Maintenance Supply Organization: Creating a Complete Vacuum Care Station
Learn how to transform disorganized vacuum maintenance into a streamlined system that saves time, extends equipment life, and improves cleaning results—all with a properly designed care station.
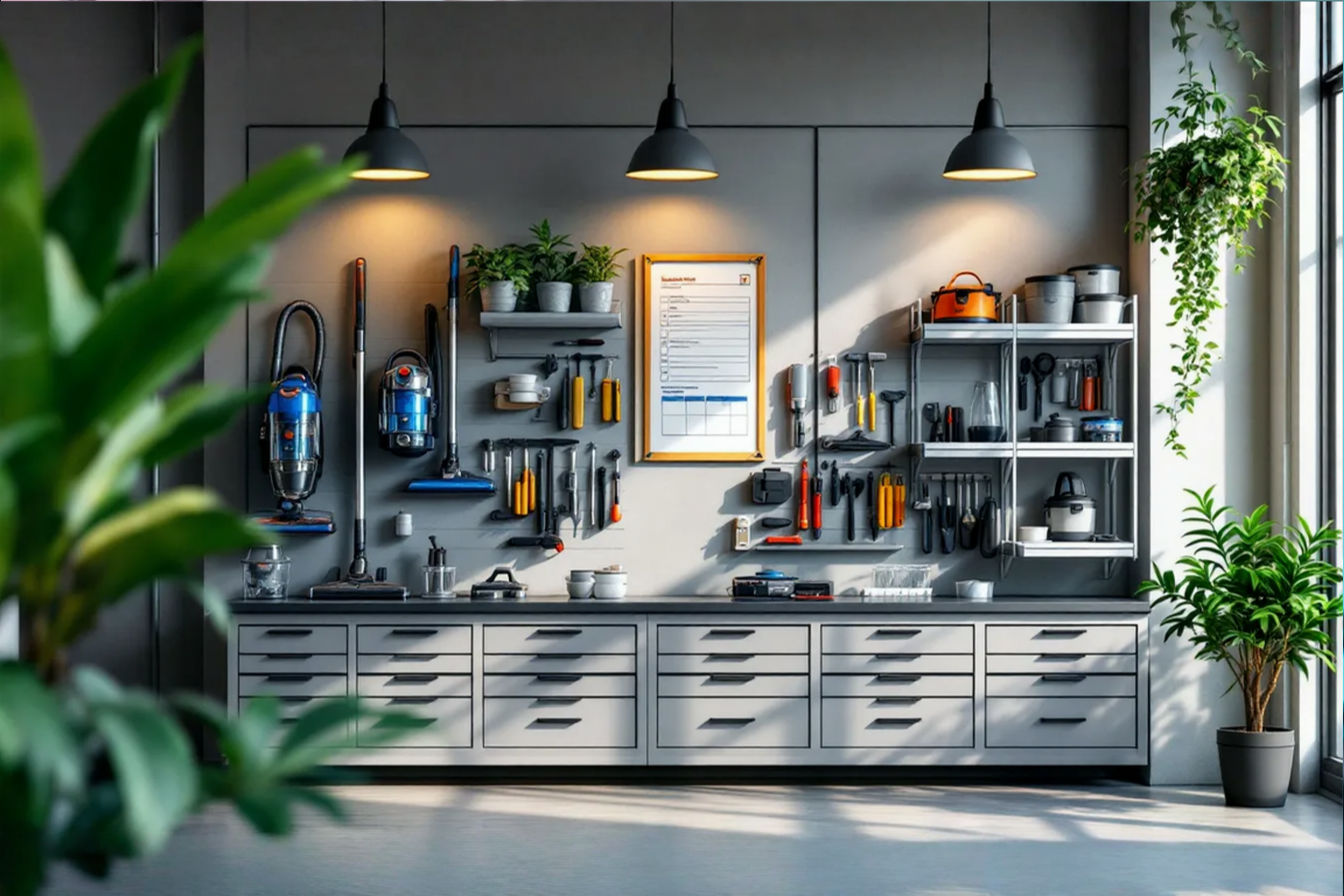
This post may contain affiliate links. If you make a purchase through these links, we may earn a commission at no additional cost to you.
In any maintenance operation, the proper care and organization of cleaning equipment plays a crucial role in operational efficiency. Among these tools, vacuum cleaners represent a significant investment that requires systematic maintenance to ensure longevity and optimal performance. Establishing a dedicated vacuum care station transforms haphazard maintenance into a streamlined process that saves time, extends equipment life, and improves cleaning results. This comprehensive guide explores how to design, implement, and optimize a complete vacuum care station that meets your organization’s specific needs.
Understanding the Need for a Vacuum Care Station
Organizations often underestimate the impact of disorganized vacuum maintenance practices. When vacuum cleaners and their associated supplies are scattered across different storage areas, maintenance becomes inconsistent and time-consuming. Technicians waste valuable minutes searching for replacement parts, appropriate tools, or specific attachments. This inefficiency not only decreases productivity but also leads to premature equipment failure.
A properly organized vacuum maintenance center provides numerous advantages. Regular maintenance performed at a dedicated station can extend equipment lifespan by up to 40%, according to industry estimates. The financial implications are substantial – replacing a commercial vacuum cleaner can cost between $300 and $1,500, while proper maintenance might cost just a fraction of that amount annually.
Beyond financial considerations, an organized care station improves cleaning effectiveness. Vacuums operating at peak performance remove more contaminants, contributing to better indoor air quality and cleaner facilities. Staff satisfaction also increases when equipment consistently works as expected, reducing frustration and improving morale.
Essential Components of a Complete Vacuum Care Station
Creating an effective vacuum care station requires thoughtful consideration of several core components that work together to support comprehensive maintenance activities.
Storage infrastructure forms the foundation of any vacuum maintenance area. This includes appropriately sized shelving or racking systems to accommodate vacuum units of various sizes and designs. Vertical storage solutions maximize available space while keeping vacuum units accessible and organized. Consider adjustable shelving that can adapt as your equipment inventory changes over time.
Maintenance supplies represent another crucial component. These include replacement belts, filters, bags, and other consumable parts specific to your vacuum models. Cleaning agents for vacuum components, lubricants for moving parts, and specialty tools for disassembly and repair should be readily available. Diagnostic tools such as airflow meters may prove valuable for performance monitoring.
Organizational elements tie the system together. These include clear labeling systems, parts bins, drawer organizers, and documentation storage. A maintenance log system, whether paper-based or digital, helps track service history and upcoming maintenance needs. Visual management tools such as shadow boards for tools or color-coding systems enhance efficiency and accountability.
Work surfaces provide the necessary space for maintenance activities. A sturdy workbench at proper height reduces physical strain during maintenance tasks. Adequate lighting, particularly adjustable task lighting, ensures visibility for detailed work. Consider incorporating electrical outlets for testing vacuums after service and compressed air access for cleaning internal components.
Selecting the Ideal Location for Your Vacuum Care Station
The effectiveness of your vacuum maintenance center begins with its location. Several factors should influence this critical decision to ensure maximum utility and adoption.
Space requirements vary based on your operation’s size and vacuum inventory. At minimum, allow enough room for your largest vacuum to be fully disassembled on a work surface with adequate clearance around all sides. Additional space for storage, movement, and potentially multiple simultaneous maintenance activities may be necessary for larger operations.
Proximity considerations balance accessibility with practical constraints. The ideal location provides convenient access from cleaning areas to minimize transport time while remaining separate enough to prevent disruption of regular operations. For multi-floor facilities, consider whether centralization on one floor or distributed maintenance points would better serve operational needs.
Environmental factors significantly impact maintenance activities. The selected area should have adequate ventilation for activities that generate dust or require cleaning solutions. Controlled temperature prevents extreme conditions that might affect adhesives or other maintenance materials. Sound considerations may necessitate some isolation if vacuum testing creates disruptive noise levels.
Facility type adaptations reflect the unique needs of different environments. Healthcare facilities might require additional infection control measures in maintenance areas. Educational institutions may need secured access to prevent unauthorized use. Manufacturing environments might need dust-control measures to prevent cross-contamination with sensitive production areas.
Designing Your Vacuum Maintenance Center Layout
The physical arrangement of your vacuum care station significantly impacts workflow efficiency and maintenance effectiveness. Thoughtful design principles create a space that supports organized, systematic equipment care.
Workflow efficiency begins with logical process sequencing. Position components to support the natural progression of maintenance tasks, from initial inspection to final testing. The design should minimize unnecessary movement, reaching, or searching for supplies. Consider arranging the space in functional zones – receiving/inspection, maintenance work, parts storage, and completed equipment staging.
Ergonomic design elements prevent strain and injury during maintenance activities. Work surfaces should position equipment at a comfortable height (typically 36-42 inches) to reduce back strain. Tool storage should keep frequently used items within easy reach without stretching. Adequate lighting reduces eye strain during detailed work, while anti-fatigue mats provide comfort during extended standing.
Scaling considerations ensure your design accommodates your operation’s specific needs. Small operations might utilize a compact, wall-mounted system with essential tools and limited inventory. Medium-sized facilities often benefit from a dedicated workbench with surrounding storage. Large operations might require multiple work stations with comprehensive inventory systems and specialized diagnostic equipment.
Modular approaches allow for adaptation as needs evolve. Consider using mobile carts or adjustable shelving systems that can be reconfigured. Standardized storage containers enable easy reorganization and expansion. This flexibility proves particularly valuable as equipment inventories change or maintenance processes evolve over time.
Storage Solutions for Vacuum Units
Proper storage of vacuum cleaners themselves represents a fundamental aspect of a complete care station. Different vacuum types present unique storage challenges that require tailored solutions.
Upright vacuum storage typically works best with vertical hanging systems or dedicated floor space with stabilizing features. Wall-mounted holders that support the vacuum by its handle keep units accessible while minimizing floor space usage. Consider cord management systems to prevent tangling and tripping hazards. Units with removable components may benefit from nearby small parts storage.
Canister vacuum considerations focus on preventing hose damage and component separation. Coiled hose storage prevents kinking while keeping hoses compact. Attachment caddies keep accessories organized and associated with the correct unit. Power cord management systems prevent damage from improper wrapping or storage.
Backpack and specialty vacuum organization addresses unique form factors. Custom wall mounts or shelving configured to these irregular shapes prevents damage from improper positioning. Battery-powered units should include charging station integration within the storage system. Specialized tools or components should remain with their associated units for easy access.
Multi-unit storage strategies become essential for operations maintaining numerous vacuums. Systematic identification methods ensure each unit can be quickly located and tracked. Consider organizing by department, area served, or vacuum type depending on your operational structure. Clear visual management systems help maintain order even with high equipment turnover.
Organizing Vacuum Accessories and Attachments
Vacuum attachments often represent the most challenging components to organize due to their quantity, variety, and frequency of use. Systematic organization approaches prevent lost or damaged accessories while ensuring quick access.
Effective categorization systems group similar items together in logical arrangements. Consider organizing by function (floor tools, upholstery tools, dusting tools), by vacuum model compatibility, or by frequency of use. This logical grouping reduces search time and encourages proper return after use. For multi-user environments, consider photographic reference guides showing correct storage locations.
Visibility solutions ensure accessories can be quickly located and inventory status easily assessed. Clear storage containers allow visual identification without opening. Pegboard systems display tools in plain sight while keeping them organized. Shadow boards or outlined storage locations immediately reveal missing items, improving accountability.
Quick-access arrangements position frequently used attachments for convenient retrieval. Consider placing these items at eye level in easily opened containers. Magnetic strips can hold metal attachments for instant visibility and access. Drawer dividers or small parts organizers prevent items from becoming jumbled while maintaining separation.
Comprehensive labeling provides information beyond simple identification. Labels should include not only the attachment name but also compatible vacuum models where appropriate. Color-coding systems can indicate department ownership, cleaning level classification, or compatibility groupings. Consider durable label materials that withstand frequent handling and occasional cleaning.
Creating a Vacuum Parts Inventory System
Maintenance efficiency depends significantly on having the right replacement parts available when needed. A well-designed inventory system prevents downtime while controlling costs.
Essential replacement parts vary by vacuum model but typically include filters (HEPA, pre-motor, post-motor), belts, bags, brushrolls, and common wear items like gaskets or wheels. For each model in your inventory, identify manufacturer-recommended replacement schedules and stock accordingly. Usage patterns unique to your facility may necessitate higher quantities of certain items based on historical replacement needs.
Inventory tracking methods range from simple visual systems to sophisticated software solutions. Minimum/maximum inventory markers provide visual cues when reordering is necessary. Barcode systems enable quick scanning for inventory updates. For larger operations, inventory management software might integrate with broader maintenance management systems for comprehensive tracking.
Effective reordering systems prevent stockouts while controlling inventory costs. Consider implementing automatic reorder points based on typical lead times and usage rates. Vendor relationships might include vendor-managed inventory options where suppliers monitor and replenish stock automatically. Standardized reorder procedures ensure consistency regardless of who initiates the process.
Strategic parts categorization improves accessibility and reduces search time. Organize parts by vacuum model, by component type, or by replacement frequency depending on your operation’s specific needs. Clear labeling with part numbers and compatible models prevents errors during selection. Reference guides showing installation procedures alongside stored parts facilitate correct usage.
Maintenance Supply Management
Beyond vacuum-specific parts, effective maintenance requires appropriate supplies and tools that must be systematically organized and maintained.
Essential cleaning agents support thorough vacuum maintenance. These typically include microfiber cloths for dust removal, approved cleansers for exterior surfaces, specialized solutions for removing hair and debris from brushrolls, and compressed air for internal component cleaning. Safety considerations should dictate appropriate storage of any chemical agents, including secondary containment where required by regulations.
Tool organization ensures necessary items remain available and in good condition. Common tools include screwdrivers in various sizes, pliers, scissors, cleaning brushes, and specialized tools required for your specific vacuum models. Consider shadow boards that show proper placement or foam-cut tool organizers that make missing items immediately apparent. Regular inspection of tool condition prevents damage from using worn or broken tools.
Supply rotation practices prevent waste from deteriorated or expired materials. Implement first-in-first-out (FIFO) usage patterns for items with limited shelf life. Clear dating systems identify when items entered inventory. Regular audits identify and remove damaged or outdated supplies that might compromise maintenance quality.
Bulk supply considerations balance cost savings against storage constraints. High-use items like vacuum bags or filters might warrant bulk purchasing, while specialty items used infrequently might be ordered as needed. Proper storage conditions prevent damage to bulk supplies – consider humidity control for paper products and temperature stability for cleaning solutions or lubricants.
Implementing a Vacuum Maintenance Schedule
Systematic maintenance prevents unexpected equipment failure and extends vacuum lifespan. A well-designed maintenance schedule transforms reactive repairs into proactive care.
Routine inspection protocols establish regular check points for each vacuum unit. Daily user checks might include examining for visible damage, ensuring proper bag/container emptying, and checking for unusual noises or performance issues. Weekly inspections might examine filters, brushrolls, and attachments for wear or blockages. Monthly comprehensive evaluations could include power testing, airflow assessment, and complete disassembly for internal inspection.
Preventative maintenance checklists detail specific tasks at predetermined intervals. These should align with manufacturer recommendations while incorporating insights from your specific operating environment. Checklists typically include tasks like filter replacement, belt inspection, brushroll cleaning, motor assessment, and wiring examination. Custom checklists for each vacuum model ensure all components receive appropriate attention.
Service documentation methods create accountability and historical records. Digital or paper maintenance logs should track dates of service, work performed, parts replaced, and technician identification. This documentation proves invaluable for identifying patterns of wear, justifying replacement decisions, and validating warranty claims when necessary. Consider photographic documentation of unusual findings or significant repairs for future reference.
Task assignment strategies ensure maintenance responsibilities are clearly defined. Options include dedicated maintenance personnel, rotating responsibilities among cleaning staff, or hybrid approaches based on task complexity. Clear role definitions prevent confusion about who handles specific maintenance requirements. Training provision ensures all assigned personnel possess the necessary skills for their responsibilities.
Vacuum Care Station Safety Considerations
Safety must remain paramount in vacuum maintenance operations. Thoughtful planning identifies and mitigates potential hazards before they cause injury or damage.
Electrical safety provisions address common hazards associated with powered equipment. These include proper grounding for workbenches, GFCI protection for outlets, clear procedures for lockout/tagout during repairs, and appropriate storage for electrical components. Consider implementing inspection procedures for power cords and plugs as part of routine maintenance activities.
Chemical safety guidelines protect personnel from hazardous substances. All maintenance chemicals should have readily accessible Safety Data Sheets (SDS). Appropriate personal protective equipment should be available where required. Storage should follow regulatory requirements for incompatible chemicals, and clear labeling should identify potential hazards. Consider secondary containment for liquid cleaning agents to prevent spills.
Physical safety features minimize injury risk during maintenance activities. These include anti-slip flooring or mats in work areas, adequate space to prevent awkward positioning during repairs, appropriate lighting to reduce eye strain, and ergonomic work heights to prevent back injuries. Tool storage should prevent sharp edges from causing injuries during retrieval.
Comprehensive training ensures all personnel understand and implement safety protocols. This includes proper lifting techniques, electrical safety basics, chemical handling procedures, and equipment-specific safety considerations. Regular refresher training maintains awareness as procedures evolve or new equipment enters service. Documentation of training completion creates accountability and demonstrates due diligence.
Enhancing Efficiency Through Standard Operating Procedures
Standardized procedures transform individual knowledge into organizational systems that ensure consistency regardless of who performs the maintenance.
Comprehensive documentation forms the foundation of effective procedures. This includes step-by-step guides for common maintenance tasks, troubleshooting flowcharts for identifying problems, parts diagrams for assembly reference, and model-specific maintenance requirements. Digital formats allow for easy updating and may include video demonstrations of complex procedures for clarity.
Usable procedure design ensures documentation actually gets used rather than ignored. Consider laminated quick-reference guides posted at workstations for frequent tasks. Use clear, jargon-free language accessible to all education levels. Incorporate visual elements like photographs or diagrams to clarify written instructions. Break complex procedures into clearly numbered steps to prevent skipping critical elements.
Training integration connects procedures with practical application. New personnel should receive structured orientation to maintenance procedures before performing tasks independently. Skill verification ensures competency in critical maintenance activities. Consider implementing a mentoring system where experienced staff guide new technicians through procedures until proficiency is demonstrated.
Continuous improvement mechanisms refine procedures over time. Encourage feedback from technicians about procedural gaps or inefficiencies. Regular review sessions identify opportunities for streamlining or enhancing documentation. Update procedures whenever equipment changes or new best practices emerge. This ongoing refinement ensures procedures remain relevant and valuable.
Budget-Friendly Vacuum Station Implementation
Creating an effective vacuum care station need not require substantial financial investment. Strategic approaches can maximize value while minimizing costs.
Phased implementation spreads expenses over time while allowing for system refinement. Begin with core elements like basic storage and essential tools, then expand to more sophisticated components as budget allows. This approach enables immediate improvement while planning for future enhancements. Each phase should function effectively on its own while preparing for subsequent additions.
Cost-effective storage solutions leverage existing resources where possible. Repurposed shelving or cabinets can provide adequate storage without new purchases. Standard plastic bins with custom labels offer affordable organization. Consider utilizing vertical wall space with pegboard systems or wall-mounted organizers to maximize capacity without additional floor space requirements.
DIY organization options substitute craftsmanship for purchased solutions. Custom-built workbenches may cost significantly less than commercial alternatives while offering tailored dimensions. PVC pipe sections create excellent holders for vacuum wands and attachments. Repurposed kitchen drawer organizers effectively sort small parts and tools for a fraction of specialized storage costs.
Resource prioritization focuses limited budgets on high-impact elements. Invest first in quality storage for the vacuums themselves to prevent damage to these expensive assets. Basic tool sets and essential replacement parts represent the next priority for functional maintenance. Aesthetic elements and convenience features can follow as resources permit. This strategic allocation ensures functional capability even with limited resources.
Professional-Grade Vacuum Care Stations
Organizations with substantial vacuum fleets or specialized equipment may benefit from advanced care station designs that support comprehensive maintenance operations.
Commercial-level equipment considerations address the unique needs of industrial vacuum systems. These may include heavy-duty lifting systems for large units, specialized diagnostic equipment for motor assessment, custom fabrication capabilities for uncommon parts, or advanced cleaning systems for thoroughly sanitizing components. The investment in these specialized systems typically pays dividends through extended equipment life and reduced replacement costs.
Advanced diagnostics areas enable thorough performance evaluation. These might include airflow measurement equipment, electrical testing capabilities, noise level assessment tools, or specialized fixtures for isolating component performance. Proper documentation systems capture test results for trend analysis and maintenance planning. Consider integrating digital diagnostic tools with maintenance record systems for comprehensive performance tracking.
Multi-user accessibility features support maintenance activities by various personnel. These include clearly documented procedures visible at workstations, tool check-out systems that ensure availability, scheduling systems that prevent station overcrowding, and standardized organization that remains intuitive across shifts. Training programs ensure all users understand station protocols and maintenance standards regardless of when they typically work.
High-volume operation adaptations address the needs of facilities maintaining numerous vacuum units. These might include assembly-line arrangements for routine maintenance tasks, specialized storage systems for managing large parts inventories, batch processing approaches for efficiency, or dedicated personnel roles focused on specific maintenance aspects. The systematic approach transforms what could be an overwhelming workload into manageable processes.
Real-World Examples of Effective Vacuum Care Stations
Examining implemented solutions provides valuable insights into practical applications of these principles across different operational contexts.
Small business implementation: A cleaning service with 15 portable vacuums created an effective care station in a 6’×8′ dedicated area. Wall-mounted vacuum holders maximized floor space while keeping units accessible. A pegboard system organized attachments with photographic labels showing proper placement. A simple workbench with overhead lighting provided adequate space for maintenance activities. Plastic drawer organizers sorted replacement parts by vacuum model. This modest investment reduced equipment downtime by approximately 30% while extending average vacuum lifespan by nearly two years.
Large facility optimization: A convention center managing over 50 vacuum units implemented a comprehensive care station that transformed maintenance practices. The system included modular workstations that supported simultaneous maintenance of multiple units, barcode inventory tracking integrated with purchasing systems, and digital maintenance records accessible via tablet devices. Specialized training allowed certain staff to handle complex repairs while others managed routine maintenance. The structured approach reduced annual vacuum replacement costs by 45% while improving cleaning performance metrics.
Before and after transformations reveal the impact of thoughtful organization. One hospital maintenance department converted a cluttered closet with vacuums piled haphazardly into a systematic care center with designated spaces for each unit and component. The transformation reduced search time for accessories from an average of 12 minutes to less than 2 minutes. Staff reported significantly higher satisfaction with equipment reliability after implementation. Photographic documentation of the transition process provided valuable reference for maintaining the improved system.
Return on investment metrics demonstrate the financial justification for vacuum care stations. Analysis from multiple implementations shows typical payback periods of 4-12 months based on reduced replacement costs, decreased labor time spent searching for parts or tools, and extended equipment lifespan. Additional benefits include improved cleaning effectiveness, reduced emergency repair expenses, and enhanced staff satisfaction with equipment reliability. These tangible outcomes support continued investment in maintenance infrastructure.
Conclusion
A well-designed vacuum care station represents a strategic investment in operational efficiency and equipment longevity. By systematically organizing maintenance supplies, creating appropriate storage solutions, and implementing structured procedures, organizations transform haphazard equipment care into a streamlined system that delivers measurable benefits.
The principles outlined in this guide can be adapted to operations of any size – from small cleaning companies to large institutional facilities. The key lies not in the scale of implementation but in the systematic approach to vacuum maintenance. Even modest investments in organization can yield significant returns through extended equipment life, improved performance, and reduced maintenance time.
Begin by assessing your current vacuum maintenance practices to identify improvement opportunities. Start with manageable changes that address the most significant pain points, then build toward a comprehensive system over time. Document your results to demonstrate value and justify further enhancements. With thoughtful planning and consistent implementation, your vacuum care station will become an essential component of your maintenance operation’s success.