Next-Generation Battery Technology: Solid State Cells in Vacuum Applications
Solid state batteries eliminate the fundamental limitations of conventional cells in vacuum, offering superior performance, safety, and longevity for space exploration and beyond.
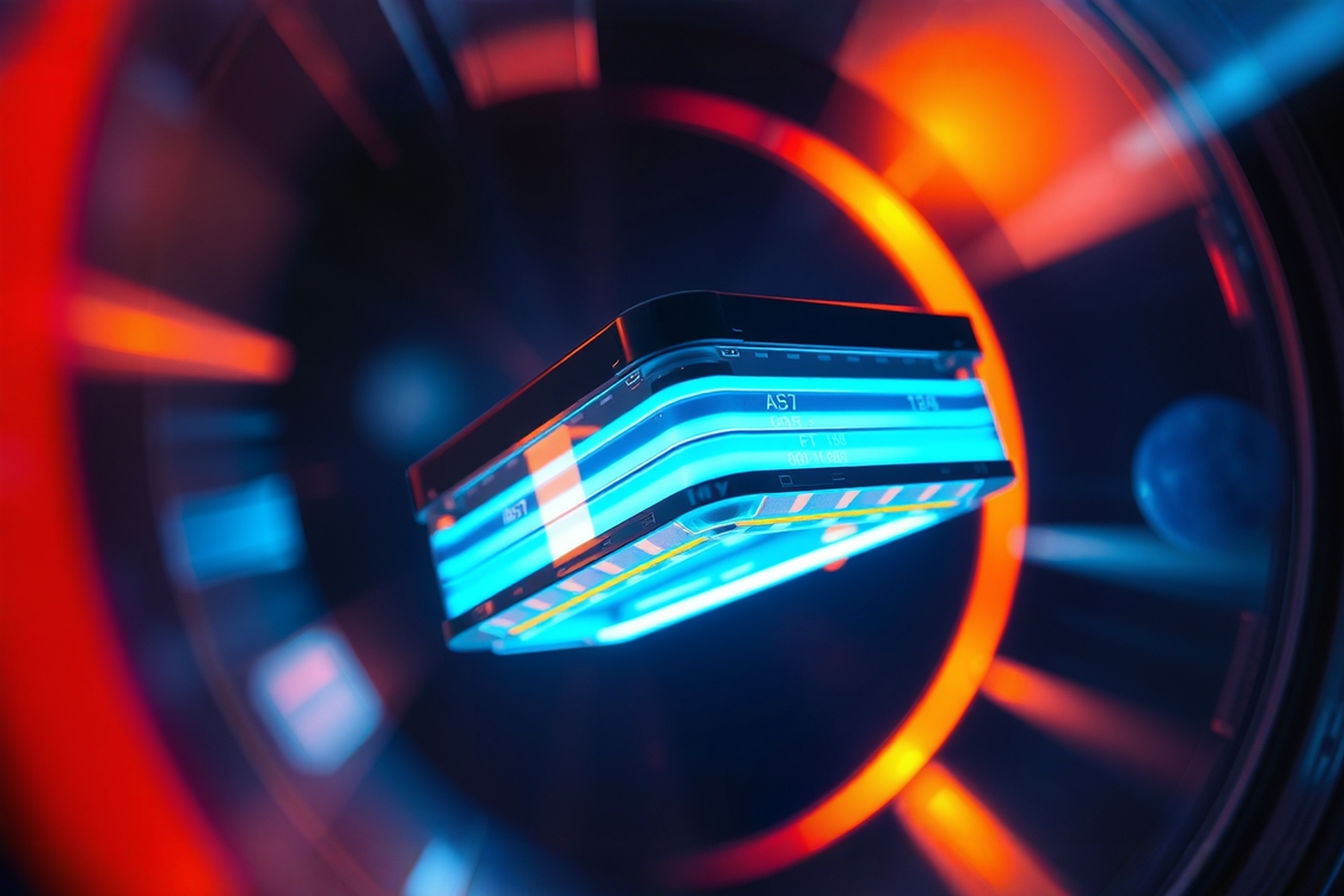
This post may contain affiliate links. If you make a purchase through these links, we may earn a commission at no additional cost to you.
The quest for reliable energy storage in vacuum environments presents unique challenges that conventional battery technologies struggle to overcome. Whether in the cold vacuum of space, inside scientific instruments, or within specialized manufacturing equipment, traditional batteries with liquid electrolytes face fundamental limitations that compromise their performance, reliability, and safety. These environments demand power solutions that can withstand extreme conditions without degradation or catastrophic failure.
Solid state battery technology has emerged as a promising solution to these challenges. By replacing liquid components with solid materials, these next-generation cells offer inherent advantages that make them particularly well-suited for vacuum applications. The stakes are high—from powering multi-billion dollar space missions to enabling breakthrough scientific research—and the potential benefits extend far beyond simple improvements in energy density or cycle life.
This article explores the transformative potential of solid state cells in vacuum applications, examining the underlying material science, performance characteristics, current state of development, and future outlook. Whether you’re a researcher, engineer, or technology enthusiast, understanding this cutting-edge battery technology will provide valuable insights into the future of energy storage in some of humanity’s most challenging environments.
Understanding Solid State Batteries
What Sets Solid State Batteries Apart
Solid state batteries represent a fundamental shift in energy storage design. Unlike conventional lithium-ion batteries that use liquid electrolytes, solid state cells employ solid materials to facilitate ion movement between electrodes. This seemingly simple change creates a cascade of performance benefits, especially in demanding environments like vacuum.
The anatomy of a solid state battery includes three primary components:
- A solid electrolyte (typically ceramic, glass, or sulfide-based materials)
- A cathode (positive electrode)
- An anode (negative electrode)
The key difference lies in the electrolyte—the medium through which ions travel during charging and discharging. Traditional batteries use organic liquid electrolytes that can leak, evaporate, or decompose. Solid state batteries eliminate these vulnerabilities by using stable solid materials instead.
How Solid State Batteries Work
The basic operating principle remains similar to conventional batteries but with important distinctions. During discharge, lithium ions move from the anode through the solid electrolyte to the cathode, creating an electrical current in an external circuit. During charging, this process reverses.
What makes this technology special is how the solid electrolyte conducts ions. In technical terms, these materials contain a crystalline structure with vacant sites that allow lithium ions to “hop” from one position to another. This mechanism, known as ionic conductivity, allows charge carriers to move efficiently without the need for liquid components.
For those without technical backgrounds, you can think of it like a busy highway versus a network of side streets. Liquid electrolytes provide a “highway” where ions move freely but can cause traffic jams (dendrite formation) or accidents (short circuits). Solid electrolytes offer carefully designed “side streets” that guide ions safely while preventing unwanted reactions.
The Vacuum Environment Challenge
What Makes Vacuum Environments Difficult
Vacuum presents a particularly hostile setting for energy storage technologies. By definition, a vacuum is a space devoid of matter—including air—where pressure is significantly lower than atmospheric conditions. These environments exist naturally in space and are artificially created in scientific instruments, manufacturing processes, and research facilities.
The challenges vacuum creates for batteries include:
- Outgassing: Materials release trapped gases when exposed to vacuum, changing their properties
- Heat management: Without air for convection, heat must be dissipated through radiation or conduction only
- Extreme temperatures: Vacuum environments often feature dramatic temperature swings
- Pressure differentials: Components must withstand internal/external pressure differences
- Radiation exposure: In space applications, radiation can degrade materials over time
Why Conventional Batteries Fail in Vacuum
Traditional lithium-ion batteries with liquid electrolytes face fundamental problems in vacuum conditions that compromise both performance and safety.
The most critical issue is electrolyte evaporation. Liquid electrolytes have vapor pressure, meaning they naturally want to evaporate when exposed to vacuum. Battery casings must be perfectly sealed to prevent this, but even microscopic leaks can lead to electrolyte loss over time. As the electrolyte evaporates, battery performance degrades until eventual failure.
Additionally, liquid electrolytes can outgas in vacuum, releasing volatile compounds that may contaminate sensitive equipment nearby. This is particularly problematic in scientific instruments where even trace contaminants can compromise experiments.
Temperature management presents another major hurdle. Without atmospheric convection to remove heat, batteries can experience thermal runaway—a dangerous condition where rising temperatures trigger chemical reactions that generate more heat in a potentially catastrophic cycle.
These issues aren’t just theoretical concerns. They’ve plagued space missions, vacuum-based manufacturing, and scientific research for decades, limiting operational capabilities and driving the need for alternative solutions.
Material Science Behind Solid State Cells
Solid Electrolyte Materials
The heart of any solid state battery is its electrolyte—the solid material that conducts ions between electrodes. Several material classes have emerged as promising candidates, each with distinct properties and advantages.
Ceramic electrolytes like LLZO (lithium lanthanum zirconate oxide) and LATP (lithium aluminum titanium phosphate) offer excellent chemical stability and can withstand extreme temperatures. These materials feature a crystalline structure that creates pathways for lithium ions to move through. Their rigidity also helps prevent dendrite formation—the needle-like structures that can cause short circuits in batteries.
Glass and glass-ceramic electrolytes combine the benefits of both materials. Examples include LGPS (lithium germanium phosphorus sulfide) and LPS (lithium phosphorus sulfide). These materials can be manufactured with fewer grain boundaries—the interfaces between crystal structures that often impede ion movement.
Sulfide-based solid electrolytes like Li₂S-P₂S₅ offer some of the highest ionic conductivities among solid materials, approaching the levels of liquid electrolytes. However, they’re also more reactive with air and moisture, requiring careful handling and packaging.
Polymer-based solid electrolytes provide flexibility and easier manufacturing, though they typically have lower ionic conductivity than inorganic alternatives. Recent advances in composite polymer-ceramic electrolytes aim to combine the best properties of both materials.
Interface Engineering Challenges
One of the most significant technical hurdles in solid state battery development involves the interfaces between components. Unlike liquid electrolytes that can easily conform to electrode surfaces, solid materials create distinct boundaries that can impede ion movement.
The electrode-electrolyte interface must maintain perfect contact despite mechanical stresses, temperature changes, and repeated charging cycles. Any separation or cracking at these interfaces creates resistance that reduces battery performance.
Scientists are addressing these challenges through several approaches:
- Buffer layers that create gradual transitions between materials
- Surface coatings that improve compatibility between components
- Pressure-maintaining designs that ensure solid-solid contact even as materials expand and contract
- Nanostructured interfaces that maximize contact area
These material science innovations are particularly valuable in vacuum applications, where the absence of atmospheric pressure can exacerbate interface separation issues.
Performance Advantages in Vacuum
Energy Density Improvements
Solid state batteries offer significant energy density advantages over conventional designs—a crucial benefit for vacuum applications where weight and volume constraints are often severe.
In technical terms, solid state cells can achieve theoretical energy densities exceeding 1,000 Wh/kg (watt-hours per kilogram) compared to the 250-300 Wh/kg limit of today’s best lithium-ion batteries. This improvement comes from two primary sources:
- Compatibility with lithium metal anodes, which store more energy per unit weight than graphite anodes used in conventional batteries
- Elimination of unnecessary components like separators and liquid containment structures
In practical terms, this means spacecraft, satellites, and vacuum-based equipment can either operate longer on a single charge or carry smaller, lighter batteries for the same operation time—a crucial advantage when every gram matters.
Temperature Stability
Perhaps the most valuable advantage for vacuum applications is the exceptional temperature stability of solid state batteries. Unlike liquid electrolytes that freeze at low temperatures or boil at high temperatures, solid electrolytes remain stable across extreme ranges.
Many solid electrolyte materials can function from -100°C to over 200°C without phase changes or performance degradation. This stability eliminates the need for complex thermal management systems in vacuum environments, where temperature control is already challenging.
For space applications specifically, this means batteries can withstand the dramatic temperature swings between sun-facing and shadow-facing orientations without protection. For scientific instruments, it enables operation in cryogenic or high-temperature vacuum chambers without battery limitations.
Safety Enhancements
Safety considerations become particularly critical in vacuum environments, where battery failures can be catastrophic and impossible to address quickly.
Solid state batteries eliminate several major safety risks:
- No flammable liquid electrolytes that can ignite
- No risk of electrolyte leakage contaminating sensitive equipment
- Minimal thermal runaway potential due to better thermal stability
- Higher mechanical resilience against physical damage
These safety improvements translate to more reliable operation in high-stakes applications like space missions, where battery failures have historically caused mission-ending events.
Extended Cycle Life
Vacuum applications often require exceptional durability, as maintenance or replacement may be impossible once deployed. Solid state batteries show promising improvements in cycle life—the number of charge-discharge cycles a battery can endure before significant capacity loss.
While conventional lithium-ion batteries typically last 1,000-2,000 cycles, some solid state designs have demonstrated potential for 5,000-10,000 cycles in laboratory settings. This longevity stems from reduced side reactions, minimal electrode degradation, and superior mechanical stability.
For long-duration space missions or remote scientific installations, this extended lifespan could mean the difference between success and failure. It also reduces lifetime costs for vacuum-based industrial applications that operate continuously for years.
Specific Vacuum Applications
Aerospace and Satellite Systems
The space industry stands to benefit enormously from solid state battery technology. Current satellites and spacecraft rely heavily on lithium-ion batteries that require extensive protection against vacuum conditions, adding weight and complexity.
Low Earth Orbit (LEO) satellites face repeated temperature cycles as they move between sunlight and Earth’s shadow. Solid state batteries can withstand these cycles without degradation, potentially extending operational lifespans by years.
Deep space missions encounter extreme cold that conventional batteries cannot tolerate without heating systems. Solid state cells that function at low temperatures could reduce power needs and enable missions to more distant targets.
Human spaceflight applications benefit from the safety improvements, as battery fires in the confined environment of a space habitat would be catastrophic.
Several aerospace companies are actively testing solid state cells for future missions, with potential deployment in the next 3-5 years for non-critical systems and 5-10 years for primary power.
Scientific Instruments
Vacuum-based scientific instruments represent another high-value application for solid state battery technology.
Electron microscopes require ultra-high vacuum conditions and extremely stable power sources. Battery-powered components inside these instruments could benefit from solid state technology’s resistance to outgassing and electromagnetic interference.
Particle accelerators use vacuum chambers to allow particles to travel without collisions. Sensors and instrumentation throughout these massive facilities could leverage solid state batteries for more reliable operation.
Space telescopes and other orbital observatories need power systems that function reliably for decades without service. The extended lifespan and temperature tolerance of solid state batteries make them ideal candidates for next-generation instruments.
Vacuum Manufacturing
Industrial vacuum processes stand to benefit significantly from improved energy storage options.
Semiconductor fabrication occurs in ultra-clean vacuum environments where even microscopic contamination can ruin expensive components. Battery-powered equipment in these settings must be absolutely reliable and contamination-free—requirements that solid state technology can better satisfy.
Vacuum deposition systems used for coating optical components, solar panels, and electronic devices often operate in batch processes. More energy-dense batteries could enable longer production runs without interruption.
Space manufacturing, an emerging field focused on producing materials in orbit that can’t be made under Earth’s gravity, will require robust power solutions that can function reliably in space vacuum.
Current State of Development
Research Breakthroughs
The past five years have seen remarkable advances in solid state battery technology, bringing vacuum applications closer to practical reality.
In 2022, researchers at the University of California San Diego demonstrated a solid electrolyte material that maintained 90% of its ionic conductivity even at temperatures as low as -40°C—a crucial breakthrough for space applications. The team used a composite approach combining ceramic and polymer materials to achieve this performance.
Scientists at Toyota Research Institute have developed sulfide-based solid electrolytes with room-temperature ionic conductivities exceeding those of liquid electrolytes. Their approach uses precisely controlled interfaces that minimize resistance between components.
A team at MIT recently published work on a solid state design specifically engineered for vacuum environments, incorporating radiation-resistant materials and novel thermal management approaches that leverage vacuum’s inherent properties rather than fighting against them.
Commercial Developments
Several companies are approaching commercialization of solid state batteries, though vacuum-specific applications remain largely in the development phase.
QuantumScape, backed by Volkswagen, has demonstrated solid state cells with remarkably fast charging capabilities and high energy density. While their initial focus is automotive applications, the company has indicated interest in aerospace markets.
Solid Power, partnered with BMW and Ford, is scaling up production of sulfide-based solid electrolytes. Their manufacturing process is particularly noteworthy for its compatibility with existing battery production equipment, potentially accelerating commercial deployment.
Blue Current, a startup focused specifically on extreme environment applications, has developed prototype cells for space and scientific applications. Their design incorporates vacuum-compatible sealing techniques and materials specifically selected for radiation resistance.
Toyota, Samsung, and LG are all investing heavily in solid state technology, with Toyota planning limited commercial release for specialized applications as early as 2025-2026.
Remaining Challenges
Despite remarkable progress, several challenges must be addressed before solid state batteries can fully realize their potential in vacuum applications:
- Manufacturing scalability remains limited, with many promising materials difficult to produce in large quantities
- Cost reduction is necessary, as current prototype cells can cost 10-100x more than conventional batteries
- Long-term performance verification in actual vacuum environments is still ongoing, with limited flight heritage
- Interface stability under repeated thermal cycling needs further improvement
- Integration with existing power systems requires standardization efforts
Industry experts suggest these hurdles will be overcome in stages, with initial commercial applications in high-value niches where performance advantages outweigh cost considerations.
Future Outlook and Technological Trajectory
Next Five Years (2025-2030)
The near-term outlook for solid state batteries in vacuum applications shows promising developments on multiple fronts.
We can expect the first specialized commercial applications to emerge in high-value sectors like scientific instruments and satellite subsystems. These initial deployments will likely use hybrid designs that incorporate solid electrolytes in otherwise conventional battery architectures.
Manufacturing capabilities will expand significantly, with production costs dropping as processes mature. Early estimates suggest a 30-50% cost reduction by 2030 as economies of scale take effect.
Several space missions scheduled for the late 2020s have already specified solid state batteries for secondary power systems, providing valuable operational data that will inform future designs.
Long-Term Potential (2030 and Beyond)
Looking further ahead, solid state technology could fundamentally transform vacuum-based applications across industries.
By the mid-2030s, we may see solid state batteries becoming the standard for all new satellite deployments, with energy densities exceeding 500 Wh/kg in flight-qualified designs—nearly double today’s best space-rated batteries.
Advanced manufacturing techniques, possibly including in-space production, could enable custom battery designs optimized for specific vacuum applications rather than adapted from terrestrial products.
Integration with other emerging technologies like high-efficiency solar cells, advanced thermal management materials, and artificial intelligence for power management could create energy systems that far surpass current capabilities.
The ultimate potential may lie in completely new applications that aren’t feasible with current technology—from self-powered vacuum sensors that operate for decades without maintenance to energy storage solutions that actively leverage vacuum conditions rather than simply surviving them.
Conclusion
Solid state batteries represent a perfect match for the unique demands of vacuum environments. By eliminating the fundamental limitations of liquid electrolytes, these next-generation energy storage devices offer improvements across every important performance metric—from energy density and temperature stability to safety and longevity.
While commercialization challenges remain, the trajectory is clear: solid state cells will progressively replace conventional batteries in vacuum applications over the coming decade, enabling new capabilities in space exploration, scientific research, and industrial processes.
For engineers and scientists working with vacuum systems, understanding this technology’s potential and limitations will be increasingly valuable. The transition won’t happen overnight, but when it comes to beating the vacuum challenge, solid state batteries have clearly emerged as the technology to watch.
The future of energy storage in vacuum isn’t just about incremental improvements to existing solutions—it’s about rethinking the fundamental approach to power in some of humanity’s most challenging environments. Solid state technology provides exactly that opportunity.