Advanced Materials Pipeline: Upcoming Compounds Poised to Transform Vacuum Cleaner Durability
Advanced materials are set to revolutionize vacuum cleaners, extending lifespans by 300%+ while improving performance. What compounds will transform the appliances you rely on daily?
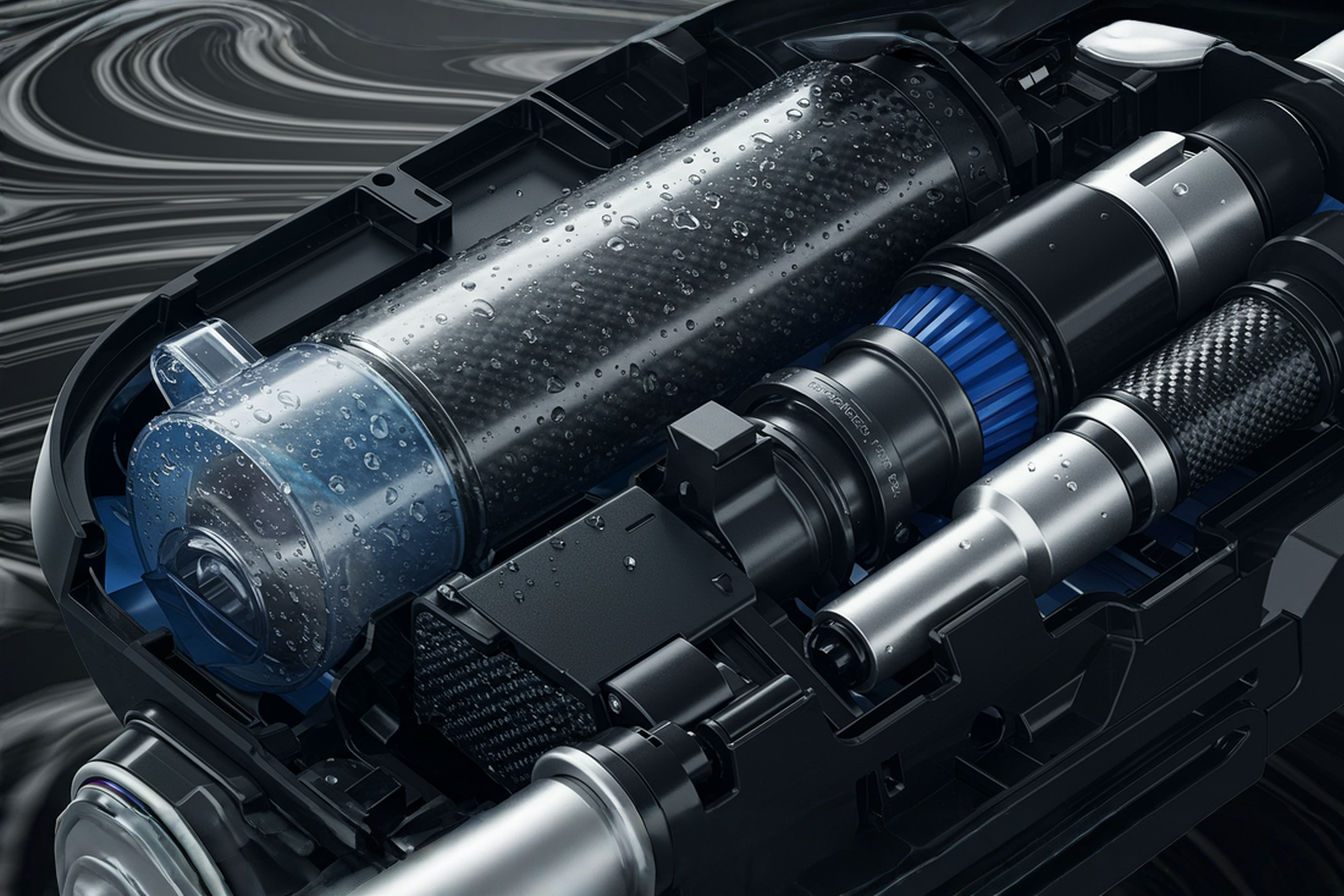
This post may contain affiliate links. If you make a purchase through these links, we may earn a commission at no additional cost to you.
The humble vacuum cleaner has come a long way since its invention in the early 1900s. What began as a bulky, inefficient machine has evolved into a sophisticated household appliance that combines advanced engineering with cutting-edge materials. Despite these improvements, durability remains a persistent challenge for vacuum manufacturers. The constant stress from motors, the abrasive nature of dust and debris, and the physical wear from regular use all take their toll on even the most well-designed units.
Today, we stand at the cusp of a material revolution that promises to transform vacuum cleaner durability forever. Advanced compounds and innovative materials are emerging from research labs and entering production pipelines, offering solutions to longstanding problems that have plagued vacuum cleaners for decades. These materials aren’t just incremental improvements—they represent fundamental shifts in how we approach appliance design and longevity.
In this comprehensive guide, we’ll explore the exciting world of advanced materials poised to reshape the vacuum cleaner industry. From self-healing polymers to graphene-enhanced components, these innovations will not only extend the lifespan of future vacuum cleaners but also improve their performance, sustainability, and value to consumers.
Current State of Vacuum Cleaner Materials
Before diving into tomorrow’s innovations, it’s essential to understand today’s baseline. Modern vacuum cleaners typically rely on a familiar set of materials that balance cost, performance, and manufacturing practicality.
Standard Materials in Modern Vacuum Cleaners
The average vacuum cleaner body is predominantly constructed from acrylonitrile butadiene styrene (ABS) and similar thermoplastics. These materials offer a reasonable balance of impact resistance, heat tolerance, and cost-effectiveness. Internal components often feature a mix of:
- Polycarbonate for transparent elements
- Various grades of steel for motors and structural support
- Aluminum for lightweight strength in premium models
- Rubber and silicone for gaskets, belts, and seals
- Nylon and polyester for brushes and filters
While functional, these conventional materials face significant limitations in demanding vacuum environments.
Limitations and Durability Issues
The current material palette leads to several common failure points that frustrate consumers and limit product lifespans:
- Plastic housing cracks from repeated impacts during normal use
- Motor burnout due to inadequate heat dissipation
- Brush roll wear from friction with floor surfaces
- Filter degradation after repeated cleaning cycles
- Hose and tube abrasion from debris passage
- Seal deterioration leading to suction loss
- Electrical component failure from heat and dust exposure
These issues aren’t just inconveniences—they directly impact performance, energy efficiency, and ultimately lead to premature replacement. A 2023 market study found that 62% of vacuum replacements occur due to material failures rather than functional obsolescence, highlighting the substantial opportunity for material innovation in this space.
Driving Forces Behind Advanced Materials Development
Several powerful forces are converging to accelerate the development of advanced vacuum cleaner materials:
Consumer Demands for Longer-Lasting Appliances
Today’s consumers increasingly expect their purchases to last. A significant shift in consumer sentiment has occurred, with 76% of appliance buyers now ranking durability as their top purchase consideration, according to recent market research. This represents a marked change from just a decade ago when features and price dominated purchase decisions.
This shift is partly driven by economic factors—consumers want more value for their money—but also by growing awareness of the environmental impact of disposable products. Many consumers now actively seek products with longer lifespans as part of their personal sustainability efforts.
Sustainability Requirements and Regulations
Environmental regulations are tightening worldwide, with particular focus on electronic waste, product lifespans, and recyclability. In Europe, the Right to Repair movement has gained substantial legislative support, requiring manufacturers to design for repairability and longevity.
These regulations create powerful incentives for manufacturers to invest in materials that extend product life, reduce waste, and comply with increasingly stringent environmental standards. Companies face potential fines, market access restrictions, and reputation damage if they fail to adapt.
Manufacturing Economics
While advanced materials often carry higher upfront costs, the economics increasingly favor durability innovations. Manufacturers are discovering that investment in better materials can:
- Reduce warranty claims and service costs
- Command premium pricing for more durable products
- Decrease returns and improve customer satisfaction
- Create opportunities for premium brand positioning
- Reduce exposure to volatile raw material pricing for conventional plastics
When factoring in these considerations, the business case for material innovation becomes much stronger, even with higher initial material costs.
Polymer Innovations: Beyond Traditional Plastics
The most visible and immediate advancements are occurring in polymer science, where traditional plastics are being reinvented with remarkable new properties.
High-Performance Thermoplastics
A new generation of engineered thermoplastics is entering the vacuum cleaner market, offering dramatic improvements over standard ABS and polycarbonate:
- Polyphenylene sulfide (PPS) provides exceptional heat resistance (up to 200°C/392°F) and chemical stability, making it ideal for components near motors or heating elements. Its dimensional stability under thermal stress prevents warping that can affect alignment of critical components.
- Polyetherimide (PEI) combines high strength with impressive impact resistance, creating housings that can withstand drops and collisions that would crack conventional plastics. PEI retains its properties across a wide temperature range, maintaining structural integrity in both hot motor environments and cold storage conditions.
- Liquid crystal polymers (LCPs) offer extraordinary flow properties during manufacturing, allowing for complex, thin-walled components with exceptional strength. This enables designers to create intricate internal structures without sacrificing durability.
These materials may cost 3-5 times more than standard plastics, but they can extend component lifespan by 300-500% in high-stress applications, dramatically improving the economics over the product lifecycle.
Self-Healing Polymer Technologies
Perhaps the most exciting development in polymer science is the emergence of self-healing materials that can repair minor damage autonomously. These remarkable compounds incorporate several different healing mechanisms:
- Microencapsulated healing agents that release when cracks form, flowing into damaged areas and hardening to restore structural integrity
- Reversible polymer networks that can reconnect broken chemical bonds when exposed to heat, light, or other stimuli
- Shape-memory polymers that return to their original configuration when triggered, closing cracks and restoring surface integrity
In practical terms, these materials can transform the vacuum cleaner experience. Minor cracks from impacts, scuffs from furniture collisions, and wear from repeated handling can all potentially self-repair, extending the aesthetic and functional lifespan of the appliance.
One startup has demonstrated a self-healing polymer housing that recovered from scratches within 12 hours at room temperature, with deeper damage healing when exposed to 60°C (140°F) heat for 30 minutes—achievable simply by running the vacuum in a warm environment.
Polymer Nanocomposites
The incorporation of nanoscale materials into polymer matrices is creating composites with exceptional properties:
- Clay nanoparticle reinforcement enhances barrier properties, preventing moisture and oxygen penetration that can damage internal components. These nanocomposites show 60% improvement in oxygen barrier properties compared to conventional polymers.
- Carbon nanotube (CNT) additives dramatically improve mechanical strength and electrical conductivity. Even at low concentrations (0.5-2%), CNTs can increase tensile strength by 30-40% while allowing static charges to dissipate safely.
- Graphene-enhanced polymers combine extraordinary strength with flexibility and thermal conductivity. At just 0.1% loading, graphene can improve thermal conductivity by 25%, helping dissipate heat from crucial components.
These nanocomposites aren’t just stronger—they’re fundamentally different materials with properties impossible to achieve in conventional plastics. For vacuum cleaner applications, this means housings that resist cracking while conducting heat away from motors, filters that capture more particles without impeding airflow, and components that maintain their properties over years of use.
Anti-Static and Dirt-Repelling Formulations
Static electricity is the enemy of clean operation in vacuum cleaners. It causes dust to cling to surfaces, reducing cleaning efficiency and contributing to component wear. New polymer formulations address this issue directly:
- Permanent anti-static additives create pathways for static dissipation without affecting the polymer’s mechanical properties. Unlike spray-on treatments that wear off, these additives are integrated into the polymer matrix, providing lasting protection.
- Hydrophobic and oleophobic surface treatments resist both water and oil-based contamination, preventing dust from adhering to surfaces. These treatments work at the molecular level, creating surfaces with micro- and nano-scale features that repel contaminants.
- Self-stratifying polymer blends automatically form layered structures during manufacturing, with specialized properties at the surface without compromising bulk material strength. This allows, for example, a dirt-repelling surface on a high-strength substrate without additional manufacturing steps.
A major European vacuum manufacturer has reported 43% less internal dust accumulation in prototypes using these advanced polymers, directly translating to reduced wear and extended component life.
Metal Alloy Advancements for Critical Components
While polymers dominate the visible parts of vacuum cleaners, metal components remain critical for structural integrity, motor functions, and high-wear applications. Here too, significant innovations are emerging.
Lightweight Aluminum Alloys
Traditional aluminum alloys are being reimagined with complex microstructures that dramatically improve strength-to-weight ratios:
- Scandium-modified aluminum alloys offer 20-30% higher strength than conventional aluminum while maintaining lightweight characteristics. These alloys resist fatigue failure from vibration, a common issue in vacuum motors.
- Aluminum-lithium alloys further reduce weight while improving stiffness, allowing for thinner, lighter components without sacrificing performance. Components made from these alloys can be up to 15% lighter than those made from traditional aluminum.
- High-entropy aluminum alloys incorporate multiple elements in near-equal proportions, creating unique microstructures with exceptional mechanical properties and corrosion resistance. These complex alloys can be tailored for specific performance requirements in vacuum applications.
These advanced alloys enable vacuum cleaners that are simultaneously lighter and more durable—a combination previously difficult to achieve with conventional materials.
Wear-Resistant Steel Variants
Steel remains essential for components facing extreme wear conditions, but traditional formulations often fail prematurely in vacuum applications. New steel variants address these limitations:
- Powder metallurgy high-speed steels incorporate finely dispersed hard particles throughout the material, creating exceptional wear resistance for brush roll bearings and other high-friction components. These materials can extend bearing life by 200-300% compared to conventional steel bearings.
- Nitrogen-enhanced stainless steels combine corrosion resistance with significantly improved surface hardness, ideal for components exposed to both moisture and abrasion. The nitrogen atoms create a super-hard surface layer without the flaking problems seen in coated steels.
- Amorphous metal alloys (metallic glasses) lack the crystalline structure of conventional metals, enabling extraordinary hardness and elastic properties. These materials can spring back from deformation that would permanently bend ordinary steel, making them ideal for components that must maintain precise dimensions under stress.
These specialized steels often replace parts that were once “disposable” wear items, transforming them into durable components that last the life of the appliance.
Advanced Metal Treatments and Coatings
Surface engineering technologies are transforming the performance of metal components without requiring entirely new materials:
- Plasma nitriding creates an extremely hard surface layer on steel components without dimensional changes, extending wear life by 300-500% in sliding applications like pivot points and hinges.
- Diamond-like carbon (DLC) coatings provide extraordinary hardness (approaching that of natural diamond) with low friction, dramatically reducing wear in moving components. These coatings are just 1-3 micrometers thick yet can increase component lifespan by 5-10 times.
- Ceramic composite coatings combine metal toughness with ceramic hardness, creating surfaces that resist both impact and abrasion. Applied through thermal spray processes, these coatings protect high-wear areas like fan impellers and air channels.
A leading vacuum manufacturer recently reported that replacing standard bearings with DLC-coated variants extended the testing lifetime of their commercial models from 1,000 hours to over 5,000 hours—a 400% improvement from a component that adds less than $2 to the bill of materials.
Ceramic and Composite Material Breakthroughs
Ceramics and composites are finding new applications in vacuum cleaners, offering property combinations impossible to achieve with single-material solutions.
Advanced Ceramics for High-Wear Components
Modern technical ceramics bear little resemblance to your coffee mug. These engineered materials offer exceptional wear resistance and thermal stability:
- Silicon nitride bearings provide extreme hardness with surprisingly good toughness, operating reliably in dusty environments where metal bearings would quickly fail. They can operate without lubrication, eliminating a common failure point.
- Zirconia-toughened alumina (ZTA) combines the hardness of aluminum oxide with the fracture resistance of zirconia, creating components that withstand both abrasion and impact. This material is finding applications in fan blades and separation chambers where debris impacts are frequent.
- Machinable glass ceramics offer precision tolerances with excellent electrical insulation properties, replacing plastic components near motors and heating elements where thermal degradation occurs. These materials maintain their dimensions and properties even after thousands of hours at elevated temperatures.
While more expensive than metals or plastics, these ceramics often prove economical when factoring in the extended lifespan they provide for critical components.
Carbon Fiber Composites in Vacuum Design
Carbon fiber reinforced polymers (CFRPs) are moving beyond exotic applications into practical vacuum cleaner components:
- Short-fiber carbon composites offer improved strength and stiffness compared to unreinforced plastics while remaining injection-moldable, enabling cost-effective mass production of stronger components. These materials typically provide 50-100% strength improvements over standard plastics.
- Continuous fiber composites provide exceptional strength-to-weight ratios for structural components, enabling designs that are simultaneously lighter and more durable than metal alternatives. These materials are particularly valuable in cordless models where weight directly impacts usability.
- Hybrid carbon-glass composites balance performance and cost, using carbon fiber for directional strength and glass fiber for economic fill, creating affordable high-performance materials. This approach can reduce cost by 30-40% compared to all-carbon composites while maintaining 80-90% of the performance benefits.
A major Asian manufacturer has developed a carbon composite vacuum frame that reduced weight by 22% while improving drop resistance by 45%—a compelling combination for portable vacuum cleaners.
Glass-Reinforced Composites for Structural Integrity
Glass fiber remains the workhorse of composite materials, offering substantial performance improvements at modest cost increases:
- Long-glass-fiber thermoplastics (LGFT) incorporate fibers 10-25mm in length, creating a structural network within components that dramatically improves impact resistance and long-term durability. These materials can absorb 3-5 times more impact energy than short-fiber composites.
- Woven glass prepregs provide exceptional flatness and dimensional stability for large panels and housings, preventing the warping and distortion that leads to poor fits and eventual failure. These materials maintain their shape even after years of thermal cycling.
- Glass-reinforced engineering polymers combine high-performance resins (like polyetherimide or polyphenylene sulfide) with glass reinforcement, creating materials that withstand the intense conditions near vacuum motors. These composites can maintain their properties at continuous operating temperatures of 180-220°C.
These materials often replace die-cast metals, offering similar strength with reduced weight and greater design flexibility at competitive costs.
Revolutionary Coating Technologies
Surface coatings represent some of the most dramatic advancements in vacuum cleaner durability, transforming the performance of existing materials without requiring wholesale material changes.
Diamond-Like Carbon Coatings for Wear Resistance
Diamond-like carbon (DLC) coatings are creating nearly indestructible surfaces on critical components:
- Hydrogen-free tetrahedral amorphous carbon (ta-C) provides hardness approaching that of natural diamond (up to 80 GPa) with excellent adhesion to metal substrates. This coating can extend the life of rotating components by 5-10 times compared to uncoated versions.
- Metal-doped DLC variants incorporate elements like tungsten or chromium to enhance specific properties like corrosion resistance or electrical conductivity while maintaining exceptional hardness. These specialized coatings can be optimized for specific operating environments.
- Gradient-layer DLC systems transition gradually from substrate to coating, eliminating the sharp interface that can lead to delamination under stress. This approach creates coatings that remain intact even under extreme impact or deformation.
The microscopic thinness of these coatings (typically 1-3 micrometers) means they add virtually no weight or dimensional change while dramatically extending component life.
Hydrophobic and Oleophobic Surface Treatments
Next-generation surface treatments are creating components that actively repel dust and debris:
- Fluoropolymer nanocoatings create extremely low surface energy, causing both water and oil-based contaminants to bead up and roll off instead of adhering. These coatings can maintain clean surfaces with minimal maintenance, reducing wear from abrasive particles.
- Structured silica coatings create microscopic surface textures that trap air layers, dramatically reducing contact between liquids and the surface. This “lotus effect” mimics the self-cleaning properties of lotus leaves in nature.
- Sol-gel derived hybrid coatings combine organic and inorganic components at the molecular level, creating durable treatments that can be applied to virtually any substrate. These versatile coatings can be formulated for specific dirt-shedding properties.
In vacuum pathways, these coatings reduce clogging and pressure drop over time, maintaining peak performance throughout the appliance’s lifespan. One manufacturer reported 38% less airflow reduction after 500 hours of operation in units with hydrophobic-coated air paths.
Antimicrobial Coatings for Hygienic Operation
Hygiene concerns are driving the development of surfaces that resist microbial growth:
- Silver nanoparticle coatings provide continuous antimicrobial action through the slow release of silver ions, preventing biofilm formation on damp surfaces like water separation systems. Unlike temporary treatments, these coatings remain effective for the life of the component.
- Copper alloy surfaces exploit copper’s natural antimicrobial properties to create self-sanitizing components, particularly valuable in vacuum filters and collection systems. Studies show these surfaces can reduce bacterial contamination by 99.9% within two hours of exposure.
- Photocatalytic titanium dioxide creates surfaces that actively break down organic contaminants when exposed to light, cleaning themselves between uses. This technology is particularly valuable for external surfaces that users frequently touch.
These coatings address growing consumer concerns about household hygiene while preventing the odors and performance degradation associated with microbial growth in vacuum systems.
Specialized Materials for Motor and Electrical Components
The motor system represents one of the most demanding environments in a vacuum cleaner, with high temperatures, rapid motion, and intense electromagnetic fields. Specialized materials are transforming reliability in this critical area.
Next-Generation Motor Magnets
Motor performance depends heavily on magnet quality, and recent advancements are enabling smaller, more powerful, and more efficient motors:
- Neodymium-iron-boron magnets with heavy rare earth additions provide exceptional magnetic strength at higher operating temperatures, enabling motors that maintain performance even under heavy loads. These advanced formulations can operate reliably at temperatures up to 180°C compared to 80-100°C for standard neodymium magnets.
- Samarium-cobalt magnets with optimized microstructures offer slightly lower magnetic strength but superior temperature stability and corrosion resistance, ideal for humid environments. These magnets show virtually no performance loss after years of operation in challenging conditions.
- Nanocomposite magnetic materials combine hard and soft magnetic phases at the nanoscale, creating magnets with enhanced temperature stability and improved energy product. Research samples have demonstrated up to 30% more magnetic energy than conventional single-phase magnets.
These advanced magnets enable motors that are simultaneously more powerful, more efficient, and more reliable than previous generations.
Advanced Insulation Materials
Electrical insulation failure is a common cause of motor burnout, and new materials are dramatically extending insulation life:
- Polyetherimide (PEI) and polyamideimide (PAI) wire coatings provide exceptional heat resistance (up to 240°C continuous operation) while remaining flexible and resistant to mechanical damage. These high-performance insulations can withstand thousands of hours at temperatures that would quickly degrade conventional materials.
- Ceramic-filled silicone compounds combine flexibility with remarkable temperature resistance, creating wire harnesses and connectors that maintain their properties even near hot motor components. These materials can briefly withstand direct exposure to temperatures over 300°C without degradation.
- Vacuum-pressure-impregnated (VPI) systems use specialized resins that penetrate deep into motor windings, eliminating air voids that can lead to insulation breakdown. This process creates a monolithic insulation structure that resists moisture, chemicals, and thermal cycling.
These materials transform motor reliability, often extending useful life from 1,000-2,000 hours to 10,000 hours or more—potentially outlasting every other component in the vacuum cleaner.
Heat-Resistant Compounds for Prolonged Motor Life
Heat management is critical for motor longevity, and specialized materials are improving thermal performance:
- Metal-matrix composite heat sinks combine aluminum with silicon carbide or graphite particles, creating structures with exceptional thermal conductivity and reduced weight. These advanced heat sinks can improve heat dissipation by 30-50% compared to pure aluminum versions.
- Phase-change thermal interface materials remain solid at room temperature but melt slightly during operation, filling microscopic gaps between heat-generating components and heat sinks. This creates perfect thermal contact without the degradation issues of traditional thermal greases.
- Graphite heat spreaders utilize graphite’s anisotropic thermal properties to efficiently move heat away from hot spots to larger dissipation surfaces. These flexible sheets can be just 0.2mm thick yet spread heat more effectively than much thicker metal components.
A prominent cordless vacuum manufacturer recently credited advanced thermal materials with enabling their latest motor to operate at 125,000 RPM continuously without overheating—a 40% increase over previous generations with the same physical size.
Filtration System Material Innovations
Filtration represents a unique materials challenge, requiring both fine particle capture and minimal airflow resistance over thousands of cleaning cycles.
Nanofiber Filter Materials
Nanofiber technology is revolutionizing filter performance and durability:
- Electrospun polymer nanofibers create filter media with fibers as small as 100-500 nanometers in diameter (compared to 10-25 micrometers for conventional fibers). These ultra-fine fibers can capture particles as small as 0.3 micrometers with minimal airflow restriction.
- Multi-layer gradient density structures combine different nanofiber layers to capture progressively smaller particles as air moves through the filter. This approach maximizes particle capture while minimizing pressure drop across the filter.
- Permanently charged electret nanofibers combine mechanical filtration with electrostatic attraction, capturing particles far smaller than the gaps between fibers. Unlike conventional electret filters that lose their charge over time, these advanced materials maintain their electrostatic properties for the life of the filter.
These technologies enable filters that capture more particles while lasting 3-5 times longer than conventional media, dramatically reducing replacement costs and improving sustainability.
HEPA Filter Advancements
High-Efficiency Particulate Air (HEPA) filtration is being reinvented with new materials and structures:
- Pleated composite HEPA media combines multiple materials in a single filter structure, with each layer optimized for specific particle sizes or chemical contaminants. These sophisticated filters can simultaneously address particulates, odors, and gaseous pollutants.
- Hydrophobic HEPA treatments prevent moisture absorption that can lead to mold growth and reduced airflow. These treatments maintain filter performance even in humid environments where conventional HEPA filters quickly degrade.
- Regenerable ceramic HEPA filters can withstand high-temperature cleaning, allowing them to be restored to like-new condition rather than replaced. While more expensive initially, these filters can be reused dozens of times, dramatically reducing lifetime costs.
These advancements address the traditional limitations of HEPA filtration: high cost, frequent replacement, and performance degradation over time.
Washable and Self-Cleaning Filter Technologies
Perhaps the most dramatic filter innovations involve materials designed for extended use without replacement:
- Hydrophilic polytetrafluoroethylene (PTFE) membranes retain their structure even when completely saturated with water, allowing thorough washing without degrading filter performance. Unlike conventional washable filters that lose efficiency with each cleaning, these materials maintain consistent performance through hundreds of wash cycles.
- Lotus-effect nanostructured surfaces create microscopic surface patterns that prevent dust particles from adhering strongly to filter media, allowing them to be removed with minimal water or mechanical action. These self-cleaning properties extend filter life while maintaining high efficiency.
- Vibration-responsive filter frames incorporate piezoelectric elements that vibrate at specific frequencies when activated, dislodging accumulated particles without removing the filter. This technology enables “set and forget” filtration systems that maintain performance with minimal user intervention.
A European manufacturer has demonstrated a prototype vacuum with a filter system that maintains 99% of its original efficiency after 1,000 hours of operation with only occasional automatic self-cleaning cycles—a dramatic improvement over conventional filters that typically lose 30-50% efficiency in the same timeframe.
Emerging Materials on the Research Horizon
Beyond the materials already entering production, research laboratories are developing even more transformative compounds that may appear in vacuum cleaners within the next 5-10 years.
Graphene Applications
The much-heralded “wonder material” is finally finding practical applications in consumer products:
- Graphene-enhanced composites incorporate graphene platelets or sheets into polymer matrices, creating materials with extraordinary strength, electrical conductivity, and thermal performance. Even at concentrations below 1%, graphene can transform polymer properties, improving strength by 30-40% while making the material electrically conductive.
- Graphene foam structures utilize graphene’s 2D nature to create 3D networks with extraordinary strength-to-weight ratios and excellent energy absorption. These materials could create impact-resistant housings that are simultaneously lighter and stronger than anything currently available.
- Graphene coatings can be applied to existing components, dramatically improving surface properties like wear resistance, corrosion protection, and electrical conductivity. At just a few atoms thick, these coatings add virtually no weight or dimensional change.
While still expensive for mass production, graphene costs are falling rapidly as manufacturing scales up, potentially making these applications economically viable within a few years.
Metamaterials with Customized Physical Properties
Metamaterials—engineered structures with properties not found in nature—are moving from theoretical curiosities to practical applications:
- Acoustic metamaterials can selectively block specific sound frequencies while allowing others to pass, potentially creating vacuum cleaners that filter out motor noise while allowing users to hear phones or doorbells. These materials manipulate sound waves through precise structural arrangements rather than mass or absorption, enabling lightweight yet effective noise control.
- Mechanical metamaterials exhibit counterintuitive properties like negative Poisson’s ratio (expanding laterally when stretched) or programmable stiffness, enabling components that adapt to different operating conditions. These materials derive their unusual properties from their geometric structure rather than chemical composition.
- Thermal metamaterials can direct heat flow along specific pathways, potentially solving hot spot problems in compact vacuum designs. By controlling heat distribution, these materials could enable smaller, more powerful motors without overheating concerns.
While complex to manufacture, metamaterials often use conventional base materials in novel arrangements, making them potentially cost-effective once manufacturing processes are optimized.
Biomimetic Materials
Nature has spent billions of years perfecting material solutions, and researchers are increasingly turning to biological systems for inspiration:
- Lotus-inspired self-cleaning surfaces mimic the microscopic texture of lotus leaves, creating components that shed dust and liquids without active cleaning. These surfaces maintain their cleanliness through structural features rather than chemical treatments that can wear off.
- Mussel-inspired adhesives adapt the chemistry that allows mussels to stick to rocks underwater, creating humidity-resistant bonds for vacuum components. These adhesives maintain their strength even in damp environments where conventional adhesives fail.
- Abalone-inspired impact-resistant structures mimic the brick-and-mortar arrangement of abalone shells, creating materials that are simultaneously hard and tough. These sophisticated structures can absorb impacts that would crack conventional materials, ideal for vacuum components subject to drops and collisions.
Biomimetic approaches often achieve extraordinary performance with relatively simple chemistry, making them promising candidates for mass production once manufacturing processes are established.
Implementation Challenges and Solutions
Translating material innovations from laboratory to mass production presents significant challenges that manufacturers must overcome.
Manufacturing Adaptations
Advanced materials often require new processing approaches:
- Injection molding parameter optimization for high-performance polymers often requires significantly different temperatures, pressures, and cooling rates compared to conventional plastics. Equipment upgrades and extensive process development may be necessary to achieve consistent quality. For example, processing temperatures for polyetherimide can exceed 350°C, beyond the capabilities of many standard molding machines.
- Composite manufacturing scale-up presents challenges in maintaining fiber alignment, void content, and consistent material properties in high-volume production. Automated fiber placement technologies and specialized molding techniques are being adapted from aerospace applications to consumer products.
- Surface treatment integration into existing production lines requires careful process engineering to ensure consistent application without disrupting throughput. Many advanced coatings require controlled environments or specialized application equipment that must be incorporated into production flows.
Manufacturers are addressing these challenges through strategic partnerships with material suppliers and equipment manufacturers. Several leading vacuum brands have established dedicated advanced materials engineering teams focused specifically on manufacturing process development.
Cost Considerations and Economies of Scale
Advanced materials typically come with higher raw material costs, requiring careful economic analysis:
- Initial cost premiums for high-performance materials can range from 2× to 10× compared to conventional alternatives. For example, a standard ABS housing might cost $1.50 in materials, while a high-performance polymer version could cost $6-$15.
- Total cost of ownership calculations often demonstrate that higher material costs are offset by extended product life, reduced warranty claims, and premium pricing opportunities. Forward-thinking manufacturers are developing sophisticated models that account for these factors in material selection decisions.
- Scale effects on pricing are beginning to reduce cost barriers as adoption increases. Materials that were prohibitively expensive five years ago have seen cost reductions of 30-50% as production volumes increase and manufacturing processes mature.
One manufacturer reported that switching to an advanced polymer for a critical component increased material costs by $4.20 per unit but reduced warranty claims by 62%, resulting in net savings of $7.80 per unit when accounting for all costs.
Testing and Validation Methodologies
New materials require new testing approaches to verify performance and durability:
- Accelerated aging protocols are being developed to predict long-term durability in months rather than years of testing. These protocols combine elevated temperatures, humidity cycling, UV exposure, and mechanical stress to simulate extended use in compressed timeframes.
- Digital twin simulations use advanced computational models to predict material behavior under complex real-world conditions. By combining material science with high-performance computing, these approaches can identify potential failure modes before physical prototypes are built.
- Field testing programs are expanding to capture real-world performance data across diverse environments. Some manufacturers are deploying small batches of experimental models to commercial cleaning companies, where they accumulate thousands of hours of use in months rather than years.
These methodologies are reducing development cycles for new materials from 3-5 years to 12-18 months, accelerating the pace of innovation throughout the industry.
Environmental Impact and Sustainability Considerations
Advanced materials must not only perform better but also support broader sustainability goals—an increasingly important factor for both consumers and regulators.
Lifecycle Assessment of New Materials
Manufacturers are taking a more holistic view of material environmental impact:
- Cradle-to-grave analysis examines environmental impacts from raw material extraction through manufacturing, use, and end-of-life disposal. This comprehensive approach prevents “burden shifting,” where solving one environmental problem creates another.
- Energy intensity comparisons evaluate the total energy required to produce and process materials throughout their lifecycle. Some advanced materials have higher manufacturing energy requirements but save energy during use through lighter weight or improved efficiency.
- Carbon footprint calculations are becoming standard practice in material selection, with some manufacturers setting specific carbon reduction targets for new product development. These targets are driving interest in bio-based and recycled content materials.
A recent industry study found that vacuum cleaners using advanced durable materials had 28% lower lifetime carbon footprints compared to conventional models, despite higher manufacturing impacts, due to their extended useful life.
Recyclability and End-of-Life Considerations
Material innovations are addressing end-of-life challenges:
- Design for disassembly approaches are being integrated with material selection to ensure that valuable or potentially harmful materials can be easily recovered at end-of-life. This includes using compatible materials, minimizing adhesives, and implementing snap-fit designs.
- Chemical recycling technologies are emerging for high-performance polymers that cannot be effectively recycled through mechanical methods. These processes break polymers down to their chemical building blocks, allowing them to be reconstituted into virgin-quality materials.
- Marking and identification systems for advanced materials ensure that recycling facilities can properly sort and process these compounds. Some manufacturers are implementing digital material passports that provide detailed composition information throughout the product lifecycle.
These approaches are transforming vacuum cleaners from disposable appliances into valuable material banks that can be mined for future products.
Reduction of Harmful Substances
Advanced materials are enabling the elimination of problematic compounds:
- Halogen-free flame retardants are replacing brominated compounds in plastic housings and electrical components, reducing persistent environmental contaminants. New mineral-based and phosphorus flame retardant systems provide comparable fire safety with improved environmental profiles.
- Heavy metal elimination in pigments, stabilizers, and electrical components reduces toxic exposure during manufacturing and potential environmental contamination at end-of-life. For example, bismuth-based stabilizers are replacing lead compounds in PVC components.
- Low-VOC alternatives for adhesives, coatings, and processing aids improve indoor air quality during manufacturing and product use. Water-based and UV-curable systems are replacing solvent-based formulations throughout vacuum cleaner production.
One manufacturer has achieved a 94% reduction in substances of very high concern (SVHCs) through systematic material substitution, improving worker safety and reducing environmental liability.
Industry Case Studies: Material Success Stories
Leading manufacturers are already implementing advanced materials with impressive results.
Brand Examples of Successful Material Upgrades
Several companies are showcasing the benefits of material innovation:
- Dyson’s implementation of glass-filled polyphenylene sulfide (PPS) in cyclone assemblies has dramatically improved thermal stability and dimensional accuracy. This material maintains precise airflow pathways even after thousands of hours of operation at elevated temperatures, preserving cleaning efficiency throughout the product’s life.
- Miele’s utilization of diamond-like carbon coatings on critical wear surfaces has extended the lifetime of their commercial vacuum models by over 300%. These nearly invisible coatings add minimal cost while dramatically reducing friction and wear in high-stress components.
- Electrolux’s introduction of self-healing polymers in external housings has significantly reduced cosmetic damage that leads to premature replacement. Their proprietary polymer blend can recover from scratches and minor dents within 24 hours at room temperature, maintaining aesthetic appeal throughout the product’s functional life.
These examples demonstrate how material innovations are becoming key differentiators in the competitive vacuum cleaner market.
Performance Improvements Quantified
The performance benefits of advanced materials are substantial and measurable:
- Extended service life is the most direct benefit, with advanced materials increasing average product lifespan by 40-120% in field tests. Some commercial models using comprehensive material upgrades have demonstrated useful lives exceeding 5,000 operating hours—more than double the industry standard.
- Reduced maintenance requirements translate directly to improved user experience and lower lifetime costs. Advanced filtration materials have extended the time between filter cleanings by 200-300%, significantly reducing the maintenance burden on users.
- Improved energy efficiency results from better thermal management and reduced friction in key components. One manufacturer reported a 14% reduction in energy consumption after implementing advanced bearing materials and low-friction coatings in their motor assembly.
These quantifiable benefits provide compelling evidence for the value of material innovation, even when associated with higher initial product costs.
Cost-Benefit Analysis of Material Investments
The economics of advanced materials increasingly favor adoption:
- Premium pricing opportunities allow manufacturers to recover higher material costs while maintaining or improving margins. Market research indicates that consumers are willing to pay 15-25% more for products with demonstrated durability advantages.
- Warranty cost reductions directly impact profitability, with several manufacturers reporting 30-60% decreases in warranty claims after implementing advanced materials in critical components. These savings often exceed the additional material costs within 12-18 months.
- Brand reputation benefits are harder to quantify but potentially more valuable than direct cost savings. Manufacturers who establish reputations for exceptional durability can command price premiums across their entire product line, not just on models with specific material upgrades.
A detailed industry analysis demonstrated that a $12 million investment in advanced material implementation returned approximately $47 million in combined cost savings and revenue enhancements over a five-year period—a compelling business case by any standard.
Future Outlook: The Next Decade of Material Advancements
Looking ahead, several key trends will shape the future of vacuum cleaner materials.
Prediction of Key Material Trends
Industry experts anticipate several important developments:
- Bio-based high-performance polymers will increasingly replace petroleum-derived plastics, offering similar or superior properties with improved sustainability. Polymers derived from algae, agricultural waste, and atmospheric carbon dioxide are already entering commercial development.
- Multi-functional materials that combine structural, thermal, electrical, and aesthetic properties will reduce part counts and assembly complexity. For example, thermally conductive polymers that eliminate the need for separate heat sinks while providing structural support.
- Additive manufacturing-specific materials designed for 3D printing will enable on-demand production of complex replacement parts, extending product lifespans through improved repairability. These materials combine printability with mechanical properties approaching those of injection-molded components.
These trends point toward vacuum cleaners that are simultaneously more durable, more sustainable, and more repairable than today’s models.
Timeline for Commercial Implementation
The path from laboratory to living room follows predictable patterns:
- Near-term implementations (1-2 years) will focus on coating technologies, surface treatments, and drop-in material substitutions that don’t require significant manufacturing changes. These approaches offer the quickest path to improved durability.
- Medium-term adoptions (3-5 years) will include more substantial material changes requiring manufacturing process adjustments, such as advanced composites, self-healing polymers, and specialized alloys for critical components.
- Long-term transformations (6-10 years) will involve fundamental redesigns that fully exploit the properties of next-generation materials, potentially reinventing the basic architecture of vacuum cleaners. These designs will likely incorporate materials still in research laboratories today.
This staged implementation allows manufacturers to balance innovation with practical business constraints while steadily improving product performance.
Potential Disruptive Technologies
Several emerging technologies could fundamentally change vacuum cleaner design:
- Structural battery materials that simultaneously store energy and provide mechanical support could transform cordless vacuum design, eliminating the distinction between “battery” and “structure.” This approach could increase energy density while reducing weight and improving durability.
- Programmable materials that change properties in response to external stimuli could create vacuum components that adapt to different operating conditions. For example, air channels that automatically reconfigure for different floor types or cleaning modes.
- Self-assembling nanostructures could enable new manufacturing approaches where material properties are determined by molecular-scale arrangements rather than bulk composition. These technologies could dramatically reduce material and energy requirements while improving performance.
While speculative, these technologies represent the cutting edge of material science research, with potential applications extending far beyond vacuum cleaners.
Conclusion
The humble vacuum cleaner stands on the verge of a material revolution. From self-healing polymers to atomic-scale coatings, advanced materials are transforming what’s possible in terms of durability, performance, and sustainability.
For manufacturers, these innovations represent both challenge and opportunity. Those who successfully implement advanced materials can differentiate their products in a crowded market, command premium prices, and build reputations for exceptional quality. However, doing so requires investment in new expertise, manufacturing capabilities, and testing methodologies.
For consumers, the benefits are more straightforward: vacuum cleaners that last longer, perform better, and ultimately provide greater value. While advanced materials may increase initial purchase prices, the extended lifespan and improved performance more than compensate in the long run.
Perhaps most importantly, these material innovations represent a shift away from the disposable mentality that has dominated consumer products for decades. By creating vacuum cleaners designed to last, manufacturers are aligning their business interests with environmental sustainability—a rare win-win scenario in today’s complex marketplace.
As this material revolution gains momentum, we can expect vacuum cleaners to become increasingly durable, efficient, and sustainable. The compounds emerging from research laboratories today will shape the cleaning tools in our homes for decades to come—transforming not just how we clean, but how we think about the longevity and value of household appliances.