Extreme Temperature Environments: Vacuum Performance in Attics and Sunrooms
Attics and sunrooms face the most extreme temperature fluctuations in your home. Learn how vacuum insulation technology offers superior performance where traditional materials fail—and if it’s worth the investment.
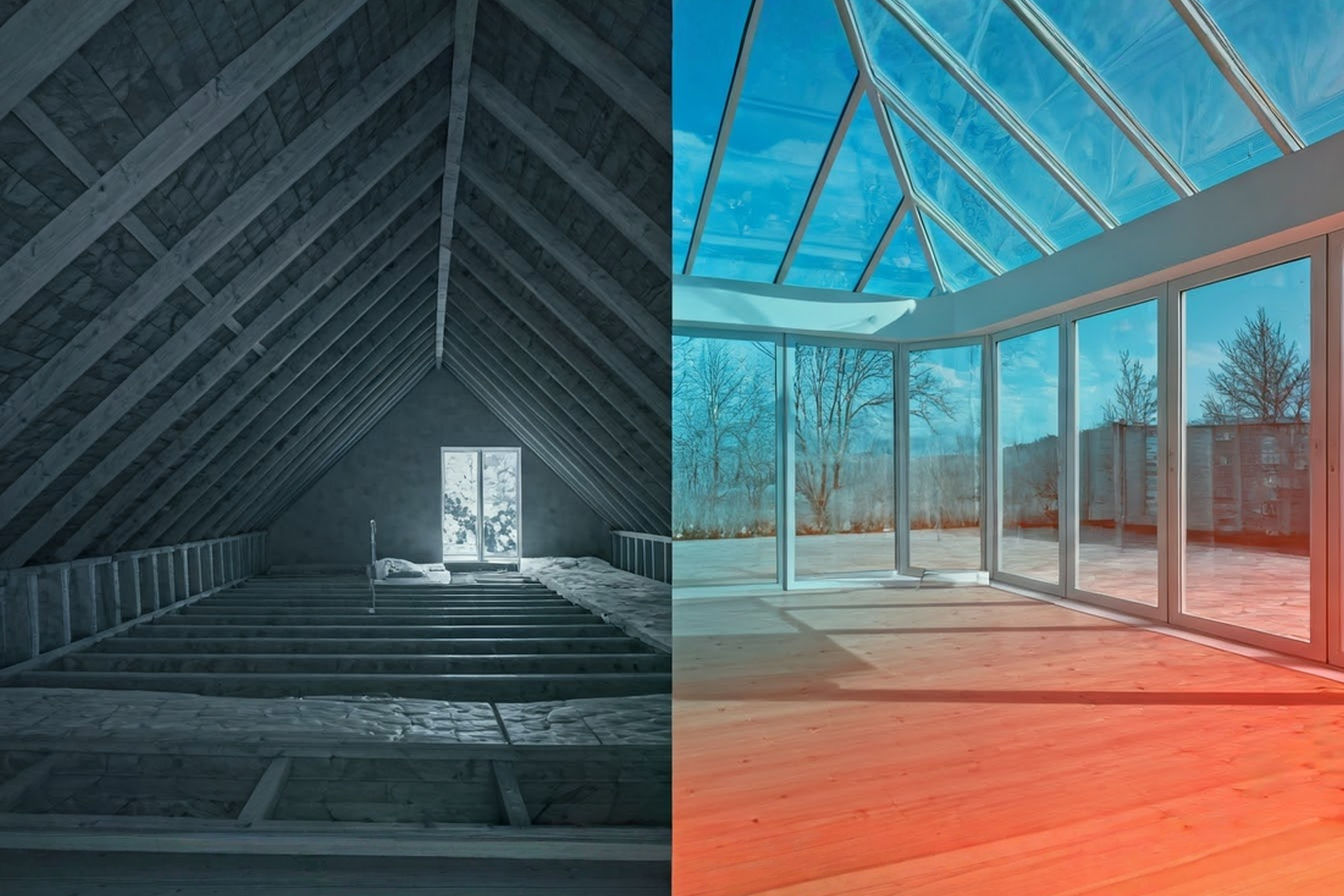
This post may contain affiliate links. If you make a purchase through these links, we may earn a commission at no additional cost to you.
Attics and sunrooms represent some of the most challenging thermal environments in residential buildings. These spaces routinely face temperature extremes that can make them uncomfortable, energy-inefficient, and potentially damaging to the overall structure. Attics can reach scorching temperatures exceeding 150°F (65°C) in summer while plummeting below freezing in winter. Sunrooms, with their extensive glazing, can experience similar extremes — transforming from tropical hothouses to frigid zones as seasons change.
Traditional insulation materials often struggle to maintain comfort in these demanding conditions. Enter vacuum insulation technology, an advanced solution that’s changing how we approach temperature regulation in these problematic spaces. This technology harnesses the same physical principles that keep your coffee hot in a thermos but scaled up for building applications.
In this comprehensive guide, we’ll explore how vacuum insulation performs in the extreme temperature environments of attics and sunrooms. We’ll examine the science behind this technology, analyze real-world performance metrics, discuss installation considerations, and provide a thorough cost-benefit analysis. Whether you’re a homeowner looking to improve your living space or a contractor seeking advanced solutions for clients, this article will equip you with the knowledge to make informed decisions about vacuum insulation applications.
Understanding Heat Transfer in Attics and Sunrooms
Before diving into vacuum insulation solutions, it’s essential to understand the fundamental heat transfer mechanisms that create temperature extremes in attics and sunrooms.
The Three Heat Transfer Mechanisms
Conduction is the direct transfer of heat through solid materials. It’s why a metal spoon in hot soup quickly becomes too hot to hold. In buildings, conduction allows heat to pass through walls, roofs, and floors — moving from warmer areas to cooler ones. Traditional insulation works primarily by slowing conductive heat transfer.
Convection involves heat movement through liquids or gases. In homes, this occurs when warm air rises and cool air falls, creating circulation patterns that can either help or hinder comfort. In poorly insulated spaces, convection can create drafts and temperature stratification, where hot air collects near the ceiling while the floor remains cold.
Radiation transfers heat via electromagnetic waves without needing a physical medium. The sun warms the earth through radiation, and similarly, your roof absorbs solar radiation during daylight hours. Radiant heat can pass through air and vacuum with minimal loss, making it particularly challenging to control in sunrooms with large glass areas.
Why Attics and Sunrooms Face Temperature Extremes
Attics typically experience extreme temperatures due to their position directly under the roof. In summer, roof surfaces can reach temperatures of 150-175°F (65-80°C) when exposed to direct sunlight. This heat radiates into the attic space, which often has minimal air exchange with the rest of the house. Without adequate insulation, this heat can then conduct through the ceiling into living spaces below.
A typical attic in a moderate climate might experience temperature swings from 25°F (-4°C) in winter to 150°F (65°C) in summer — a 125-degree range that puts enormous stress on building materials and insulation systems.
Sunrooms present a different but equally challenging thermal environment. Their large glass surfaces allow solar radiation to enter freely, creating a greenhouse effect where heat becomes trapped inside. A sunroom with standard double-pane windows can easily reach 120°F (49°C) on a sunny 85°F (29°C) day. Conversely, these same glass surfaces lose heat rapidly in cold weather, with interior surface temperatures often dropping below comfort levels even when heating systems are running.
These extreme conditions require insulation solutions that address all three heat transfer mechanisms effectively — a tall order for conventional materials.
The Science Behind Vacuum Insulation
Vacuum insulation represents a significant advancement over traditional insulation materials, offering exceptional thermal performance through fundamental physics principles.
Basic Principles of Vacuum Insulation
At its core, vacuum insulation technology employs one simple fact: heat cannot transfer through a vacuum by conduction or convection because both require a physical medium. By removing air from a space, two major heat transfer pathways are effectively eliminated.
Vacuum insulated panels (VIPs) consist of three primary components:
- A rigid core material with an open porous structure
- A high-barrier envelope film
- A vacuum between 0.01 and 1 mbar (nearly complete vacuum)
How it works: The core material provides structural support while the vacuum eliminates conductive and convective heat transfer. The barrier film maintains the vacuum and helps control radiative heat transfer. This combination creates an insulation product with R-values of R-25 to R-50 per inch (compared to R-3 to R-7 per inch for conventional insulation materials).
Historical Development of Vacuum Insulation
Vacuum insulation isn’t new — the first commercial application appeared in refrigeration technology during the 1930s. However, building applications remained limited until the 1990s when manufacturing advances made vacuum insulated panels more durable and affordable.
The technology benefited greatly from aerospace research, where NASA needed ultra-efficient insulation for spacecraft that would face temperature extremes from -250°F to +250°F (-157°C to +121°C). These demanding requirements led to innovations in core materials and barrier films that eventually made their way into residential construction applications.
Core Materials and Barrier Films
The core material in a VIP serves multiple critical functions. It must:
- Maintain its structure under atmospheric pressure
- Create a network of tiny voids for vacuum creation
- Minimize radiative heat transfer
- Resist compression over time
Common core materials include:
- Fumed silica: The most widely used core material, offering excellent thermal properties and pressure resistance
- Fiberglass: Provides good structural support but higher thermal conductivity
- Aerogel: Offers exceptional insulation value but at higher cost
- Precipitated silica: Similar to fumed silica but with different manufacturing process
- Polyurethane foam: Used in some applications despite higher thermal conductivity
The barrier film is equally important, as it must maintain the vacuum for the panel’s entire service life. Modern VIPs use multi-layer films that typically include:
- Metallized polymer layers to block gas permeation
- Structural polymer layers for durability
- Aluminum foil layers as moisture and oxygen barriers
- Protective outer layers for handling and installation
Even the best barrier films allow some gas permeation over time, which is why vacuum insulation manufacturers often specify performance metrics at 25-year values rather than initial values.
R-Value Comparisons
The thermal resistance (R-value) of insulation materials directly correlates to their effectiveness. Vacuum insulation dramatically outperforms traditional options:
Insulation Type | R-Value per inch | Thickness needed for R-19 |
---|---|---|
Vacuum Insulated Panel | R-25 to R-50 | 0.4-0.75 inches |
Polyurethane Spray Foam | R-6 to R-7 | 2.7-3.2 inches |
Fiberglass Batt | R-3.1 to R-3.7 | 5.1-6.1 inches |
Cellulose (Blown) | R-3.2 to R-3.8 | 5.0-5.9 inches |
XPS Foam Board | R-5 | 3.8 inches |
This exceptional performance comes from the near-elimination of conductive and convective heat transfer. While traditional insulation primarily slows these mechanisms, vacuum insulation almost completely blocks them. The remaining heat transfer occurs through radiation and thermal bridging at panel edges.
Vacuum Insulation Performance in Attic Spaces
Attics present unique challenges and opportunities for vacuum insulation applications. Their extreme temperature variations, limited access, and critical role in whole-house energy performance make them important test cases for vacuum technology.
Temperature Conditions in Attics
Attic spaces routinely experience the most extreme temperature fluctuations in residential buildings. During summer months, roof surface temperatures can exceed 175°F (80°C) under direct sunlight. This heat radiates and conducts into the attic space, where temperatures of 140-150°F (60-65°C) are common in poorly insulated homes.
These high temperatures create multiple problems:
- Heat transfer to living spaces below
- Increased cooling costs (up to 30% of total cooling load)
- Degradation of roofing materials from the inside
- Potential damage to items stored in attic spaces
- Stress on HVAC equipment located in attics
Winter conditions present the opposite problem, with attic temperatures dropping below freezing in many climate zones. This creates risks of frozen pipes and significant heat loss from living spaces.
Vacuum Insulation Applications for Attics
Vacuum insulated panels offer several advantages for attic applications:
Reduced thickness means more usable space in attics with limited clearance. A 1-inch (25mm) VIP can replace 6 inches (150mm) of fiberglass with equal or better performance.
Weight reduction is critical for older homes where adding conventional insulation might overload ceiling joists. VIPs weigh approximately 4-7 pounds per square foot at R-30, compared to 8-12 pounds for equivalent fiberglass with required depth.
Moisture resistance helps prevent condensation issues common in attics. The impermeable barrier films used in VIPs block moisture migration that can degrade thermal performance in traditional insulation.
Installation Methods for Attics
Installing vacuum insulation in attics requires careful planning and execution due to the panels’ vulnerability to puncture. Common approaches include:
Direct application to attic floor works well in unfinished attics where VIPs can be placed between joists and covered with a protective layer. This approach maximizes energy saving potential but limits future attic access.
Roof deck application places VIPs directly under roof sheathing, creating a “hot roof” design that brings the attic within the building’s conditioned envelope. This strategy works particularly well when HVAC equipment is located in the attic space.
Hybrid systems combine VIPs with conventional insulation to maximize performance while managing costs. A common approach uses a base layer of VIPs (R-30) covered by blown cellulose (R-10) for protection and additional thermal resistance.
Managing Thermal Bridges
Thermal bridging occurs where insulation is interrupted by structural elements like joists or rafters. These bridges can reduce overall insulation effectiveness by 15-30% in conventional systems.
Vacuum insulation systems address thermal bridging through several strategies:
Staggered panel placement ensures that VIP seams don’t align with structural elements, creating a more consistent thermal barrier.
Edge treatment with specialized tape or foam strips helps minimize heat transfer at panel junctions.
Thermal break materials installed between structural elements and VIPs further reduce heat flow through wood or metal components.
In field tests, properly installed VIP systems in attics have demonstrated 98% of their rated R-value performance, compared to 70-85% for conventional insulation systems where thermal bridging effects are more pronounced.
Moisture Considerations
Moisture management is critical in attic insulation systems. Vacuum insulated panels offer significant advantages here because:
- Their impermeable barrier films prevent moisture absorption that plagues fibrous insulation
- They maintain constant R-value regardless of humidity conditions
- They eliminate the risk of mold growth within the insulation material
However, proper installation must address potential condensation at panel seams and edges. Most professional installations include:
- Vapor barriers on the warm side of the insulation assembly
- Careful sealing at all penetrations
- Strategic ventilation design to remove any moisture that does enter
Vacuum Insulation Solutions for Sunrooms
Sunrooms present perhaps the most challenging thermal environment in residential construction. Their large glazed areas create extreme temperature fluctuations that standard insulation struggles to address. Vacuum insulation technology offers promising solutions for these spaces.
Unique Temperature Challenges in Glass-Enclosed Spaces
Sunrooms face a fundamental thermal contradiction: they’re designed to let light in while keeping temperature extremes out. This creates several challenges:
Solar heat gain can cause temperatures to rise 30-40°F (17-22°C) above outdoor temperatures on sunny days, even in winter. This occurs because glass readily transmits shortwave radiation from the sun but blocks the longwave radiation that would normally allow heat to escape.
Rapid heat loss occurs through the same glass surfaces at night and during cloudy weather. A typical sunroom with standard double glazing can lose heat up to 10 times faster than an insulated wall of the same area.
Temperature stratification creates uncomfortable conditions where the ceiling area may be 20°F (11°C) warmer than the floor. This occurs because heated air rises while cool air from glass surfaces falls, creating constant convection currents.
Seasonal extremes mean that many sunrooms are effectively unusable during peak summer and winter months without massive energy inputs for heating and cooling.
Solar Heat Gain Management with Vacuum Technology
Vacuum insulation can be strategically deployed in sunroom floor, wall, and ceiling elements to counterbalance the thermal challenges of glass:
Floor applications are particularly effective. By installing VIPs under flooring, radiant floor heating systems become dramatically more efficient, reflecting heat upward rather than losing it to the ground. This helps counter the cold air that naturally collects at floor level in sunrooms.
Ceiling applications help prevent overheating by reducing heat transfer from the roof. In side-by-side tests, sunrooms with VIP ceiling insulation maintained temperatures 12-18°F (7-10°C) cooler during summer months compared to conventional insulation of twice the thickness.
Wall elements between glass panels can incorporate thin VIPs without sacrificing the open, airy aesthetic that makes sunrooms attractive. A 0.5-inch (12mm) VIP provides insulation equivalent to a 3-inch (75mm) thick wall with conventional materials.
Condensation Management
Condensation is a persistent problem in sunrooms due to the temperature differential between glass surfaces and interior air. When warm, humid interior air contacts cold glass surfaces, water droplets form, potentially causing damage to frames, sills, and flooring.
Vacuum insulation helps manage condensation through several mechanisms:
- Temperature stabilization keeps interior surfaces closer to ambient room temperature, reducing the likelihood of reaching dew point
- Strategic placement around window frames and edges prevents thermal bridges where condensation typically forms first
- Integration with ventilation systems allows for maintaining lower humidity levels without sacrificing comfort
Field studies show that properly designed sunrooms using vacuum insulation can maintain relative humidity levels 15-20% lower than conventionally insulated spaces without additional dehumidification equipment.
Year-Round Comfort Strategies
Creating comfortable sunroom environments throughout the year requires a systems approach that considers:
Seasonal sun angles determine where solar heat gain will occur. Vacuum insulation can be strategically placed to complement seasonal needs—reflecting heat in summer while retaining it in winter.
Thermal mass integration works synergistically with VIPs. Materials like concrete, stone, or phase-change materials can store thermal energy when coupled with the exceptional insulation properties of vacuum panels.
Ventilation design must account for the reduced air infiltration in well-insulated spaces. Mechanical ventilation with heat recovery can maintain air quality without sacrificing thermal performance.
A well-designed sunroom using vacuum insulation technology can achieve year-round comfort while reducing energy usage by 40-60% compared to conventionally insulated spaces of similar design.
Performance Metrics and Testing
Understanding how vacuum insulation performs in real-world conditions requires rigorous testing methodologies and standardized performance metrics.
R-value Measurements in Extreme Temperatures
Unlike conventional insulation, vacuum insulated panels maintain nearly constant R-values across a wide temperature range. Testing protocols like ASTM C518 (Standard Test Method for Steady-State Thermal Transmission Properties) have been adapted for VIPs to account for their unique properties.
Test results show that VIP R-values typically vary less than 5% between -40°F and 200°F (-40°C and 93°C), compared to variations of 15-30% for conventional materials like fiberglass or foam. This stability is particularly valuable in attics and sunrooms where temperature extremes are common.
A typical 1-inch (25mm) VIP maintains an R-value between R-28 and R-30 across this entire temperature range, while 1-inch polyurethane foam might range from R-5.1 at 200°F to R-7.2 at 0°F.
Accelerated Aging Tests
Because vacuum insulation performance depends on maintaining the vacuum, accelerated aging tests are crucial for predicting long-term performance. Industry standards include:
Temperature cycling tests expose panels to repeated temperature swings from -40°F to 180°F (-40°C to 82°C) to simulate decades of seasonal changes
Humidity exposure tests measure the impact of moisture on barrier films and edge seals
Pressure tests evaluate the core material’s resistance to compression under atmospheric pressure over time
Gas permeation measurements quantify the slow infiltration of air molecules through barrier films
Most quality VIPs are designed to maintain at least 80% of their initial R-value after 25 years of service, with annual performance degradation of 0.5-1.0%.
Thermal Imaging Assessments
Infrared thermal imaging provides valuable real-world performance data for vacuum insulation installations. These assessments reveal:
Thermal bridging at panel seams and structural elements Installation quality issues where panels may be damaged or improperly sealed Performance differences between VIPs and surrounding conventional insulation
Field studies using thermal imaging in attic applications show temperature differentials of just 2-3°F (1-1.7°C) across properly installed VIP surfaces, compared to 8-12°F (4.4-6.7°C) for conventional insulation of equivalent R-value rating.
Energy Efficiency Calculations
The energy impact of vacuum insulation can be calculated using several methodologies:
Whole-building energy modeling using software like EnergyPlus or TRNSYS predicts annual energy consumption Heat flux measurements using sensors placed on both sides of insulation assemblies quantify actual energy transfer Utility bill analysis before and after installation provides real-world validation
Case studies of residential attic retrofits with VIPs show average energy savings of:
- 22-28% reduction in total cooling costs
- 15-20% reduction in heating costs
- 3-5 year simple payback period in extreme climate zones
For sunrooms, the impact is even more dramatic, with many spaces becoming usable year-round without supplemental heating or cooling after VIP installation.
Installation Considerations and Best Practices
The exceptional performance of vacuum insulation can only be realized with proper installation techniques. The unique properties of VIPs create both challenges and opportunities during the installation process.
Professional vs. DIY Installation
While DIY installation is possible for some applications, professional installation is strongly recommended for vacuum insulated panels due to:
Puncture risk – Even small perforations will compromise the vacuum and dramatically reduce insulation value Panel sizing – VIPs cannot be cut on-site and must be pre-ordered to exact dimensions Edge treatment – Professional edge sealing techniques help minimize thermal bridging System design – Proper panel layout requires technical knowledge to maximize performance
Professional installation typically adds 15-30% to material costs but significantly reduces the risk of performance problems. Many manufacturers void warranties on self-installed panels due to the high risk of damage during installation.
Preparation Requirements
Proper surface preparation is essential for VIP installation:
Surface smoothness – The substrate must be free of sharp protrusions that could puncture panels Structural assessment – Existing structure must be evaluated to ensure it can support the installation Moisture mitigation – Any existing moisture issues must be resolved before installation Thermal mapping – Infrared scanning can identify problem areas that need special attention
For attic installations, thorough cleaning and removal of old insulation is typically recommended to provide a clean, smooth surface for VIP placement.
Working Around Obstacles and Penetrations
Attics and sunrooms often contain various penetrations for electrical, plumbing, and HVAC systems. Working around these obstacles requires:
Pre-manufactured cutouts – Many VIP manufacturers offer custom panels with precisely positioned openings for known penetrations Junction panels – Special panels designed to safely accommodate electrical boxes and similar penetrations Buffer zones – Areas around penetrations are often insulated with conventional materials to reduce puncture risk
For electrical penetrations, specially designed VIP installation boxes can maintain thermal performance while providing code-compliant electrical connections.
Edge Sealing and Thermal Bridge Mitigation
Panel edges represent the most vulnerable points in a vacuum insulation system:
Tape systems – Specialized aluminum tapes create continuous thermal and moisture barriers Overlap patterns – Strategic panel arrangement minimizes the impact of edge thermal bridges Foam gaskets – Compressible foam strips can seal irregular gaps between panels Thermal break materials – Low-conductivity materials placed at structural intersections reduce heat transfer
Field testing shows that proper edge treatment can improve overall system performance by 8-12% compared to basic installation methods.
Integration with Existing Systems
Few projects involve vacuum insulation exclusively. Most combine VIPs with conventional materials in a hybrid approach:
Protective coverings – VIPs are typically covered with a layer of conventional insulation or building material for mechanical protection Vapor barrier integration – Careful attention to vapor barrier continuity prevents moisture problems Ventilation modifications – Reduced heat transfer may require adjustments to existing ventilation systems Structural adaptations – The reduced thickness of VIP systems sometimes requires adjustment of framing elements
In attic applications, VIPs are commonly installed between joists with a covering layer of blown cellulose or fiberglass for protection and additional R-value.
Cost Analysis and Return on Investment
Vacuum insulation represents a premium insulation solution with higher initial costs but potentially significant long-term benefits. Understanding the complete financial picture is essential for making informed decisions.
Initial Investment Comparisons
Vacuum insulated panels currently carry a substantial price premium over conventional insulation:
Insulation Type | Approximate Cost per R-value per sq ft | Cost for R-30 (10’×10′ area) |
---|---|---|
Vacuum Insulated Panels | $0.40-$0.60 per R per sq ft | $1,200-$1,800 |
Spray Foam (Closed Cell) | $0.17-$0.25 per R per sq ft | $510-$750 |
Fiberglass Batts | $0.03-$0.05 per R per sq ft | $90-$150 |
Cellulose (Blown) | $0.03-$0.06 per R per sq ft | $90-$180 |
This significant cost difference is partially offset by several factors:
Space savings – The thin profile of VIPs can free up valuable space, particularly in renovations Installation efficiency – Less material handling and faster installation can reduce labor costs Structural benefits – Lighter weight may eliminate the need for structural reinforcement Ancillary savings – Reduced HVAC equipment sizing due to lower heating/cooling loads
For sunrooms specifically, VIPs can transform seasonally used spaces into year-round living areas, significantly increasing usable square footage without new construction.
Energy Savings Calculations
Energy savings from vacuum insulation vary by climate zone, existing insulation levels, and specific application. Average figures from field studies show:
Attic applications in cooling-dominated climates:
- 0.5-0.8 kWh/sq ft/year electricity savings
- $0.06-$0.10 per sq ft annual utility cost reduction (at $0.12/kWh)
Attic applications in heating-dominated climates:
- 0.4-0.6 therms/sq ft/year natural gas savings
- $0.40-$0.70 per sq ft annual utility cost reduction (at $1.10/therm)
Sunroom applications:
- 30-50% reduction in supplemental heating/cooling energy
- Potential elimination of dedicated HVAC equipment in moderate climates
These figures translate to annual savings of $120-$300 for a typical attic installation (1,000 sq ft) and $200-$500 for a sunroom application (200 sq ft), depending on local energy costs and climate severity.
Lifespan and Durability Factors
The service life of insulation significantly impacts return on investment calculations:
Vacuum insulated panels typically maintain at least 80% of their R-value for 25-30 years when properly installed and protected Spray foam insulation generally performs well for 20-30 years but may deteriorate faster in extreme temperature environments Fiberglass and cellulose can lose 20-40% of their effective R-value within 10-15 years due to settling, moisture absorption, and air infiltration
This durability advantage means that while VIPs might cost 8-10 times more initially, their lifetime cost per R-value-year can be just 3-4 times higher than conventional options when considering performance degradation.
Payback Period Estimates
Simple payback periods for vacuum insulation vary considerably based on application and climate:
Attic installations in extreme climates (IECC Climate Zones 1-2 and 7-8):
- 8-12 year simple payback period
- 10-15% internal rate of return
Attic installations in moderate climates (IECC Climate Zones 3-6):
- 12-18 year simple payback period
- 6-9% internal rate of return
Sunroom applications across all climate zones:
- 5-10 year simple payback period when considering extended seasonal use
- 15-25% internal rate of return when calculating based on additional usable square footage
When factoring in potential property value increases, particularly for sunroom improvements that expand year-round living space, the financial case becomes considerably stronger.
Limitations and Considerations
Despite their impressive performance, vacuum insulated panels have several limitations that must be considered when planning installations in extreme temperature environments.
Size Restrictions and Panel Dimensions
Manufacturing constraints limit individual panel sizes:
Maximum dimensions typically range from 4’×8′ to 5’×10′ (1.2m×2.4m to 1.5m×3m) Minimum dimensions are usually around 12″×12″ (30cm×30cm) Thickness options generally range from 0.25″ to 2″ (6mm to 50mm)
These size limitations mean that installations require careful planning to:
- Minimize the number of panel joints
- Accommodate irregular spaces
- Work around structural elements
Custom-sized panels are available from most manufacturers but typically carry a 20-30% price premium and may have 4-6 week lead times.
Puncture Vulnerability
The vacuum that gives VIPs their exceptional performance also creates their greatest weakness:
Puncture resistance varies by manufacturer but even the most durable panels can be compromised by sharp objects, power tools, or fasteners Repair options are extremely limited once a panel is punctured – typically requiring complete replacement Risk mitigation usually involves protective coverings and clear marking of panel locations to prevent future damage
This vulnerability makes VIPs problematic for spaces where future modifications are likely or where occupants might inadvertently damage them.
Thermal Bridging Concerns
Despite their high center-of-panel R-values, overall system performance can be compromised by thermal bridges:
Edge effects reduce effective R-value by 5-15% depending on panel size (smaller panels have proportionally more edge area) Structural elements like rafters and studs create unavoidable thermal bridges Panel joints create small but significant paths for heat transfer
Manufacturers’ stated R-values typically represent center-of-panel performance rather than installed system performance. Real-world installations may achieve 85-95% of rated R-value when properly executed.
Aging and Performance Degradation
All vacuum insulation experiences some performance loss over time:
Gas permeation through barrier films gradually reduces vacuum quality Core compression can occur over decades of pressure differential Edge seal degradation may allow faster gas infiltration
Quality VIPs typically lose 0.5-1.0% of their R-value annually. This means a panel rated at R-30 initially might provide R-25.5 to R-27 after 10 years and R-21 to R-24 after 20 years.
Some manufacturers address this by initially evacuating panels beyond what’s needed for stated R-values, providing a “performance reserve” that maintains rated values longer.
Compatibility with Other Building Elements
Integration challenges exist when combining VIPs with other building systems:
Fastening limitations – Panels cannot be penetrated for mounting fixtures or finishes Fire rating questions – Some barrier films and core materials may affect fire performance Sound transmission – The rigid nature of VIPs can create acoustical bridges Electrical considerations – Special provisions are needed for electrical boxes and wiring
These integration issues require thoughtful design and often specialized components to maintain both thermal performance and compliance with building codes.
Building Code Compliance
The relatively recent introduction of vacuum insulation to residential construction has created some code compliance challenges:
Testing standards developed for conventional insulation don’t always apply directly to VIPs Fire rating requirements may necessitate additional protective layers Installation documentation often requires more detail than conventional systems Inspector familiarity varies widely, potentially leading to approval delays
Most manufacturers provide technical documentation specifically addressing building code requirements, and many offer consulting services to help navigate the approval process.
Future Developments in Vacuum Insulation Technology
As vacuum insulation technology continues to evolve, several promising developments are poised to address current limitations and expand applications for extreme temperature environments.
Emerging Manufacturing Techniques
Advancements in manufacturing processes are steadily reducing costs while improving performance:
Roll-to-roll production methods are replacing batch processing, potentially reducing manufacturing costs by 30-40% within the next five years. This continuous production approach allows for longer, more consistent panels with fewer edge effects.
Automated quality control systems using ultrasonic testing and thermal imaging can detect microscopic flaws before panels leave the factory. This improved quality assurance is reducing failure rates from 3-5% to under 1%, making VIPs more reliable for critical applications.
3D-printed core structures are beginning to replace traditional fumed silica cores in some applications. These engineered structures optimize support while minimizing thermal bridging within the panel itself, potentially increasing R-values by 10-15% per inch.
Advancements in Barrier Films
Barrier film technology is perhaps the most active area of vacuum insulation research:
Multi-layer nano-coatings are reducing gas permeation rates by up to 80% compared to current metallized films. These advanced barriers can extend useful life from 25 years to 40+ years before significant performance degradation occurs.
Transparent vacuum barriers are in development, which would revolutionize sunroom applications by allowing vacuum insulation within glazing systems themselves. Prototypes have achieved R-10 in a 1/2-inch panel while maintaining 70% visible light transmission.
Flexible barrier systems that can withstand moderate bending without compromising vacuum integrity are expanding potential applications. These materials can conform to curved surfaces while maintaining 85-90% of flat panel performance.
Self-Healing Vacuum Insulation Research
Perhaps the most exciting development addresses the Achilles’ heel of vacuum insulation—puncture vulnerability:
Chemical getter systems actively absorb gases that enter through micro-punctures, maintaining vacuum quality despite minor damage. Current systems can compensate for punctures up to 0.5mm in diameter.
Encapsulated vacuum regeneration technologies use embedded materials that can release additional vacuum-creating compounds when triggered by pressure changes, effectively “re-evacuating” panels that have experienced partial pressure loss.
Self-sealing layers incorporating materials similar to those used in puncture-resistant tires can instantly seal small penetrations before significant vacuum loss occurs.
Laboratory prototypes incorporating these technologies have maintained 95% of their original R-value after punctures that would render conventional VIPs completely ineffective.
Integration with Smart Home Technology
Vacuum insulation is increasingly being integrated with digital monitoring and control systems:
Embedded sensors can monitor vacuum pressure and thermal performance in real-time, alerting homeowners to panels that need replacement before energy costs increase significantly.
Adaptive systems combine vacuum insulation with phase-change materials and controllable heat transfer mechanisms to actively manage temperature swings in attics and sunrooms.
Predictive energy management uses weather forecasts and historical performance data to optimize heating and cooling strategies in spaces with vacuum insulation, further maximizing energy savings.
These smart integrations are particularly valuable in sunroom applications, where they can automatically adjust shading, ventilation, and supplemental heating/cooling based on insulation performance and environmental conditions.
Sustainability Improvements and Recyclability
Environmental concerns are driving significant research into more sustainable vacuum insulation:
Bio-based core materials derived from agricultural waste products are replacing petroleum-based components in some VIP formulations. These materials offer similar performance with 40-60% lower embodied carbon.
End-of-life recycling processes can now recover up to 90% of materials from used vacuum panels. New mechanical separation techniques make it economically viable to reclaim both barrier films and core materials.
Reduced manufacturing energy requirements through process optimization have cut the carbon footprint of VIP production by approximately 35% over the past decade.
These sustainability improvements are helping vacuum insulation meet increasingly stringent green building standards and improve lifecycle assessment metrics.
Conclusion
Vacuum insulation technology represents a significant advancement in addressing the extreme temperature challenges found in attics and sunrooms. Its exceptional thermal performance—typically 5-10 times better than conventional materials per inch of thickness—offers compelling benefits despite higher initial costs.
For attic applications, VIPs provide dramatic energy savings while maintaining their performance across the wide temperature ranges commonly experienced in these spaces. The thin profile preserves valuable headroom while the moisture resistance prevents condensation issues that plague many conventional insulation systems. When properly installed with attention to thermal bridging and edge sealing, vacuum insulation can transform problematic attics into well-regulated spaces that contribute to whole-house energy efficiency.
In sunrooms, vacuum insulation’s ability to maintain comfort despite large glazed areas extends usable seasons and often eliminates the need for separate heating and cooling systems. By strategically incorporating VIPs into floors, non-glazed walls, and ceiling elements, these traditionally challenging spaces can become comfortable year-round environments without excessive energy inputs.
While the initial investment in vacuum insulation significantly exceeds conventional alternatives, the long-term benefits often justify the cost—particularly in extreme climate zones or when space constraints limit insulation thickness. As manufacturing advances continue to reduce costs and address current limitations, vacuum insulation technology is positioned to become increasingly mainstream in residential construction and renovation projects.
Key Implementation Recommendations
When considering vacuum insulation for attics or sunrooms, several best practices emerge:
- Engage specialized professionals for design and installation to maximize performance and minimize risk of panel damage
- Develop a comprehensive thermal envelope strategy that addresses all heat transfer mechanisms, not just conduction
- Document panel locations precisely to prevent future damage during renovations or maintenance
- Consider hybrid approaches that use VIPs for primary insulation with conventional materials for protection and secondary insulation
- Evaluate lifetime costs and benefits rather than focusing solely on initial investment
With proper planning, design, and installation, vacuum insulation technology can transform the most thermally challenging spaces in residential buildings into comfortable, energy-efficient environments regardless of outdoor temperature extremes.
Additional Resources
Industry Standards and Specifications
- ASTM C1484: Standard Specification for Vacuum Insulation Panels
- ISO 16478: Thermal insulation products for buildings — Vacuum insulation panels (VIP)
- ASTM C1363: Standard Test Method for Thermal Performance of Building Materials
- Building America Solution Center: Vacuum Insulated Panel Installation Guidelines
Manufacturer Information
Leading vacuum insulation panel manufacturers providing residential solutions include:
- Kevothermal (USA)
- Va-Q-tec (Germany)
- Panasonic (Japan)
- ThermoCor (USA)
- Kingspan OPTIM-R (Ireland)
Most manufacturers offer detailed technical specifications, installation guides, and project consultation services.
Professional Installation Services
Vacuum insulation installation is increasingly available through:
- Certified insulation contractors with VIP-specific training
- Energy retrofit specialists focusing on high-performance building envelopes
- Sunroom manufacturers offering integrated VIP options in their designs
Look for contractors with manufacturer certification and documented experience with vacuum insulation products.
Energy Efficiency Programs and Incentives
Financial assistance for vacuum insulation projects may be available through:
- Utility company rebate programs for high-performance insulation
- Energy efficiency tax credits at federal, state, and local levels
- Green building certification programs that recognize exceptional thermal performance
- Home energy upgrade financing programs with favorable terms for energy-saving improvements
Contact local utility providers and building departments to identify available incentives in your area.