Poolside Vacuum Solutions: The Complete Guide to Dry and Wet Pickup for Splash Zones
Managing water and debris around swimming pools requires specialized equipment. This guide explores poolside vacuum solutions that handle both wet and dry pickup to create safer splash zones.
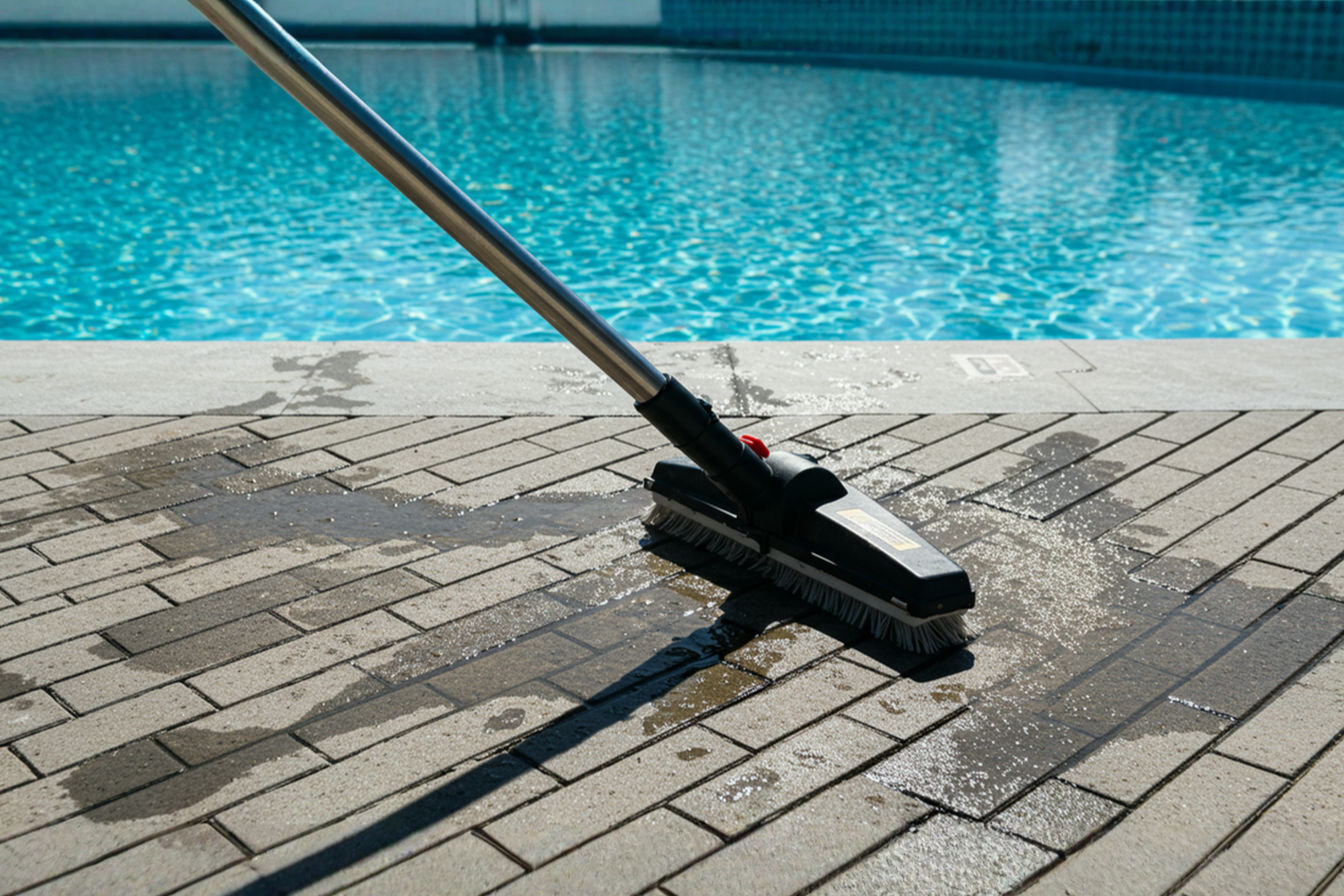
This post may contain affiliate links. If you make a purchase through these links, we may earn a commission at no additional cost to you.
Managing water and debris around swimming pools presents unique challenges that ordinary cleaning equipment simply can’t handle. Wet pool decks aren’t just difficult to clean—they’re potential safety hazards waiting to happen. One slip on a puddle can lead to serious injuries, making proper water management essential for any pool area.
That’s where specialized poolside vacuum solutions come in. These purpose-built machines tackle both dry debris and water accumulation, providing a comprehensive approach to maintaining clean, safe splash zones. Unlike standard household vacuums that can be damaged by water or pose electrical hazards in wet environments, poolside vacuums are designed specifically for the challenging conditions around swimming pools.
The right equipment doesn’t just make pool maintenance easier—it fundamentally transforms how safely and efficiently you can manage your aquatic environment. Whether you’re a homeowner with a backyard pool or a facility manager overseeing a commercial swimming center, understanding your options for poolside vacuum solutions will help you make informed decisions about this essential equipment.
In this comprehensive guide, we’ll explore everything you need to know about selecting, using, and maintaining poolside vacuum systems that effectively handle both dry and wet pickup in splash zones.
Understanding Poolside Environments and Cleanup Challenges
Unique Characteristics of Pool Areas
Pool environments create cleaning challenges unlike any other area of a property. These spaces are constantly exposed to moisture—not just from rain or humidity, but from splashing, wet feet, and evaporation processes. This persistent dampness creates a perfect breeding ground for mold, mildew, and bacteria if not properly managed.
Chemical presence is another defining feature of pool areas. Chlorine, bromine, salt (in saltwater pools), and various pH balancers leave residues on surfaces that require specialized cleaning approaches. These chemicals can be corrosive to standard equipment and may interact unpredictably with cleaning solutions.
Temperature variations add another layer of complexity. Outdoor pools experience everything from freezing conditions to extreme heat, while indoor pools create consistently humid environments that accelerate wear on equipment. These temperature fluctuations affect not only cleaning equipment performance but also how quickly spills dry or debris breaks down.
Indoor and outdoor pools present distinctly different challenges. Outdoor areas contend with natural debris like leaves, grass, and insects, while indoor facilities battle condensation and require equipment that operates quietly in enclosed spaces.
Common Debris Types in Splash Zones
The debris found around pools is as varied as it is persistent. Organic matter like leaves, grass clippings, and insects are common, especially in outdoor settings. These materials can quickly clog drains and filters if not regularly removed.
Pool chemicals and residues leave films that build up over time, requiring equipment that can handle potentially corrosive substances. These chemical residues often create slippery surfaces that standard cleaning equipment might spread rather than remove.
Human factors contribute significantly to the cleanup challenge. Sunscreen, body oils, hair, and skin cells create a biofilm that’s particularly slippery and difficult to remove with standard methods. Food and beverage spills are inevitable around recreational pools, adding sticky residues and potential staining agents to the mix.
Safety Concerns in Wet Areas
Safety must be the primary concern when selecting poolside cleaning equipment. Slip and fall hazards represent one of the most common causes of pool-related injuries. According to the National Floor Safety Institute, wet floors contribute to over one million hospital emergency room visits annually in the United States.
Electrical safety around water cannot be overstated. Standard electrical equipment poses serious shock hazards in wet environments. Proper poolside vacuum solutions must incorporate multiple layers of electrical protection to prevent potentially fatal accidents.
Sanitation and hygiene requirements add another dimension to pool area maintenance. Public and commercial pools must meet specific health department standards, requiring equipment that not only removes visible debris but also supports proper sanitization protocols.
Types of Poolside Vacuum Solutions
Traditional Wet-Dry Vacuums
Wet-dry vacuums represent the most familiar option for many pool owners. These versatile machines use powerful motors to create suction that can handle both dry debris and water spills.
At their core, wet-dry vacs operate on a simple principle: a motor drives an impeller that creates air movement, drawing water and debris through a hose into a collection tank. The key distinction from regular vacuums is the sealed collection system and internal components designed to prevent electrical components from contacting water.
Standard wet-dry vacuums offer considerable versatility for casual pool owners. They typically feature:
- Collection tanks ranging from 5 to 16 gallons
- Motors rated between 2 and 6.5 horsepower
- Basic filtration systems for capturing larger debris
- Multiple attachments for different surfaces
However, these general-purpose machines have limitations in pool environments. Their filtration may be insufficient for fine particles, and while they can handle occasional water pickup, they’re not optimized for constant wet operation. Most importantly, not all wet-dry vacs offer the electrical protection necessary for safe poolside use.
Specialized Pool Deck Vacuums
Purpose-built pool deck vacuums address the shortcomings of general-purpose wet-dry models. These specialized units feature design elements specifically engineered for the unique demands of pool environments.
The key differences begin with enhanced water handling capabilities. Pool deck vacuums often incorporate:
- Higher water lift capacity (the ability to pull water up through the hose)
- Improved water separation systems to protect motors
- Faster extraction rates for efficiently clearing large puddles
- Drain valves for easy emptying without lifting heavy water-filled tanks
Filtration systems in these specialized units are designed to capture the unique contaminants found in pool areas. Multiple filtration stages prevent fine particles like sand, dirt, and chemical residues from being recirculated, while also protecting the vacuum’s internal components.
These purpose-built systems often include features specifically for pool environments:
- Non-marking wheels that won’t scuff pool decks
- Chemical-resistant components that withstand chlorine exposure
- Specialized attachments for cleaning pool edges, furniture, and equipment
Commercial-Grade Water Extraction Systems
For commercial pools or larger residential installations, commercial-grade water extraction systems provide industrial-strength solutions. These heavy-duty machines represent a significant step up in capabilities and durability.
The most notable advantage is their higher capacity. Commercial units typically feature:
- Collection tanks of 20 gallons or more
- Dual or triple vacuum motors for enhanced suction
- High-flow pump systems for simultaneous extraction and discharge
- The ability to continuously remove water without stopping to empty tanks
Enhanced durability features make these systems suitable for daily use in demanding environments. Commercial-grade components like stainless steel tanks, reinforced housings, and commercial-rated motors significantly extend service life even under heavy use conditions.
The speed advantage of commercial systems can’t be overstated. Their powerful motors and optimized designs can clear large water spills in a fraction of the time required by consumer models, making them ideal for facilities that must minimize downtime and quickly respond to safety hazards.
Battery-Powered vs. Corded Options
The power source for your poolside vacuum significantly impacts its utility and safety. Both battery-powered and corded options have distinct advantages and limitations worth considering.
Battery-powered vacuums offer unmatched mobility. Without being tethered to an outlet, these units can easily reach every corner of a pool area without extension cord management. This freedom of movement proves particularly valuable for larger pool decks or commercial facilities with multiple pool areas. The absence of cords also eliminates a potential tripping hazard, an important safety consideration in already slippery environments.
However, battery limitations must be considered:
- Runtime constraints typically ranging from 15-60 minutes depending on the model
- Reduced suction power compared to corded equivalents
- Higher initial purchase cost
- Battery degradation over time requiring eventual replacement
Corded options deliver consistent power without runtime limitations. Their advantages include:
- Stronger, consistent suction power
- Lower initial purchase cost
- No battery replacement expenses
- No waiting for recharging between uses
The tradeoff comes with safety management challenges. Cords in pool areas require careful routing to prevent trips and falls. More critically, proper electrical protection is essential, with requirements for GFCI (Ground Fault Circuit Interrupter) protection to prevent shock hazards in wet environments.
Essential Features for Poolside Vacuum Solutions
Safety Features
When operating any electrical equipment around water, safety features aren’t optional extras—they’re essential requirements. A comprehensive understanding of these safety mechanisms can literally be lifesaving when selecting poolside vacuum equipment.
GFCI protection represents the most critical safety feature for poolside electrical equipment. These devices monitor the electrical current flowing through a circuit and automatically shut off power when they detect current leakage—which can happen when electricity contacts water. For corded vacuums, built-in GFCI plugs or connection to GFCI-protected outlets is mandatory for poolside use.
Waterproof ratings provide standardized information about equipment’s resistance to water intrusion. The IPX (Ingress Protection) rating system uses numbers to indicate protection levels:
- IPX4: Protected against splashing water
- IPX5: Protected against water jets
- IPX6: Protected against powerful water jets
- IPX7: Protected against temporary immersion
- IPX8: Protected against continuous immersion
For poolside vacuums, a minimum rating of IPX5 is recommended, with IPX6 or higher providing better protection in frequently wet environments.
Physical stability features prevent accidents during operation. Anti-tip designs with lower centers of gravity and wider bases reduce the risk of equipment toppling into pools or onto users. This stability becomes particularly important when vacuums have heavy water-filled tanks.
Insulated components provide an additional layer of electrical protection. Double-insulated systems use multiple barriers to prevent electrical contact even if outer casings become damaged. Look for UL (Underwriters Laboratories) certification, which indicates equipment has been tested against rigorous safety standards specifically for wet-environment use.
Performance Features
Understanding performance specifications helps match equipment capabilities to specific pool area needs. These technical ratings directly impact cleaning effectiveness and efficiency.
Suction power, typically measured in air watts or sealed suction (inches of water lift), determines how effectively a vacuum can pick up debris and extract water. For context, light-duty pool vacuums might offer 60-70 inches of water lift, while commercial-grade units can exceed 150 inches. Higher ratings generally indicate better performance with heavy debris and deeper water.
Water lift and airflow represent two different but complementary aspects of vacuum performance:
- Water lift (measured in inches) indicates the maximum height a vacuum can pull water up a vertical tube
- Airflow (measured in cubic feet per minute or CFM) indicates volume of air moved through the system
A balanced combination of both metrics delivers optimal performance—high water lift for puddle extraction and strong airflow for moving debris through longer hoses.
Tank capacity directly impacts operational efficiency. Smaller tanks (5-10 gallons) require more frequent emptying but are lighter and more maneuverable. Larger tanks (15+ gallons) allow longer continuous operation but become extremely heavy when filled with water. Some commercial units solve this dilemma with continuous discharge systems that pump water out as it’s collected.
Filtration efficiency determines both cleaning effectiveness and equipment longevity. Multi-stage filtration systems capture progressively smaller particles, protecting motor components while ensuring thorough cleaning. HEPA-rated filters can capture particles as small as 0.3 microns, including many bacteria and allergens—an important consideration for indoor pools where air quality is a concern.
Durability Features
Pool environments accelerate wear on equipment through constant exposure to moisture, chemicals, and sometimes harsh weather. Durability features directly impact service life and total ownership cost.
Corrosion-resistant materials should be used for all components that contact water or pool chemicals. Stainless steel tanks offer superior durability compared to plastic alternatives, though they add weight. For exterior components, look for:
- Marine-grade metals with specialized coatings
- Chemical-resistant plastics like polypropylene
- Composite materials engineered for wet environments
UV-resistant components are essential for outdoor equipment. Standard plastics can become brittle and crack after extended sun exposure, but UV-stabilized materials maintain flexibility and strength even after years in direct sunlight. This protection is particularly important for hoses, cords, and exterior housing components.
Chemical-resistant seals and gaskets prevent internal damage from pool chemicals that can degrade standard rubber components. Specialized materials like EPDM (Ethylene Propylene Diene Monomer) rubber maintain flexibility and sealing properties even when regularly exposed to chlorine and other pool chemicals.
Impact-resistant construction protects against the inevitable bumps and drops that occur during use. Reinforced housings, protected wheels, and recessed controls reduce damage risk during daily operation. Commercial-grade units often feature bumpers and crash guards to protect both the equipment and pool area furnishings during use.
Top Considerations When Choosing a Poolside Vacuum
Assessing Your Specific Needs
The “perfect” poolside vacuum varies dramatically depending on your unique situation. A systematic assessment of your specific requirements will guide you toward equipment that delivers the best value.
Pool size and type create the foundation for your needs assessment. Larger pools generate more splash zone area requiring maintenance, while specialty features like beach entries, infinity edges, or extensive decking create unique cleaning challenges. Different pool types introduce specific considerations—saltwater pools require equipment with enhanced corrosion resistance, while indoor pools benefit from quieter operation and finer filtration.
Indoor versus outdoor requirements significantly impact equipment selection. Outdoor equipment needs weather resistance and the ability to handle natural debris like leaves and twigs. Indoor pool vacuums may prioritize noise reduction and fine filtration for air quality management. Some facilities require equipment for both environments, necessitating versatile solutions or multiple specialized units.
Usage frequency directly impacts durability requirements. A vacuum used daily in a commercial setting needs considerably more robust construction than one used weekly at a residential pool. Premium components and commercial-grade construction provide better value for high-frequency use, while consumer-grade equipment may suffice for occasional operation.
Storage limitations constrain physical dimensions and design. Limited storage space might make a compact unit with folding handles essential, while abundant storage allows for larger equipment with attached accessory caddies and extended hoses.
Balancing Budget and Quality
Poolside vacuums represent a substantial investment, with price points ranging from around $200 for basic consumer models to $2,000+ for commercial-grade systems. Finding the optimal balance between cost and quality requires looking beyond the initial purchase price.
The relationship between initial investment and long-term value isn’t always straightforward. Higher-priced units often offer:
- Extended operational lifespan
- Better performance that saves labor time
- Enhanced safety features that reduce liability risks
- Lower repair frequency and maintenance costs
However, premium pricing doesn’t always guarantee proportionally better performance. The value sweet spot typically lies in mid-range commercial equipment or high-end consumer models that incorporate essential safety and durability features without specialized capabilities you may never use.
Replacement parts availability significantly impacts ownership costs. Some manufacturers use proprietary components that are expensive and difficult to source, while others utilize standardized parts available from multiple suppliers. Before purchasing, investigate:
- Typical part costs for common replacement items
- Local availability of parts and service
- Whether repairs require specialized technicians
- Manufacturer’s parts warranty policies
Warranty coverage varies dramatically between manufacturers and models. Look beyond the headline warranty period to understand what’s actually covered:
- Motor-only warranties may leave you unprotected for tank, hose, or accessory failures
- Pro-rated warranties reduce coverage over time
- On-site service versus ship-in repair requirements
- Whether commercial use voids warranty protection
The distinction between professional and consumer-grade options extends beyond price. Professional equipment typically offers:
- Serviceable components designed for repair rather than replacement
- Metal components instead of plastic at key wear points
- Standardized fittings compatible with existing equipment
- Detailed technical documentation and service manuals
Accessory Compatibility
The basic vacuum unit represents only part of an effective poolside cleaning system. Accessories dramatically expand functionality and efficiency for specific cleaning tasks.
Specialized attachments for pool areas transform a good vacuum into a comprehensive cleaning solution. Consider the value of:
- Squeegee tools for smooth surface water extraction
- Corner tools for cleaning along pool edges and stairs
- Brush attachments for scrubbing textured surfaces
- Crevice tools for cleaning expansion joints and drain covers
Extension wands and hoses expand reach without moving the main unit. This expanded reach isn’t just about convenience—it enhances safety by allowing the heavier vacuum unit to remain in a dry, stable location while cleaning extends into wetter areas. Look for:
- Telescoping wands that adjust to different heights
- Crush-resistant hoses that maintain airflow when stepped on
- Quick-connect systems for rapid tool changes
- Lightweight materials that reduce operator fatigue
Different brush types optimize cleaning for specific surfaces. Pool areas typically include multiple materials requiring different approaches:
- Soft brushes for vinyl liners and fiberglass surfaces
- Medium-stiffness brushes for concrete and plaster
- Hard brushes for removing algae and stubborn deposits
- Wide-path brushes for efficiently covering large deck areas
Storage solutions for accessories prevent loss and damage between uses. Integrated storage systems keep essential tools immediately available, while wall-mounted organizers protect equipment during off-season storage. The best storage solutions are ventilated to allow wet accessories to dry, preventing mold and mildew growth.
Best Practices for Using Vacuums in Pool Areas
Safety Protocols
Operational safety begins before you power on the equipment. Establishing consistent safety protocols protects both users and bystanders in the potentially hazardous combination of electricity and water.
Pre-operation safety checks should become routine before each use:
- Inspect cords and plugs for damage or wear
- Check hoses for cracks or splits that could leak
- Verify that all safety features are functioning
- Ensure wheels and brakes operate properly
- Confirm proper filter installation
Proper extension cord usage is critical when additional reach is needed. Always use outdoor-rated, GFCI-protected extension cords with appropriate gauge wire for the equipment’s amperage. The American Red Cross recommends a minimum 14-gauge cord for most poolside electrical equipment, with heavier 12-gauge for higher-amperage devices.
Preventing electrical hazards requires constant vigilance:
- Always plug into GFCI-protected outlets
- Keep power connections elevated and away from puddles
- Maintain awareness of cord positioning during operation
- Never operate equipment while standing in water
- Power off immediately if equipment gets submerged
Personal protective equipment provides an additional safety layer, particularly in commercial settings or when dealing with chemical residues. Basic protection includes:
- Non-slip footwear with rubber soles
- Chemical-resistant gloves when handling pool chemicals
- Eye protection when vacuuming potentially caustic materials
- Breathing protection in enclosed areas if using equipment without HEPA filtration
Efficient Cleaning Techniques
Strategic approaches to pool deck cleaning maximize efficiency while ensuring thorough results. Developing systematic methods reduces missed areas and minimizes the time required.
A systematic approach to pool deck cleaning begins with a clear plan:
- Start from the highest elevation and work downward
- Clean in overlapping patterns to ensure complete coverage
- Move from drier to wetter areas to prevent tracking debris
- Complete one section entirely before moving to the next
Managing large water spills requires specific techniques to prevent spreading contamination. Create a “dam” by vacuuming a complete path around the spill first, then work from the outside edge toward the center in increasingly smaller circles.
Different debris types require tailored approaches:
- Fine particles (sand, dirt): Use slow, deliberate passes to allow complete capture
- Larger debris (leaves, twigs): Remove largest pieces by hand before vacuuming to prevent clogs
- Oils and sunscreen residues: Pre-treat with appropriate cleaners before vacuuming
- Chemical powders: Use low airflow settings to prevent dispersal into the air
Regular tank emptying maintains optimal performance. As collection tanks fill, vacuum performance decreases significantly. Most wet-dry vacuums experience a 20-30% suction reduction when tanks reach 75% capacity. For water extraction, empty tanks when they reach 50-60% capacity to maintain maximum efficiency and prevent overly heavy lifting.
Maintenance and Care
Regular maintenance significantly extends equipment life while ensuring consistent performance. Establishing routine care procedures prevents costly repairs and unexpected downtime.
Post-use cleaning prevents long-term damage from corrosive pool chemicals and organic debris:
- Empty and rinse collection tanks thoroughly
- Clean filters according to manufacturer specifications
- Wipe down exterior surfaces to remove chemical residues
- Allow all components to dry completely before storage
- Inspect hoses and tools for damage or blockages
Filter maintenance schedules should align with usage patterns. High-use environments may require daily filter cleaning, while residential equipment typically needs weekly attention. Many professional-grade systems utilize multi-stage filtration that requires different maintenance intervals for different components.
Preserving chemical resistance requires proactive care. Chlorine and other pool chemicals gradually degrade even resistant materials. Thorough rinsing after each use significantly extends component life. For equipment used with saltwater pools, pay special attention to metal components and electrical connections, as salt residue is particularly corrosive.
Proper storage significantly impacts equipment longevity. Store equipment:
- In dry, climate-controlled environments when possible
- With tanks empty and lids removed for ventilation
- With hoses disconnected and properly drained
- Protected from direct sunlight and extreme temperatures
- With cords properly coiled to prevent insulation cracks
Seasonal maintenance for outdoor equipment should include:
- Deep cleaning of all components
- Lubrication of moving parts according to manufacturer specifications
- Inspection and replacement of worn seals and gaskets
- Motor service if recommended by the manufacturer
- Battery conditioning for battery-powered units
Common Applications and Scenarios
Residential Pool Maintenance
Home pool environments balance maintenance efficiency with practical storage and budget constraints. Effective residential maintenance typically follows scheduled routines based on usage patterns.
Daily maintenance focuses on safety and immediate cleanliness:
- Quick water extraction from high-traffic deck areas
- Removal of visible debris that could cause slips or falls
- Spot cleaning of spills or sunscreen residue
- Brief inspection for developing issues
Weekly comprehensive cleaning addresses deeper maintenance needs:
- Complete deck cleaning with appropriate attachments
- Cleaning of pool furniture and equipment
- Attention to corners, steps, and other detailed areas
- Filter cleaning and equipment maintenance
Seasonal considerations drive maintenance adjustments throughout the year. Spring typically requires pollen management, summer demands increased attention to sunscreen residues and food spills, fall introduces leaf management challenges, and winter preparation focuses on thorough cleaning before reduced use or closure.
Family-friendly safety protocols are particularly important in residential settings where children may be present:
- Store equipment with tanks empty and power disconnected
- Use lockable storage for chemicals and cleaning equipment
- Establish clear rules about equipment operation
- Create visual indicators (cones, signs) during active cleaning
- Never leave powered equipment unattended
Commercial Pool Facilities
Commercial environments face unique challenges including regulatory compliance, high-traffic management, and the need for rapid response to potential hazards.
High-traffic area management requires specialized approaches:
- Scheduled cleaning during lower-usage periods
- Sectional cleaning that allows continued facility use
- Rapid-drying techniques to minimize closure time
- More frequent cleaning of entry/exit points and shower areas
- Durable marking systems for wet areas undergoing maintenance
Health regulation compliance drives commercial cleaning protocols. Most jurisdictions follow guidelines similar to CDC Model Aquatic Health Code, which requires:
- Daily cleaning and sanitizing of pool decks and wet areas
- Documentation of cleaning schedules and procedures
- Regular testing of surfaces for bacterial contamination
- Specific procedures for bodily fluid cleanup
- Staff certification in proper cleaning techniques
Staff training considerations extend beyond basic operation to comprehensive facility management. Commercial operators should implement training programs covering equipment operation, chemical handling, hazard identification, emergency response procedures, and proper documentation practices.
Commercial equipment selection typically prioritizes:
- Rapid water extraction capabilities
- Continuous operation without frequent emptying
- Ease of transport between areas
- Durability under multiple daily uses
- Compatibility with required sanitizing chemicals
Special Event Cleanup
Pool facilities hosting events require specialized planning and equipment capabilities to maintain safety during increased usage.
Pool parties and gatherings generate unique cleaning challenges:
- Higher volumes of food and beverage spills
- Increased sunscreen and cosmetic residues
- Greater foot traffic on deck surfaces
- More paper and plastic debris
- Compressed timeframes for cleaning between events
Rapid response to spills becomes critical during events. Establishing zones with pre-positioned equipment allows immediate attention to hazards without disrupting the entire gathering. Mobile cleaning stations with basic supplies support quick attention to minor issues before they become safety hazards.
Managing high-volume cleaning needs often requires:
- Multiple smaller units rather than one large system
- Teams working simultaneously in different areas
- Simplified cleaning protocols focused on safety essentials
- Scheduled cleaning windows between event phases
- Enhanced signage and communication about wet areas
Post-event deep cleaning should address:
- Thorough extraction of all standing water
- Removal of hidden debris in corners and under fixtures
- Attention to drainage systems that may be clogged with debris
- Sanitization of all high-touch surfaces
- Complete equipment cleaning and preparation for next use
Maintenance and Troubleshooting
Regular Maintenance Schedule
Systematic maintenance extends equipment life while ensuring consistent performance. Establishing a clear schedule based on usage frequency provides a framework for proper care.
Daily tasks focus on operational readiness:
- Empty and rinse collection tanks
- Inspect filters and clean if visibly dirty
- Check hoses and attachments for blockages
- Wipe down exterior surfaces
- Verify safety features are functioning
Weekly maintenance addresses emerging wear issues:
- Thoroughly clean or replace primary filters
- Inspect electrical cords and connections
- Check wheels and brakes for proper operation
- Clean accessory tools and attachments
- Lubricate moving parts if required
**Monthly comprehensive service ensures long-term reliability:
- Deep clean all filtration components
- Inspect motor vents and cooling systems
- Check gaskets and seals for deterioration
- Verify proper function of float mechanisms
- Inspect tanks for cracks or damage**
Seasonal requirements vary by climate and usage patterns. For seasonal facilities, beginning and end-of-season service should include:
- Complete disassembly and cleaning of all components
- Inspection of all electrical systems
- Replacement of worn parts before they fail
- Motor service according to manufacturer recommendations
- Battery maintenance for battery-powered systems
Component inspection guidelines should follow manufacturer recommendations but generally include checking:
- Filter integrity and frame condition
- Hose flexibility and connection security
- Wheel free movement and brake function
- Switch and control operation
- Motor sound and temperature during operation
Common Issues and Solutions
Understanding typical problems enables rapid diagnosis and resolution, minimizing downtime and preventing minor issues from developing into major failures.
Loss of suction power commonly results from:
- Clogged filters (solution: clean or replace filters)
- Blocked hoses (solution: disconnect and clear obstructions)
- Tank overfill (solution: empty tank more frequently)
- Motor inlet obstruction (solution: clear debris from intake)
- Damaged hose (solution: repair or replace hose)
Water leakage problems typically stem from:
- Cracked tanks (solution: replace tank if cracks are present)
- Damaged gaskets (solution: replace worn gaskets and seals)
- Loose connections (solution: tighten all fittings and connections)
- Float mechanism failure (solution: repair or replace float assembly)
- Overfilled tanks (solution: maintain proper fill levels)
**Motor overheating frequently occurs due to:
- Restricted airflow (solution: ensure adequate ventilation around motor)
- Clogged cooling vents (solution: clean motor housing and vents)
- Extended operation (solution: implement cooling breaks during long use)
- Voltage issues (solution: verify proper power supply)
- Worn motor components (solution: professional service or replacement)**
Filter clogging accelerates when:
- Using incorrect filter type (solution: verify proper filter installation)
- Operating in high-debris environments (solution: consider pre-filtering large debris)
- Vacuuming fine powders (solution: use specialized fine-particle filters)
- Filters are not dried between uses (solution: allow complete drying before storage)
- Maintenance is neglected (solution: implement regular cleaning schedule)
Strange noises during operation often indicate:
- Debris in the impeller (solution: disconnect power and clear impeller)
- Loose components (solution: tighten fasteners and connections)
- Damaged bearings (solution: professional repair or replacement)
- Restricted airflow (solution: check and clear all air pathways)
- Foreign objects in tanks or hoses (solution: empty and inspect thoroughly)
When to Replace vs. Repair
Making informed decisions about repair versus replacement maximizes equipment value while ensuring safety and performance.
Cost-benefit analysis should consider:
- Current equipment age versus expected service life
- Repair cost compared to replacement price
- Availability of replacement parts
- Frequency of previous repairs
- Performance degradation even after repairs
Safety considerations may override economic factors when:
- Electrical components show signs of water intrusion
- Casings are cracked or damaged
- Overheating occurs despite maintenance
- Safety features no longer function properly
- Electrical cords show wear or damage
**Performance degradation signs that often indicate replacement is needed include:
- Consistent loss of suction despite maintenance
- Motor requiring multiple starts to activate
- Unusual odors during operation
- Excessive noise that persists after service
- Operating temperature higher than when new**
For commercial operations, equipment downtime costs should factor into decisions. The labor and revenue impact of equipment unavailability often justifies earlier replacement or maintaining backup equipment rather than attempting repairs on aging systems.
If choosing repair, always use manufacturer-approved parts and qualified service providers. Improper repairs, particularly to electrical systems, create safety hazards that may not be immediately apparent but can lead to serious accidents in wet environments.
Future Trends in Poolside Vacuum Technology
Smart Features and Connectivity
The future of poolside maintenance is increasingly connected, with intelligent features enhancing both performance and user experience.
Remote monitoring capabilities are emerging in premium equipment, allowing:
- Real-time performance tracking via smartphone apps
- Remote power control and scheduling
- GPS location tracking for commercial fleets
- Usage logs for maintenance planning
- Power consumption optimization
Automated maintenance alerts represent a significant advancement in equipment longevity. **Next-generation systems can monitor internal components and notify users before failures occur, detecting issues like:
- Reduced airflow indicating filter restrictions
- Motor temperature patterns suggesting bearing wear
- Vacuum pressure changes signaling developing leaks
- Battery performance degradation
- Unusual vibration patterns indicating mechanical problems**
Usage pattern analytics help optimize cleaning schedules and equipment deployment. Advanced systems can track:
- High-traffic areas requiring more frequent attention
- Optimal cleaning times based on facility usage
- Equipment utilization rates for fleet management
- Performance trends that indicate maintenance needs
- Energy consumption patterns for efficiency improvement
Eco-Friendly Innovations
Environmental considerations are driving numerous advances in poolside vacuum technology, reflecting broader sustainability trends.
Energy efficiency improvements focus on doing more with less power:
- Brushless motors providing better performance with lower energy consumption
- Smart power management that adjusts suction based on debris load
- Solar-charging options for battery-powered equipment
- High-efficiency filtration requiring less motor power
- Optimized airflow pathways reducing energy requirements
Sustainable materials are increasingly incorporated into equipment design:
- Recycled plastics for non-critical components
- Biodegradable options for disposable filters
- Longer-lasting components reducing replacement waste
- Modular designs that allow partial replacement rather than complete unit disposal
- Materials requiring less energy-intensive manufacturing processes
**Reduced water usage in self-cleaning systems represents a significant advancement, particularly in water-conscious regions. Newer technologies incorporate:
- Cyclonic separation reducing filter rinse requirements
- Reusable filters that can be cleaned without water
- Grey water recycling for filter cleaning processes
- Electrostatic filtration systems requiring minimal water
- Moisture-sensing systems that optimize water extraction**
Integration with Pool Management Systems
The siloed approach to pool equipment is giving way to integrated systems that enhance overall facility management.
Connected pool equipment ecosystems link vacuums with:
- Water chemistry management systems
- Pool heating and pump controls
- Lighting and ambient systems
- Access control and safety monitoring
- Energy management platforms
Centralized control systems provide unified interfaces for all pool operations:
- Single-app control of multiple equipment types
- Coordinated maintenance scheduling
- Integrated alert systems
- Performance analytics across all systems
- Resource optimization across connected equipment
**Data-driven maintenance scheduling uses real-time information to optimize operations:
- Predictive maintenance based on actual usage rather than calendar schedules
- Coordination of cleaning with chemical treatments for enhanced effectiveness
- Optimization of maintenance timing based on facility usage patterns
- Resource allocation prioritizing highest-need areas
- Service verification through equipment usage logs**
These integrated approaches particularly benefit commercial operations, where coordinated systems can significantly reduce operating costs while improving safety and user experience.
Conclusion
Maintaining clean, safe pool areas requires specialized equipment designed for the unique challenges of wet environments. The right poolside vacuum solution doesn’t just remove water and debris—it fundamentally transforms facility management by enhancing safety, efficiency, and user experience.
Throughout this guide, we’ve explored the essential considerations for selecting, using, and maintaining poolside vacuum systems. From understanding the unique characteristics of pool environments to exploring cutting-edge technology trends, we’ve provided a comprehensive framework for making informed decisions about this critical equipment.
The value of proper equipment investment extends far beyond simple cleanliness. Appropriate poolside vacuum solutions reduce slip-and-fall risks, extend the life of pool deck surfaces, maintain sanitary conditions, and allow faster recovery from weather events or heavy usage periods. For commercial facilities, the right equipment can meaningfully impact insurance costs, regulatory compliance, and customer satisfaction.
As you evaluate your specific needs, remember that the ideal solution balances performance, safety, and durability within your budget constraints. Whether you’re managing a residential pool, a commercial aquatic center, or a hotel facility, taking the time to select appropriate equipment pays dividends through enhanced safety, reduced maintenance costs, and improved operational efficiency.
Pool environments will always present unique cleaning challenges, but with the right equipment and maintenance practices, you can transform splash zones from potential hazards into safe, enjoyable spaces for all users.