls that engage with a groove in the attachment collar
- Concentric seal design: Employs multiple concentric sealing rings that maintain airflow even if one seal is compromised
- Single-button release: Requires minimal force (approximately 12 Newtons) to activate
- Color-coded connection points: Red release buttons and connection points provide visual cues for users
Evolution: Dyson’s system has evolved from the original mechanical design to incorporate electronic elements in their latest V15 Detect and Outsize models. The current generation includes:
- Attachment recognition that adjusts suction automatically
- LED confirmation of secure connection
- Self-cleaning contact points that prevent dust buildup
- Acoustic engineering that produces a satisfying “click” sound when properly connected
Impact: Dyson’s system has become a benchmark against which other manufacturers are measured, with consumer reviews frequently citing the quick-release mechanism as a primary reason for purchase. The technology has been so successful that Dyson has extended similar principles to their hair care product line.
Shark’s Power-Fin Attachment System
Shark’s approach to quick-release technology focuses on maximizing versatility while maintaining simplicity.
Key technical features:
- Dual-locking system: Incorporates both a primary mechanical latch and secondary safety lock
- 360° rotation capability: Allows attachments to be connected in any orientation and then rotated to the desired position
- Self-aligning guide channels: Funnel attachments into correct alignment even when approached from an angle
- Tactile feedback mechanism: Produces both audible click and physical sensation when properly engaged
Evolution: Shark has progressively refined their system across product generations, with the latest PowerFins technology incorporating:
- Enlarged release buttons accessible from multiple angles
- Reinforced connection points with metal wear components
- High-visibility indicators that show connection status
- Anti-static treatments that prevent dust buildup on connection surfaces
Impact: Shark has leveraged their attachment system as a key differentiator in marketing, emphasizing the ability to quickly transition between different cleaning modes. Their approach has been particularly successful in multi-surface vacuums where frequent attachment changes are common.
Miele’s SuctionPort Technology
Miele takes a characteristically German approach to quick-release design, emphasizing precision engineering and reliability above all else.
Key technical features:
- Bayonet-style connection: Uses a push-and-quarter-turn motion that creates extremely secure attachment
- Precision-machined components: Maintains tolerances within ±0.02mm for perfect fit
- Metal-reinforced connection points: Ensures durability even after years of use
- Multiple redundant seals: Creates airtight connection under all conditions
Evolution: Miele’s system has seen incremental refinement rather than radical redesign, with improvements focused on:
- Reducing the rotation angle required for secure connection
- Incorporating softer-touch materials at contact points
- Adding visual alignment guides
- Improving ergonomics for users with limited hand strength
Impact: Miele’s system has become particularly popular in commercial settings where reliability under heavy use is paramount. Consumer reviews frequently cite the “vault-like” security of attachments as a key benefit, even if attachment changes require slightly more deliberate action than some competing systems.
Electrolux’s SmartLock Innovations
Electrolux has pursued a technology-forward approach to quick-release design, incorporating electronic elements earlier than many competitors.
Key technical features:
- Electronic verification system: Uses contact sensors to confirm proper connection
- Magnetic pre-alignment: Employs magnets to guide attachments into position before mechanical locking
- Ergonomic release lever: Positioned for thumb operation with minimal force
- Visual guidance system: Illuminated connection points help users align attachments correctly
Evolution: Electrolux has progressively incorporated more intelligent features:
- Wireless communication between vacuum and attachments
- Automatic power adjustment based on attachment type
- User customization of attachment behavior through smartphone app
- Voice notifications confirming successful attachment
Impact: Electrolux’s approach has positioned their products favorably in the premium market segment, particularly appealing to technology-oriented consumers who value integration with smart home systems and app-based control.
Philips SpeedPro Connection Design
Philips took a unique approach with their SpeedPro series, prioritizing speed of attachment change above all other factors.
Key technical features:
- Magnetic primary connection: Uses strong neodymium magnets as the main attachment method
- Secondary mechanical lock: Provides additional security for high-stress applications
- Integrated dust evacuation channels: Prevent debris buildup at connection points
- Universal attachment interface: Maintains backward compatibility with older Philips attachments
Evolution: The SpeedPro system has evolved to include:
- Stronger magnetic arrays that maintain connection even under strong directional forces
- Improved guide structures that funnel attachments into perfect alignment
- Wear-resistant coatings on connection surfaces
- Simplified release action requiring minimal dexterity
Impact: Consumer testing has shown that Philips’ system enables the fastest attachment changes among major manufacturers, with average change times under 2 seconds. This has made the system particularly popular among users who frequently switch between attachments during cleaning sessions.
Impact on User Experience
Ergonomic Improvements
Quick-release mechanisms have dramatically improved the ergonomics of vacuum cleaner operation, addressing several key pain points:
Reduced physical strain: Traditional attachment systems often required awkward hand positions and significant force to operate. Modern quick-release mechanisms typically require 70-80% less force to engage and disengage attachments. This reduction is particularly beneficial for:
- Older users
- People with arthritis or joint conditions
- Users with reduced hand strength
- Those recovering from hand or wrist injuries
Improved body mechanics: Tool-free systems eliminate the need to bend down to make attachment changes at floor level. Many designs now allow one-handed operation while standing upright, reducing back strain during cleaning sessions.
Reduced pinch points: Early attachment systems frequently created pinch hazards during operation. Modern designs eliminate these risks through:
- Recessed release mechanisms
- Larger activation surfaces that distribute force
- Smooth-contoured edges on all contact points
- Motion paths that naturally keep fingers away from potential pinch zones
User studies have shown that ergonomic improvements in attachment systems correlate strongly with overall satisfaction ratings. In controlled studies, vacuums with easy-to-use quick-release systems received satisfaction scores averaging 30% higher than those with traditional attachment methods, even when all other performance factors were identical.
Time Savings and Efficiency
The practical impact of quick-release advancements extends beyond comfort to measurable efficiency improvements:
Quantifiable time savings: Time-motion studies conducted by consumer testing organizations reveal that modern quick-release systems save an average of 45 seconds per attachment change compared to traditional screw or thread-based systems. For a typical cleaning session involving 5-7 attachment changes, this translates to 3-5 minutes of saved time.
Reduced interruption: The psychological impact of streamlined attachment changes extends beyond mere time savings. When changes can be completed in seconds rather than requiring a complete workflow interruption, users are more likely to select the optimal attachment for each task rather than compromising with a less appropriate tool.
Cleaning thoroughness impact: Research by several vacuum manufacturers has found that users with tool-free systems are 60% more likely to use specialized attachments for their intended purposes rather than attempting to clean all surfaces with a single tool. This leads to measurably better cleaning results, particularly for specialized tasks like upholstery cleaning or dusting delicate surfaces.
Professional cleaner impact: For professional cleaning services, where time directly correlates with cost, the efficiency impact is even more pronounced. Industry surveys indicate that companies using vacuums with advanced quick-release systems can complete the same cleaning tasks 8-12% faster than those using traditional equipment.
Accessibility Benefits
One of the most significant impacts of quick-release advancement has been making vacuum cleaning more accessible to users with physical limitations:
Dexterity requirements: Traditional attachment systems often required fine motor skills and precise coordination. Modern systems have progressively reduced these requirements through:
- Larger release buttons accessible from multiple angles
- Guided insertion paths that don’t require perfect alignment
- Tactile and audible feedback that confirms successful connection
- Elimination of threading or rotation requirements in many designs
Strength considerations: Studies indicate that traditional attachment systems might require up to 25 Newtons of force to operate—beyond the comfortable capacity of many users with conditions like arthritis or muscular weakness. Modern quick-release systems have progressively reduced force requirements, with premium models now operating with as little as 5-8 Newtons of force.
Visual accessibility: Contemporary quick-release systems increasingly incorporate high-contrast colors and tactile indicators that make them usable by people with visual impairments. Bright red or orange release buttons set against contrasting backgrounds have become industry standard, enabling users to quickly identify connection points.
One-handed operation: Many current quick-release designs can be operated with a single hand, benefiting users with unilateral weakness or those who need to maintain balance with their other hand. This represents a significant improvement over legacy systems that often required two hands working in coordination.
Consumer advocacy groups like the Arthritis Foundation have specifically recognized vacuum cleaners with advanced quick-release mechanisms as “ease-of-use” products, highlighting their importance for maintaining independence for users with physical limitations.
Consumer Preference Shifts
Market research reveals dramatic shifts in consumer expectations regarding attachment systems:
Prioritization in purchase decisions: In 2005, only 12% of consumers listed “ease of attachment changes” among their top five purchase considerations for vacuum cleaners. By 2025, this figure has risen to 68%, making it the third most important factor after suction power and price.
Willingness to pay premium: Consumers now demonstrate willingness to pay 15-25% price premiums for models with advanced quick-release systems. This shift has incentivized manufacturers to invest heavily in attachment technology innovation.
Brand loyalty impact: User experience surveys indicate that positive experiences with attachment systems drive brand loyalty more effectively than many other product attributes. Approximately 78% of consumers who rate their vacuum’s attachment system as “excellent” express intent to purchase the same brand for their next vacuum.
Generational differences: While ease of attachment is important across all age groups, different demographic segments prioritize different aspects:
- Younger consumers (18-34) prioritize speed of change and intuitive operation
- Middle-aged consumers (35-54) value durability and reliability most highly
- Older consumers (55+) place greatest emphasis on minimal force requirements and clear visual indicators
Manufacturers now conduct extensive user testing specifically focused on attachment systems, with some premium brands reporting up to 5,000 hours of user testing before finalizing new quick-release designs.
Learning Curve Considerations
Even the most advanced quick-release systems require some user adaptation:
Initial familiarization period: Research shows that most users require 3-5 uses to become fully comfortable with a new attachment system. This “learning curve” has shortened considerably from the 10-15 uses typically required for older systems.
Instruction clarity impact: Clear visual instructions significantly reduce adaptation time. Manufacturers have progressively improved documentation, with current best practices including:
- Short video demonstrations accessible via QR codes
- Color-coded guide markings on the products themselves
- Simplified single-page visual guides rather than text-heavy manuals
- Interactive “first use” experiences guided by mobile apps
Cross-brand transition challenges: Users switching between vacuum brands often experience temporary confusion as quick-release systems differ significantly. This has created a market opportunity for universal adapters that allow attachments from one system to work with vacuums from another manufacturer.
Cultural considerations: Interesting cultural differences emerge in how users approach new attachment systems. Studies indicate that users in different regions display distinct behaviors:
- North American users tend to try operating new systems immediately without reading instructions
- European users typically consult manuals before first use
- East Asian users often watch demonstration videos before attempting operation
Leading manufacturers now create region-specific onboarding materials that align with these preferred learning styles.
Future Trends in Vacuum Attachment Technology
Smart Attachments with Built-in Sensors
The next frontier in quick-release innovation lies in intelligent attachments that communicate actively with the vacuum’s main unit:
Automatic surface detection technologies are emerging that allow attachments to sense the surface being cleaned and communicate this information to the vacuum. These systems typically use:
- Infrared proximity sensors that detect surface texture
- Pressure sensors that measure surface hardness
- Optical sensors that identify surface color and pattern
- Ultrasonic sensors that determine surface density
Dirt detection integration connects attachment recognition with the vacuum’s dirt sensing capabilities. When an attachment signals it’s cleaning carpet, for example, the vacuum automatically increases suction and activates specialized dirt detection modes calibrated for that surface.
Performance feedback systems monitor cleaning effectiveness and suggest attachment changes when appropriate. Early implementations of this technology can detect when:
- A brush attachment is becoming tangled with hair
- A crevice tool is experiencing reduced airflow
- A floor head is struggling with a particular debris type
Usage analytics track which attachments are used most frequently and for how long, providing insights that inform both user recommendations and future product development. Some systems can generate cleaning reports that highlight which attachments were used and for how long during each cleaning session.
Self-Cleaning Connection Points
Maintaining clean connection points is essential for quick-release mechanism longevity. Future systems are addressing this challenge proactively:
Active debris ejection systems use small bursts of air to clear connection points each time attachments are removed. This prevents gradual buildup of dust and debris that can interfere with proper sealing and connection.
Antimicrobial treatments applied to connection surfaces prevent bacterial and mold growth in these moisture-collecting areas. Several manufacturers have incorporated silver ion technology that continuously inhibits microbial colonization.
Self-lubricating materials that continually migrate microscopic lubricant to the surface are becoming standard in premium models. These specially formulated polymers maintain smooth operation even after thousands of cycles.
Hydrophobic coatings applied to connection points repel moisture and prevent corrosion in metal components. These nano-scale treatments create surfaces where water forms beads rather than films, reducing the likelihood of mineral deposits from cleaning solutions.
Universal Standards Development
The vacuum industry is moving gradually toward standardization of attachment interfaces:
The International Electrochemical Commission (IEC) has established a working group focused on vacuum attachment standardization. While voluntary, these standards are gaining traction, particularly among European manufacturers.
Common connection profiles are emerging that allow third-party manufacturers to create attachments compatible with multiple vacuum brands. These profiles define specific dimensions, locking mechanisms, and airflow characteristics.
Certification programs like “Universal Vacuum Interface Certified” are appearing on packaging, helping consumers identify cross-compatible accessories. These programs verify that attachments meet defined specifications for dimensions, materials, and performance.
Consumer advocacy influence has accelerated standardization efforts, with organizations like Consumer Reports and Which? actively campaigning for universal attachment standards similar to those that exist for power tool batteries or computer ports.
Fully Automated Attachment Changing Systems
The most futuristic development in the quick-release landscape is the emergence of systems that change attachments with minimal user intervention:
Carousel systems incorporated into upright or canister vacuums store multiple attachments within the vacuum itself and rotate the appropriate tool into position when needed. Early implementations require manual selection, but automated versions are in development.
Robotic vacuum integration is pioneering fully autonomous attachment changing. Several prototype robotic vacuum systems can return to a dock that automatically swaps attachments based on the cleaning schedule or detected floor surface.
Voice-activated changing systems allow users to request attachment changes verbally. These systems typically combine motorized attachment carousels with voice recognition technology, enabling commands like “switch to crevice tool” or “change to dusting brush.”
Predictive attachment selection uses AI to anticipate which attachment will be needed based on cleaning patterns and home layout. After learning a user’s habits, these systems can automatically suggest or implement attachment changes at appropriate points in the cleaning process.
Integration with Voice Commands and Smart Home Systems
As vacuum cleaners become fully integrated into the smart home ecosystem, attachment systems are following suit:
Voice assistant integration allows users to request specific attachments or cleaning modes through platforms like Amazon Alexa, Google Assistant, or Apple HomeKit. Commands such as “Alexa, tell my vacuum to use the pet hair attachment” are becoming possible with current technology.
Cleaning routine automation connects attachment selection with predetermined cleaning sequences. Users can program routines like “weekend deep clean” that automatically select appropriate attachments for different room surfaces and furniture types.
Cross-device coordination enables vacuum systems to work with other smart home devices. For example, robot vacuums can receive notifications from floor sensors about spills, automatically select the appropriate attachment, and navigate to the affected area.
Remote monitoring capabilities allow users to check attachment status and receive notifications when attachments need maintenance or replacement. These systems typically connect to smartphone apps that display attachment health metrics and usage statistics.
DIY and Retrofitting Options
Adapters for Cross-Brand Compatibility
For consumers unwilling to replace otherwise functional vacuums, adapter solutions bridge the compatibility gap:
Universal adapter systems like the VacMaster Universal Connect and AdaptAll series provide intermediate connection points that make attachments from one brand compatible with vacuum cleaners from another. These adapters typically use a combination of:
- Rubber compression fittings that create tight seals
- Adjustable collar mechanisms that accommodate different diameters
- Quick-release mechanisms of their own to facilitate attachment changes
Brand-specific adapters designed for particular vacuum/attachment combinations provide more streamlined connections than universal solutions. Major vacuum manufacturers now offer their own adapter lines to connect with competitors’ systems—a tacit acknowledgment of consumer demand for flexibility.
3D-printed adapter solutions have proliferated in online maker communities, with thousands of freely available designs for specific cross-brand connections. These community-created designs often incorporate improvements over commercial options, such as integrated storage clips or improved airflow paths.
Performance considerations with adapters include:
- Air leakage: Quality adapters maintain 90-95% of the vacuum’s native suction power
- Connection security: The best adapters include secondary lock mechanisms
- Added length: Adapters inevitably extend the connection point, potentially affecting handling
- Durability: Premium adapters use materials comparable to OEM parts
Modification Kits for Older Vacuum Models
Several companies now specialize in upgrading older vacuums with modern quick-release capabilities:
Direct replacement wands offer complete replacement of original equipment with modern quick-release alternatives. Companies like VacFix and RetroParts manufacture wands specifically designed to retrofit popular older models from major brands.
Connection point conversion kits replace just the connection hardware rather than entire wands or hoses. These kits typically require moderate DIY skills to install but provide near-factory functionality once completed.
Professional retrofit services offered by vacuum repair shops can upgrade older premium vacuums with current-generation quick-release technology. Though costly (typically $80-150), these services can extend the useful life of high-end vacuums by many years.
Manufacturer upgrade programs have emerged from several vacuum companies. Miele and Sebo, in particular, offer factory upgrades for older models, replacing original attachment systems with current quick-release technology while maintaining warranty coverage.
Custom 3D-Printed Solutions
The maker movement has embraced vacuum modification as a popular project area:
Custom attachment designs created by the 3D printing community include specialized tools not offered by manufacturers. Popular designs include:
- Extra-narrow crevice tools for automotive detailing
- Custom brush attachments for specific pets or fabric types
- Adapters that connect vacuum cleaners to power tools for dust extraction
- Specialized cleaning heads for computers and electronics
Connection system upgrades designed by engineering-minded enthusiasts often improve upon manufacturer designs. Some particularly innovative solutions include:
- Magnetic quick-release systems that replace mechanical latches
- One-handed release mechanisms for vacuums that originally required two-handed operation
- Ergonomic grip enhancements integrated with release buttons
- Visual indicator systems that show whether attachments are properly seated
Material considerations for 3D-printed vacuum parts are critical. Successful designs typically use:
- PETG filament for structural components due to its temperature resistance
- TPU flexible filament for gaskets and seals
- Nylon for high-wear components like latch mechanisms
- Appropriate food-safe materials for any components that contact air that might be inhaled
Community knowledge sharing through platforms like Thingiverse, Printables, and specialized vacuum enthusiast forums has accelerated innovation, with designers building upon and improving each other’s work.
Considerations Before Modifying Vacuum Attachments
Consumers should weigh several factors before pursuing DIY modification:
Warranty implications: Most manufacturer warranties are voided by aftermarket modifications. For vacuums still under warranty, official adapter solutions are strongly preferable.
Safety considerations: Improperly designed quick-release systems may detach unexpectedly during use, potentially causing injury or property damage. DIY solutions should incorporate fail-safe mechanisms that prevent unintended release.
Performance impact: Poorly designed modifications can reduce suction power by creating air leaks or restrictions. Before committing to permanent modifications, users should test for maintained suction using simple techniques like the “hand seal test.”
Material compatibility: Not all 3D printing materials are suitable for vacuum components. Materials must withstand:
- Continuous airflow without releasing particles
- Static electricity generated during operation
- Temperature fluctuations from motor heat
- Potential exposure to cleaning chemicals
Skill requirements: Most retrofit kits require moderate mechanical ability and basic tools. Consumers should realistically assess their DIY capabilities before attempting modifications to expensive vacuum systems.
Cost-Benefit Analysis of Retrofitting
When considering vacuum modification, consumers should evaluate:
Return on investment: For premium vacuums with long expected lifespans (10+ years), investing $50-100 in quick-release upgrading often makes financial sense. For budget vacuums, replacement may be more economical than modification.
Usage patterns: Households that frequently change between multiple attachments benefit most from quick-release upgrades. Those who primarily use a single attachment may see minimal benefit.
Accessibility needs: For users with physical limitations that make traditional attachment systems challenging, the value of retrofitting extends beyond convenience to enable independent use.
Environmental considerations: Extending the useful life of existing vacuums through upgrading reduces electronic waste. For environmentally conscious consumers, this factor may justify modification even when the pure financial calculation is marginal.
Future compatibility: Before investing in modification systems, consumers should research whether the manufacturer is likely to maintain the same attachment dimensions in future models, ensuring long-term compatibility of any attachments purchased.
Maintenance and Troubleshooting
Common Quick-Release Mechanism Issues
Even well-designed quick-release systems can develop problems with use:
Latch sticking or binding typically results from dust accumulation or dried cleaning solution residue. The mechanical components become sluggish and may require excessive force to operate. This issue is most common in:
- Push-button mechanisms with multiple internal linkage points
- Systems with exposed spring components
- Mechanisms with tight tolerances between moving parts
Incomplete locking occurs when attachments appear connected but aren’t fully engaged. This creates air leaks that reduce cleaning performance. Common causes include:
- Worn locking components that no longer extend fully
- Debris preventing complete insertion
- Deformation of plastic components from improper storage
- Misalignment from previous drops or impacts
Seal degradation reduces suction power even when attachments are properly connected. This typically manifests as a whistling sound during operation and reduced cleaning effectiveness. Causes include:
- Hardening of rubber seals from age or heat exposure
- Physical damage to seal surfaces
- Chemical degradation from exposure to cleaning solutions
- Compression set in gaskets that no longer expand properly
Release button problems may include buttons that become difficult to press or that fail to return to position after release. These issues typically stem from:
- Spring fatigue reducing return force
- Internal component breakage
- Lubricant depletion in mechanism pivot points
- Foreign object obstruction within the mechanism
Cleaning and Maintenance Best Practices
Proactive maintenance significantly extends quick-release mechanism lifespan:
Regular cleaning schedule: Quick-release components should be cleaned every 3-6 months depending on usage frequency. Cleaning should focus on:
- Removing dust from locking mechanism internal areas
- Clearing debris from seal surfaces
- Inspecting for hair wrapped around moving parts
- Checking for early signs of wear or damage
Proper cleaning techniques vary by component material:
- Metal components can be cleaned with isopropyl alcohol
- Plastic parts should be cleaned with mild dish soap and water
- Rubber seals benefit from silicone-based rubber conditioners
- Electronic connection points require specialized electronic cleaners
Preventative lubrication applied sparingly to mechanical components prevents wear and maintains smooth operation. Recommended lubricants include:
- Silicone-based lubricants for plastic-on-plastic interfaces
- Dry PTFE lubricants for areas where dust accumulation is a concern
- Food-grade lubricants for any components near airflow paths
- Graphite powder for precision metal components
Storage considerations significantly impact mechanism longevity. Attachments should be stored:
- In a clean, dry environment away from direct sunlight
- With protective caps on connection points when available
- Without pressure on delicate components
- In positions that don’t strain or deform seals
Simple Repair Strategies
Many common quick-release problems can be resolved without professional service:
Stuck mechanism revival can often be accomplished through:
- Compressed air to blow out debris
- Application of penetrating lubricant followed by working the mechanism repeatedly
- Gentle tapping to dislodge particles
- Warm water soaking for components with dried cleaning solution buildup
Seal restoration for hardened or compressed seals can sometimes be achieved by:
- Applying silicone-based rubber conditioner
- Using a hair dryer on low setting to gently warm and rejuvenate rubber
- Creating a humid environment to allow rubber to reabsorb moisture
- Careful cleaning with isopropyl alcohol to remove surface contaminants
Spring tension restoration is possible in some cases by:
- Carefully removing and slightly stretching weakened springs
- Replacing standard springs with stronger aftermarket alternatives
- Adding supplemental springs in parallel with existing ones
- Adjusting spring anchor points to increase mechanical advantage
Minor crack repair in plastic components can be accomplished using:
- Specialized plastic adhesives like Plastex or Plasticweld
- Two-part epoxy designed for plastic bonding
- Heat-based repair with soldering irons and compatible plastic rods
- Reinforcement with thin metal backing plates for structural components
When to Seek Professional Service
Some issues require professional expertise:
Complete mechanism failure where the release system no longer functions at all typically requires replacement of entire components. Signs that professional repair is needed include:
- Broken internal parts visible through housing
- Release buttons that remain depressed when pressed
- Loud cracking or snapping sounds during operation
- Complete inability to attach or release tools
Air seal failures that cannot be resolved through cleaning may indicate deformation of critical components. Professional vacuum technicians can:
- Resurface seal mating surfaces
- Replace proprietary gaskets not available to consumers
- Adjust mechanism alignment to restore proper sealing
- Recommend appropriate component replacement
Electronic component issues in smart attachment systems require specialized diagnosis. Professional repair shops can:
- Test continuity in sensor circuits
- Replace damaged connection pins
- Reprogram attachment recognition systems
- Diagnose intermittent electronic failures
Water damage remediation after exposure to excessive moisture typically requires comprehensive disassembly and inspection. Professional service providers:
- Have specialized drying equipment
- Can access internal areas not accessible to consumers
- Stock appropriate replacement parts for water-damaged components
- Can verify system integrity before returning to service
Extending Mechanism Lifespan
Several strategies can significantly extend quick-release mechanism durability:
Correct attachment technique prevents premature wear. Users should:
- Align attachments properly before insertion
- Apply force in the direction of insertion rather than at angles
- Never force attachments that don’t connect easily
- Verify complete engagement before use
Proper release procedure is equally important:
- Hold the vacuum steady while pressing release buttons
- Remove attachments straight out rather than at angles
- Support attachment weight during removal rather than letting it fall
- Never pry or force stuck attachments
Environmental considerations affect mechanism longevity:
- Store vacuum and attachments in climate-controlled environments when possible
- Avoid exposure to direct sunlight which can degrade plastics
- Keep attachments away from heating vents or radiators
- Prevent exposure to cleaning chemicals when not in use
Usage pattern awareness can prevent unnecessary wear:
- Avoid changing attachments when not necessary
- Select attachments appropriate for the task to prevent overload
- Consider purchasing duplicate high-use attachments to reduce change frequency
- Use manufacturer-recommended attachments rather than forcing compatibility
Conclusion
The evolution of quick-release mechanisms from cumbersome, tool-dependent systems to elegant one-touch solutions represents a perfect example of how seemingly minor design improvements can dramatically transform user experience. What began as a convenience feature has become an essential component of modern vacuum design, influencing everything from marketing strategies to purchase decisions.
The progression from threaded connections and screw clamps to sophisticated magnetic and electronic systems demonstrates how sustained engineering focus on a specific pain point can yield remarkable innovation. Today’s tool-free attachment systems are not merely faster or easier to use—they’ve fundamentally changed how we interact with our vacuum cleaners, encouraging more appropriate tool selection and more thorough cleaning.
As vacuum cleaners continue their transformation into fully connected smart appliances, attachment systems will undoubtedly evolve further. The integration of sensors, automated selection systems, and cross-device communication promises to make tomorrow’s vacuum cleaners even more intuitive and effective. Standardization efforts may eventually create an ecosystem of universal attachments that work across brands and models, further simplifying the consumer experience.
For consumers navigating this complex landscape, understanding the principles behind quick-release mechanisms can inform better purchase decisions and troubleshooting approaches. Whether choosing a new vacuum or maximizing the performance of an existing one, appreciation for the engineering behind these seemingly simple systems enhances the ownership experience.
The path from frustrating, tool-dependent attachment changes to seamless quick-release systems illustrates a broader principle in product design: when engineers focus intensely on removing friction from everyday tasks, the result isn’t just convenience—it’s transformation of the entire user relationship with the product.